|
Chris Johnson
 Advanced Member
 Posts:877
 |
16 Jun 2013 09:41 AM |
|
And to add to TexasICF statement, vertical ICF systems along with about 40+ odd other ICF systems, they seem to only capture a localized area. Only a handful of ICF are nation wide or even worldwide. |
|
Chris Johnson - Pro ICF<br>North of 49 |
|
|
sailawayrb
 Veteran Member
 Posts:2274
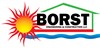
 |
16 Jun 2013 12:44 PM |
|
Right, that's exactly what I stated and precisely my point. ICF product availability and contractor experience with a given product is still very localized and often highly monopolized to the detriment of the consumer. This is one the reasons that the installed cost of ICF construction for an identical building plan in different localities can vary by nearly an order of magnitude. Vertical ICF already dominates the few local markets where it is available, but vertical ICF currently has very limited availability unless you are willing to pay the additional shipping cost which can be as much as the product cost...although this can still end up being lower cost than using some block ICF systems. From our experience, vertical ICF is by far a preferable product with regard to design flexibility and construction cost and, as such, we expect it will ultimately dominate all markets eventually. The only question in our mind is whether this dominance will be accomplished by the few existing vertical ICF companies successfully expanding their territory or by the some of the existing ICF block companies eventually switching to vertical ICF after expiration of patents held by the existing vertical ICF companies. |
|
Borst Engineering & Construction LLC - Competence, Integrity and Professionalism are integral to all that we do! |
|
|
Midsouth ICF
 New Member
 Posts:65
 |
16 Jun 2013 02:27 PM |
|
I would also agree, let the installer decide. they will have their favorite that they can rock and roll with and save you time and money. |
|
Ryan Gunn Owner, Midsouth ICF Builders LLC |
|
|
jperiod
 New Member
 Posts:21
 |
16 Jun 2013 04:32 PM |
|
A disadvantage of installers having favorite ICF block is that it could minimize the options available to a potential customer. For example, if a customer wants higher insulation value (i.e. R30) that are available from some ICF products , if the local installer's favorite does not provide this higher insulation value your may be SOL. Compare this with a stick builder who builds with 2x 4 studs, if the customer wants 2x 6 walls with higher insulation,he just buys 2x 6 instead of 2x4s and its no problem. I think that in order to get higher acceptance the iCF industry needs to have this kind of flexibility. |
|
|
|
|
Midsouth ICF
 New Member
 Posts:65
 |
16 Jun 2013 04:39 PM |
|
How about Fox Blocks? I have used most block and I prefer Fox. I trust it and it is very versatile. However, each installer prefers a certain block and the homeowner will benefit from an installer that trusts and knows his respective block. |
|
Ryan Gunn Owner, Midsouth ICF Builders LLC |
|
|
BrucePolycrete
 Advanced Member
 Posts:524
 |
16 Jun 2013 06:33 PM |
|
If you're thinking about using a vertical product, take a close look at the code compliance. You may be surprised to learn that some vertical "ICF" systems that market most aggressively do not meet the International Code Council's minimum requirements for insulated concrete forms or those of ASTM E-2634. |
|
|
|
|
sailawayrb
 Veteran Member
 Posts:2274
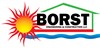
 |
16 Jun 2013 10:15 PM |
|
No, actually I would not be surprised that some vertical ICF systems do not meet ASTM E-2634. I would be more surprised if any vertical ICF systems actually meet ASTM E-2634...along with some block ICF systems that are out there too. As stated in scope section 1.2 of ASTM E-2634, "products covered by the specification consist of molded expanded polystyrene (EPS) insulation panels that are connected by cross ties to form the ICF system." Vertical ICF systems don't use or depend on cross ties to maintain structural integrity during the pour and it would seem to me that ASTM E-2634 would not be applicable to vertical ICF systems. Vertical ICF systems use continuous rails that can often handle full 12' lifts and don't often exhibit the wavy wall issues resulting from horizontally seamed EPS cross tie induced float or settling like block ICF systems have always struggled with. ASTM writes material testing standards and often lags keeping up with new material and product developments. No matter what ICF system is used, we would be much more concerned that it meets the applicable engineering structural design codes for the specific location. |
|
Borst Engineering & Construction LLC - Competence, Integrity and Professionalism are integral to all that we do! |
|
|
Lbear
 Veteran Member
 Posts:2740
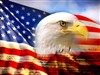
 |
17 Jun 2013 01:35 AM |
|
I don't see block systems becoming obsolete anytime soon by vertical systems. If it did happen, it would be like 10-15 years before they would become mainstream, the big emphasis on "if". As TexasICF mentioned, the current blocks are used in millions of square feet of builds. The vertical systems are very scarce when compared to the standard block system.
