pennsyltucky
 New Member
 Posts:1
 |
27 Dec 2009 07:14 PM |
|
Forgive me if this topic has been covered before, but I'm unable to find a clear answer.
How exactly can you incorporate thermal mass into the first floor of a home with a basement. Most plans I've seen omit the basement and use a concrete slab for thermal mass, but I grew up in a home with a basement and would have serious reservations building a home without one. I'm thinking you might be able to get some thermal mass with tile flooring or a couple brick half-walls, but nothing that will compare to a 4" slab. I've seen some nice concrete floors with inset slate to break-up the standard gray monolith, but I haven't seen anyone do that above a basement.
Basically, does anyone have ideas for incorporating thermal mass into a floor above a basement. If it helps, I'm thinking of ICF walls for the basement and SIPs for 1st and 2nd floors.
|
|
|
|
|
|
Jere
 Basic Member
 Posts:106
 |
27 Dec 2009 08:01 PM |
|
You could pour 1.5" thick concrete on top of your subfloor... many people do this that want radiant floor heat. Doing this you may have to install additional bottom plates that is treated lumber, also have your floor system engineered for additional loads.
You could also spray in cellulose in your interior walls for some thermal mass... this is also great for sound deadening. |
|
I built my home with the help of Pierson-Gibbs Homes, "The Hands on House". They build the shell, you finish it.
www.p-ghomes.com |
|
|
ecobuilder
 Basic Member
 Posts:102
 |
27 Dec 2009 11:04 PM |
|
Pennsltucky, This can be done several ways. One is to over size your floor joists and add 1-1/2" of mass as Jere stated, another is to use a floating slab. I think insulsdeck has a product for just that purpose. Insulated panels that form I joists out of the concrete floor and a 2" or 3" slab thickness. This product was used on one project that I completed a couple of years ago and is performing well. The original floor did have some cracks that formed mostly control joints but a few wanderers also. The homeowners put a stamped concrete finish over the slab after it cured properly. This took some time as you really want the concrete to cure well before covering it with anything. The moisture content inside of this ICF house was high for nearly a year after the house was poured and weathertight. The use of an ERV instead of an HRV did not allow for the house to dry out as well as it would have with an HRV. Although HRV's are not designed to control humidity but if used right the can control indoor humidity levels if the right conditions apply. If your house is more humid than the outside air an HRV with bring dryer air into you home. If you use an HRV when the outdoor humidity is higher than your house, then you will be introducing humidity into your home. ERV's are more efficient than HRV's at capturing and saving energy but they also maintain humidity levels and do not allow for dryer air to enter into the home. To solve their problem with the house being to humid they added a dehumidifier to the ERV ventilation system. IMHO this is not a very good combination. As the ERV recirculates the humid air from the house the Dehumidiifier is having to dry this air afterwards. This works in a humid or very humid climate but not in a cold one like MA when we have 10 times the heating load as we do cooling loads and when in heating mode the relative humidity is typically dryer outside allowing for drying to occure through the HRV. On one house I recently finished we used two seperate systems for ventilation and humidity control. I installed a whole house HRV system to handle the ventilation needed for this very tight house. We also installed a whole house dehumidification system as well, for reasons I won't go into here. But the dehumidifier also allowed for fresh air intake and meets the indoor air requirements when it is running. So when we need the house to be less humid, then the ventilation system atached to the dehumidifier will also bring in fresh air and the HRV will not run. Once the house has achieved the proper humidity levels then the Dehumidifier will turn off and the HRV will take over ventilation for the house. Check out the insul-deck product but I am sure there are others as well. Just for your info the engineering for this is going to be more expensive, unless your engineer is familiar with the product. From