I can maybe see the manufacturers testing the market and maybe offering BOTH systems and if they verticals took off, they might switch over but that would be a long time. ICF when compared to residential wood frame is pretty rare. For every 1,000 wood frame homes that go up, how many ICF homes go up? Out here in my neck of the woods I would safely estimate that for every 1,000 wood homes, 10 ICF homes go up. So around 1%. Other states have more ICF builds but out here they are rare.
|
|
|
|
|
BrucePolycrete
 Advanced Member
 Posts:524
 |
17 Jun 2013 06:14 AM |
|
@Sailawayrb, ASTM and ICC-ES define and certify minimum standards for safety and performance. In my opinion, the bar they set is not high enough, but many vertical systems do not meet those minimum standards.There is also the issue of thermal bridging. The "rail" configuration causes a thermal superhighway with heat and cold traveling back and forth freely. Additional measures required to reduce that problem can be costly and time consuming. |
|
|
|
|
smartwall
 Veteran Member
 Posts:1197
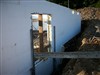
 |
17 Jun 2013 04:06 PM |
|
Bruce, for somone who sells a 32 lb form the make up of which is maybe 2/3 steel, thou should not cast stones. I believe the TF system uses recycled poly in it's rails that can be buried inside as much foam as you would choose to buy. |
|
|
|
|
BrucePolycrete
 Advanced Member
 Posts:524
 |
17 Jun 2013 04:20 PM |
|
Thanks Smartwall, You are correct that the Big Block contains 66% steel by weight and it's recycled steel. It is a VERY strong ICF that will not bulge, scallop or blow out. You continue to make my other points for me as well. You must buy additional foam to solve that thermal bridging problem on the vertical system.Then you have to install it -- or mess around with the EIFS panel. But how do you solve the problem that the system does not meet the minimum ICC requirements? |
|
|
|
|
sailawayrb
 Veteran Member
 Posts:2274
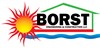
 |
17 Jun 2013 07:15 PM |
|
Lbear, your 10-15 year forecast sounds about right to me...assuming it will be the existing block ICF companies switching to vertical ICF that will actually increase availability and NOT the existing vertical ICF companies successfully expanding their territory. I believe the vertical ICF system design patents were granted in 2011 and design patents expire after 14 years. So the existing block companies should be able to get into the vertical ICF game about 12 years from now or in 2025. I wish that we could wait that long for vertical ICF availability to improve, but the passive solar and hydronic radiant floor integrated building designs that we specialize in greatly benefit from the vertical ICF advantages. Bruce, having recently trained on the TF Systems vertical ICF, I don't see how their thermal bridging could be any worse than block ICF systems? Any thermal bridging effect on thermo performance should be included in the whole wall R-value. The standard TF Systems vertical ICF with 2.5" EPS, 6" core, and 2.5" EPS has a whole wall R-value of 25.17. TF Systems doesn't play games by mixing R-value and thermal mass effects to claim a higher R-value like some companies do. TF Systems even allows you to put as much as 12" of EPS on one side of the core and 0" on the other side (or 12" on both sides) if you so desire. I am not of aware any contractors needing to do remedial work to address a thermo performance with any vertical ICF system. Do you have definitive data/reports that you can share on this? Bruce, I would agree ASTM E-2634 is intended to address product safety. However, the safety issue that is addressed is in regard to the initial form structural integrity to allow safely pouring the walls and NOT the final structural integrity. While initial form structural integrity is certainly something that us contractors need to worry about, us engineers and home buyers should be more concerned about meeting the applicable final structural integrity requirements for the specific building location. The final structural integrity largely depends on the concrete strength/thickness and the rebar schedule (or Helix dose) used. You can remove the EPS forms from all ICF systems after the concrete cures and the final structural integrity is solely governed by the reinforced concrete core and it will be exactly the same with or without the EPS forms in place. ASTM E-2634 doesn't even attempt to address concrete strength and rebar schedule...or meeting the applicable structural requirements for the specific building location such as wind and seismic loads. Bruce, I don't recall that ASTM E-2634 even addresses ICF performance? I am going from recollection here as I am currently on location and I don't have this spec handy, but I thought it only covered basic EPS properties (e.g., density, surface burning characteristics, etc) and quality assurance stuff...and not thermo performance. In any event, we are only talking about EPS and reinforced concrete here. So we really only need to know the correct whole wall R-value and have the knowledge to work out the thermal mass performance to allow us to meet all our design objectives. Smartwell, you are correct that TF Systems uses recycled products. They have been involved with a couple LEED Gold projects. They are also involved with the Pensmore project which is designed to be a tornado-proof 70,000 SF residence using their 12" concrete core vertical ICF and ballistic-proof windows. I also agree with you that a 66% steel block would make a strong ICF form, but would significantly and adversely affect thermo performance too. Sounds "old school" to me and most ICF companies with residential products have learned to use recycled plastic, properly consider thermo performance, and only make the form strong enough to ensure that the pour can be safely and confidently accomplished. As mentioned previously, some TF Systems vertical ICF products can be poured to full 12' lifts with minimal vibration required to achieve proper consolidation. So initial form structural integrity should not be a concern for this product. I have attached photos showing some of the TF Systems product options from when I took their training a couple months ago. We don't have any affiliation with TF Systems (or any other ICF company) and we believe anyone making comments on this forum about various companies or products should also always fully disclose if they have an affiliation with a specific company or product.
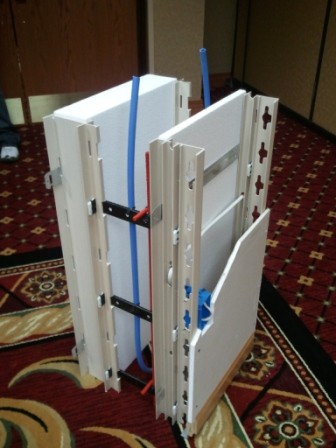 |
|
Borst Engineering & Construction LLC - Competence, Integrity and Professionalism are integral to all that we do! |
|
|
BrucePolycrete
 Advanced Member
 Posts:524
 |
17 Jun 2013 08:43 PM |
|
What is the compressive and flexural strength of their EPS? What is the fire rating on the wall system? What are the result of the fastener withdrawal and shear tests? There aren't any. The system does not meet ICC code.The panels, alone have burn tests and they are approved for exterior perimeter insulation only according to the information the company gave to our client when he inquired. Look up ICC-ESR 1006. Read the NY Times article on Pensmore and pay particular attention to the part where they say building codes and inspections would "complicate" the project. http://www.nytimes.com/2011/07/19/us/19ozarks.html?_r=3&partner=rss&emc=rss&
If I'm wrong, someone send me the test results. Lastly, on the steel in Polycrete, it's in the form of a .16" welded wire mesh that is inside the EPS panel. Rather than "old school" it's the future of commercial grade ICF. |
|
|
|
|
Lbear
 Veteran Member
 Posts:2740
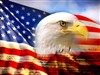
 |
18 Jun 2013 02:41 AM |
|
Posted By sailawayrb on 17 Jun 2013 07:15 PM
I can spot bad hotel carpeting from a mile away. Let me guess, Ramada Inn? I'm in the hotel biz and I've seen my share of hotel carpeting. |
|
|
|
|
arkie6
 Veteran Member
 Posts:1453
 |
18 Jun 2013 07:21 AM |
|
Those TF samples above look like expensive solutions looking for a problem. Radiant tubes in the wall? Why? |
|
|
|
|
Bob
 New Member
 Posts:7
 |
18 Jun 2013 09:11 AM |
|
Lbear said RE above post: "I can spot bad hotel carpeting from a mile away. Let me guess, Ramada Inn? I'm in the hotel biz and I've seen my share of hotel carpeting". MY guess, could be Residence Inn? Whoever took the picture, come clean - what hotel?? I am so glad to see this Forum pick back up since I did a random post on 14 Jun 2013 10:25 AM. Last post above mine was on 07 Nov 2008 11:48 AM from ph3nom3nallICF. Regards from no dog in the fight, RL |
|
|
|
|
sailawayrb
 Veteran Member
 Posts:2274
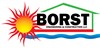
 |
18 Jun 2013 07:57 PM |
|
Lbear, great eye, but this was NOT a Ramada Inn (or a Residence Inn either Bob)...although I would certainly agree those would usually be very safe bets... These photos were from the location at which a TF Systems contractor training session was conducted a couple months ago in Green Bay, WI and at this resort: Tundra Lodge And the carpet installation was the least of issues associated with this building. In fact, this was one of the most poorly designed and constructed buildings that we had seen in quite a while. We actually commented about this and were told that the building had to be rehabilitated a year after opening because of overwhelming guest complaints about room to room noise. I believe they replaced all the original interior walls with QuietRock and moved the original back-to-back electrical outlets to non-adjacent locations. I don't know who the original contractor was on this project, but I would be very surprised if they are still in business. And speaking of construction industry best practices... Only a month after more than an estimated 1,100 Bangladeshi garment workers lost their lives in the collapse of a badly-built and poorly-maintained eight-story building, the new building code has thankfully gone into force. Its rigid practices are already being applied by