my experience building officials will want to see engineering done on any floor system like this and will require an engineers stamp of approval. This cost nearly as much as the product itself. Either way you should always incorporate a radiant floor heating system into the concrete. Here is a link to some pictures of the finished product after the homeowners added the stamped cocncrete finish, http://picasaweb.google.com/TomPittsley/PassiveSolarICFSIPSHybrid#5269116191093766194 , http://picasaweb.google.com/TomPittsley/PassiveSolarICFSIPSHybrid#5269116174586609346 Here are some pictures of a stained concrete finish as part of the slab, doesn't look like concrete to me. http://picasaweb.google.com/TomPittsley/PassiveSolarHomeMiddleboroMA#5318105572499696866 , http://picasaweb.google.com/TomPittsley/PassiveSolarHomeMiddleboroMA#5318105560322942514 You can also add tile over the slab if you want to add more mass to the floor. Tom Pittsley [email protected] www.eebt.org |
|
"Don't be afraid to go out on a limb. That's where the fruit is." Jackson Brown |
|
|
Brawler
 Basic Member
 Posts:229
 |
29 Dec 2009 12:07 PM |
|
On my cottage, currently under construction i had the floor enginered for 1.5" concrete with tile over, over 14" open web trusses. We made the spacing 1 foot on center. I'll let you know in a month or so how it goes. |
Attachment: trusses.jpg
|
|
|
|
jdebree
 Basic Member
 Posts:497
 |
29 Dec 2009 04:09 PM |
|
You could just go with a commercial type floor deck. I've seen them used in garages that are over a basement. It's just corrugated metal floor pans over re-bar trusses. Many commercial buildings are built that way due to the required load capability. Where I work, the second floor is rated at 160 lbs/sq/ft. You could easily add radiant heat tubing while building it. I can see where the humidity would be a problem until it all worked it's way out of the slab. |
|
|
|
|
jerkylips
 Basic Member
 Posts:359
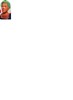
 |
29 Dec 2009 04:46 PM |
|
I briefly gave some thought to doing something like this & decided against it. Honestly, the main factor was cost, but another big one was comfort. If we are in the house, we're barefoot or in socks - never wear shoes in the house. In our old house, there was a HUGE difference in comfort between standing on the tile floor & on the wood floors. Standing at the kitchen sink doing dishes, my feet would start to hurt. There is NO cushion in that floor. For that reason, I couldn't see myself ever putting concrete on the first floor.
Not sure what the orientation of your home is, but we're building a walkout, back of the house facing due south. We're trying to do a passive solar design, so in addition to 1st floor windows we're going to have a fair amount in the basement as well, on the south side. That will "hit" the concrete slab & take advantage of the thermal mass. We don't have any overhangs on the basement windows so probably will get some heat in there in the summer, but in this climate I'm more concerned about pulling in heat in the winter. |
|
|
|
|
Bob I
 Veteran Member
 Posts:1435
 |
30 Dec 2009 11:20 AM |
|
discussion here about using additional drywall as thermal mass: http://www.greenbuildingadvisor.com/community/forum/green-building-techniques/15095/thermal-mass |
|
Bob Irving<br>RH Irving Homebuilders<br>Certified Passive House Consultant |
|
|
Brawler
 Basic Member
 Posts:229
 |
30 Dec 2009 03:48 PM |
|
Hey guys. I spent maybe an extra 250 to 350, its been a while, to set trusse ever 12 inchs instead of 16. Other than that cost i will have the cost of 1 1/2 inch concrete, less than 2 1/2 yards and tubing. I do have concerns about standing on tile alot but i am sure we will have a couple runners in the kitchen and a small rug near the couch. For me it cost less than just the warmboard would have. I am laying out the tubing myself, about one ft of tubing per sq ft of floor, spaced tighter near the windows and doors. I like the idea of a heavy slab for the flywheel effect it gives. |
|
|
|
|
jmagill
 Basic Member
 Posts:371
 |
30 Dec 2009 04:32 PM |
|
Our main floor is the same as Brawler is going to do.
I do have to wear shoes if I am doing alot of moving around cleaning etc. but I would not give up the feeling of bare feet on a cold winter morning on that wonderfully warm floor. I am sorry but wood over radiant does not compare to concrete radiant.