highly-skilled and properly-trained construction teams laboring in harmony on job-sites all across the sub-continent: New Pile Driver Requirements Implemented Arkie, one of the benefits of vertical ICF is that you can leave one side of the wall open and easily place PEX tube (and rebar too). The most obvious reason for placing PEX tube would be for having hydronic radiant wall heating. This is possible because some of the TF Systems products allow the interior side of the concrete to remain exposed (which is also advantageous for active thermal mass passive solar design applications) while the exterior side of the concrete core can be insulated at whatever thickness of EPS is required for the building design. A less obvious reason for placing PEX tube would be to just slightly heat the EPS sandwiched concrete core to essentially increase the effective wall R-value. As we all know, heat loss through a wall component is proportional to the temperature differential across the component. So when you keep the concrete core at a higher temperature than the outside temperature, you will have less heat loss through the wall. The heat source for accomplishing this is typically from a free renewable resource such as solar heat collection or hydroelectric power. Conversely, the PEX tube can also be used to keep the concrete at a lower temperature than the outside temperature to reduce cooling load. However, one needs to fully understand condensation and dew point or this could become very problematic. Clearly, placing PEX tube in ICF walls is more of an energy efficiency design strategy for long-lived commercial and custom residential projects than for disposable tract homes. There are also few existing design/build companies capable of fully taking advantage of this vertical ICF system benefit. Bruce, I suspect that Mr. Huff's pursuit of happiness relative to acquiring/displaying excessive wealth, shunning government regulations, and lack of empathy to his neighbors as highlighted by this New York Times article has much more to do with his political affiliation/philosophy than with his ICF product selection. Nevertheless, he made his fortune in the software business and is likely very intelligent and busy savvy. So I doubt that Mr. Huff would invest an inferior ICF company and product for his 70,000 SF second residence and his next business venture. Every major code body in North America, including ICC and CCMC, has approved the use of TF Systems vertical ICF products. And as most contractors/engineers know, ICFs are also listed as a prescriptive method of building in the International Residential Code and can be built to commercial design specification using the International Building Code. EPS properties for the six types of available EPS can be found here: EPS Properties All reputable ICF companies purchase their EPS from EPS companies that adhere to ASTM-C578 standards and they typically select either Type II or IX for their ICF designs. Both types of EPS will work well in a given ICF design as long as either the block ICF cross tie system or the vertical ICF rail system has been properly designed to handle the weakest type of EPS that will be used in the final product for the highest allowed concrete pour lift specified. Type II EPS has a density, R-value per inch, compressive strength, and flexural strength of 1.35 PCF, 4.76, 15 PSI and 35 PSI, respectively. Type IX EPS has a density, R-value per inch, compressive strength, and flexural strength of 1.80 PCF, 5.00, 25 PSI and 50 PSI, respectively. TF Systems vertical ICF system products are available in both Type II or IX and in whatever EPS thickness the building design requires. However, I suspect that you already know all this and I get the strong impression that your motivation is more about casting doubt and spewing disparaging remarks about superior products that compete with whatever product you are likely affiliated with and reluctant to provide self-disclosure. |
|
Borst Engineering & Construction LLC - Competence, Integrity and Professionalism are integral to all that we do! |
|
|
BrucePolycrete
 Advanced Member
 Posts:524
 |
19 Jun 2013 09:06 AM |
|
Sailaway, you generate a lot of words but there is little evidence to support them so they just sail away into the clouds. You make disparaging remarks about my veracity without knowing anything about me, yet I am very easy to find. Do you know what ICC requirements for ICF are? Show us the evidence that TF meets ICC minimum requirements for insulated concrete forms and we will happily shut up. |
|
|
|
|
FBBP
 Veteran Member
 Posts:1215
 |
19 Jun 2013 12:21 PM |
|
Posted By sailawayrb on 18 Jun 2013 07:57 PM
And speaking of construction industry best practices... Only a month after more than an estimated 1,100 Bangladeshi garment workers lost their lives in the collapse of a badly-built and poorly-maintained eight-story building, the new building code has thankfully gone into force. Its rigid practices are already being applied by highly-skilled and properly-trained construction teams laboring in harmony on job-sites all across the sub-continent: New Pile Driver Requirements Implemented
Such harmony doesn't always exist on North American sites. Neither does the ingenuity. Please note that the holes are predrilled so the columns are only being place. Neat video anyway! |
|
|
|
|
FBBP
 Veteran Member
 Posts:1215
 |
19 Jun 2013 01:32 PM |
|
I don't think we have to worry about the vertical products taken over the market. There is a reason Lego is, well a block. Childs play. Those of us that entered the industry by way of cip walls with vertical forms are not likely to go back. The closer the height of the block is to the the base the more stable the product. With blocks you can go up to your reach height with virtually no bracing. If you are using a quality block that clips together top to bottom and interlock horizontally, your walls will stay put even in quite windy conditions. I can't imagine handling 8" x 8' foam strips in the wind. I would probably only be able to work 10 day out of the month while I wait for the wind to be below 20 K. While there will be some niche markets where it would be advantageous to place the bar after the wall is up, I can't see how dragging the bar through the uprights would be anywhere as quick as just tucking them in the open top of each layer. There is also an advantage to webs that actually grip the bar and hold it in place. I believe in the control of a pro, any of the main stream blocks can be pour 12' of height at a time. Not to sure why you would want to. Even TF manual appears to suggest 4' lifts. I don't see any reason to increase the the insulation beyond 2.5 plus 2.5". That enclosed mass already exceeds the thermal protection of any other component of the house. The funny thing is that the detractors of the ICF have give the manufactures an excuse to up sell the customers on higher foam levels that aren't needed. Just stay with the standard block and invest any extra coin you have in the other components. In spite of their fancy video I fail to see how TF systems can be faster. You have more component parts to deal with, you need to brace as you go, you need to drag the rebar through the wall. On top of that you need to have a trailer load of extra components to install their transform system. Over time these will get covered with slurry and be difficult to deal with. As it is a localized system, I suspect the the distributor will rent you all these pieces but it does remind me of going back to the job to strip the forms and loading all the forms at the end of the job prior to moving to the next. I believe there will be a place for this type of system but I doubt it will ever be main stream. Wether you have to transport your product 100 miles or 1000 the road cost form a surprisingly small part of the cost. Availability has more to do with the acceptance (or lack the of) of the product itself. The is certainly a case for the the small guys not having the advertising budget to expose their product. maybe that is Mr. Huff's problem. Wether a block is cast in the manufacturers facility or a contract facility makes small difference. The contract facilities do nothing else but blow foam. They are experts at making foam products just like concrete precasters are experts at precast. It doesn't matter what product the precaster are casting. Paying for an increase in pull out strength only makes sense if you are going to hang your kitchen cabinets with one screw. Fully load cabinet would seldom reach more than 60 pounds per lineal foot and most cabinets are hung with between 4 and 8 screws. Doesn't take much when you spread the weight over that many screws. If the product is well received in your area and you can talk to installers and homeowners about it, I would take that to heart more then exactly what codes it happened to be tested to. No installer is going to use a product for the long haul that give him problems. Happy installers are much more important then how some company got past a particular code compliance issue. As has been said, after the pour all concrete is the same regardless of what foam it is inside. If anyone is reading this to actual pick a product, I will say what many of the professional installers have already said. Go with the installers preference and where you get support. Beyond that I would look for a block the actively clips together top to bottom. These block do not drift or float. The webs are solid from top to bottom and have very little stretch or compression to them. If your wall is 8' high prior to the pour it will be 8' high after the pour. Also look for block that fully interlocks horizontally. There should be no need for extensive corner bracing etc.. Big blocks tend to go a bit quicker while smaller blocks have some advantage in complicated projects. Steel conducts heat much quicker than plastic so I would avoid any block that has steel in the foam part of the block. Just my thought on the subject.
|
|
|
|
|