Our floors are acid stained concrete and a breeze to keep clean. |
|
|
|
|
Brawler
 Basic Member
 Posts:229
 |
31 Dec 2009 08:07 AM |
|
Jmagill, How thick did you pour? Did it crack on you much. Do you think if we poured 2" we could skip the tile and just stain it. I could live with a little cracking to save the money for tile? Does anyone know how much effect marmoleum tile would have on the transfer of heat to the room? The stuff is fairly dense and very thin. thanks michael HAPPY NEW YEAR!  |
|
|
|
|
jmagill
 Basic Member
 Posts:371
 |
31 Dec 2009 08:34 AM |
|
I would forgo any thing like tile etc. You can stain it yourself and gets some great looks. We have cracks. You need control joints in areas where the concrete might pull apart. Doorways and where small areas of slabs meet( such as the end of a hallway into a bigger room. Lots of people put score lines so it looks like tile. The best thing you can do is a long slow drying of the slab with no heat. Do not crank up the radiant for a few months if you can help it. |
|
|
|
|
jmagill
 Basic Member
 Posts:371
 |
31 Dec 2009 08:35 AM |
|
Sorry forgot. We did a 1.5 " pour. I had a few large cracks, I filled them with concret filler(flexible) and painted them to match the floor. Next time I will know to put in control joints. I actually like the idea of inset wood thresholds or decorative pieces. |
|
|
|
|
Bruce Frey
 Basic Member
 Posts:429
 |
31 Dec 2009 09:39 AM |
|
Posted By Brawler on 12/31/2009 8:07 AM Jmagill, How thick did you pour? Did it crack on you much. Do you think if we poured 2" we could skip the tile and just stain it. I could live with a little cracking to save the money for tile? Does anyone know how much effect marmoleum tile would have on the transfer of heat to the room? The stuff is fairly dense and very thin. thanks michael HAPPY NEW YEAR!  A question to you guys who are pouring a topping slab over wood trusses and wood sub-floor: Do you set your interior walls on the wood subfloor or on the topping slab? It seems that cracking would less of a problem if it is done on a "room by room" basis after the interior walls are up due to the smaller areas and reduced deflection. A tradeoff would be the added difficulty in finishing smaller spaces. This could make a difference if you are leaving the topping exposed. Bruce |
|
|
|
|
jmagill
 Basic Member
 Posts:371
 |
31 Dec 2009 09:47 AM |
|
We framed all the walls, had drywall up and placed sleepers under all the places where cabinets would go. All the plumbing was in. Then we laid all the pex. It gave us clear view of where we wanted to put pex and where we did not want it. |
|
|
|
|
Bob I
 Veteran Member
 Posts:1435
 |
31 Dec 2009 01:51 PM |
|
A builder in the Seattle area puts down the base plates for the walls, then Ice & Water Shield over the plywood subfloor, then PEX tubing for the radiant heating & pours the slab even to the top of the base plates - giving you a 1-1/2" thick slab. Fast since you're not working around the walls and smaller sections of concrete. |
|
Bob Irving<br>RH Irving Homebuilders<br>Certified Passive House Consultant |
|
|
Brawler
 Basic Member
 Posts:229
 |
31 Dec 2009 06:19 PM |
|
If i was planning on skipping the tile and goin with a concrete finish surface should i avoid fibers in the mix? Im afraid they might stick out and be unconfortable. My room is small, 19x27 on the interior, much of which is taken up with stairs kitcken cabinets and a tiny powder room. Any idea how to cut a control joint without cutting the pex? I was going to pour the entire floor, even under the cabinets. What are the problems with that? |
|
|
|
|
jmagill
 Basic Member
 Posts:371
 |
31 Dec 2009 07:18 PM |
|
No fibers, though I have heard of people polishing them off. Maybe a bit more reasearch on that one.
The control joints should only be maybe 1/8 of and inch. No problems with poring concrete under the cabinets, it is just easier later if you need to add more plumbing etc. to have no concrete to go through. |
|
|
|
|
Bob I
 Veteran Member
 Posts:1435
 |
02 Jan 2010 08:34 AM |
|
Brawler - don't use the fiber - it will show. Also, DON'T CUT control joints - one cut in the PEX and your radiant heat is history. You can use premade control joint material or precoated metal or wood which you later remove. The ideal method is to manually do the control joints with a grooving tool - like you see on concrete sidewalks. It is time consuming, but gives a custom look like nothing else. |
|
Bob Irving<br>RH Irving Homebuilders<br>Certified Passive House Consultant |
|
|
jbaron
 Basic Member
 Posts:122
 |
02 Jan 2010 11:37 AM |
|
The plastic fibers do not show in the final product. Their sole purpose is to prevent plastic cracks in finished concrete, and obviously, they would not be in use if they failed - by showing - in the finished product. The act of troweling off the wet concrete puts them below the surface. See www.fibermesh.com for information.
We used hand troweled control joints becuase we (as Bob) liked the look of them. Just like sidewalks, and very distinctive. However, the lines are wider than you might want to use. It you'd prefer to cut the crontrol joints, run the Pex under a piece of protective material (metal, a piece of rebar) where the joints are to be cut to be sure that the Pex is deep enough.
Jeff
|
|
|
|
|
Bob I
 Veteran Member
 Posts:1435
 |
04 Jan 2010 11:13 AM |
|
I have used the fiber mix in garages and basements and have seen that it can be visible. I have also heard, although have no personal experience, that PEX can "float" in the concrete and may not be as far down in the concrete floor as you think. I wouldn't want to take the chance. Bob |
|
Bob Irving<br>RH Irving Homebuilders<br>Certified Passive House Consultant |
|
|