euler
 New Member
 Posts:11
 |
05 Aug 2015 12:26 PM |
|
I have a question about using closed-cell spray foam on the exterior of a (new) poured concrete foundation. We live in climate zone 6 and are planning a new construction house, most likely to break ground a year from now. State building code now requires R-10 insulation on exterior foundation, extending at least 6" below grade.
Has anybody used spray foam for exterior foundation insulation instead of rigid foam board (e.g., type IX EPS or type IV XPS)? Would 2" of closed-cell spray foam be feasible?
I understand that finishing details on exterior foundation foam are tricky to say the least. My inclination would be to use surface bonded cement and live with the reality of occasional maintenance. I imagine spray foam surface would not be as level or smooth as rigid foam. Aesthetics aside, could surface bonded cement (or an alternative finish) be applied as practically to the spray foam as it can to rigid foam?
Although termites are not a concern in our region, I am also wondering if spray foam's tight direct adhesion to the exterior foundation might further reduce the likelihood of the hidden space behind the foam providing a potential thoroughfare for insects.Thank you for any advice. |
|
|
|
|
|
Bob I
 Veteran Member
 Posts:1435
 |
05 Aug 2015 12:47 PM |
|
It will work, but if you do this, cover it with a good, heavy coat of cement based stucco to well below grade. We used to trowel on Acryl 60 mixed with Thoroseal Plaster Mix which form a hard cement like coating which requires no maintenance and lasts very well. But we gave that up when we saw too many applications of poorly covered exterior Styrofoam with thousands of ant tunnels. So then we went to interior insulation which can be 2" closed cell foam sprayed onto the inside of the wall, or (our current method) two layers of 2" polyiso where the interior layer is fire retardant. And while termites are not a problem now, they are moving north. Also, carpenter ants (which are local residents) love exterior foam! |
|
Bob Irving<br>RH Irving Homebuilders<br>Certified Passive House Consultant |
|
|
euler
 New Member
 Posts:11
 |
05 Aug 2015 01:28 PM |
|
Bob,
Thank you for the advice. I appreciate the thermal advantages of exterior insulation; I do not, however, relish the impractical finishing details. The older house we bought and live in now has EPS board on a lot of the exterior foundation with a synthetic stucco-like finish, and it is a pain in the rear.
On balance, I think I would prefer all interior insulation in the basement, but for new construction our 2015 state building code dictates R-10 on the exterior foundation, so I think we are stuck with board or spray foam outside. I will research using a thick, real stucco finish (instead of acrylic), extending well below grade, on the foam once we get to the point of hiring a contractor and working on the design specs. |
|
|
|
|
Bob I
 Veteran Member
 Posts:1435
 |
05 Aug 2015 02:04 PM |
|
The stucco is troweled on, so the thickness & finish is up to you. I used this mixture on my house & when, twenty years later I built an addition, had to saw the damn stucco - was too tough to break it otherwise. |
|
Bob Irving<br>RH Irving Homebuilders<br>Certified Passive House Consultant |
|
|
euler
 New Member
 Posts:11
 |
05 Aug 2015 02:52 PM |
|
I like durable! Given up to 12" of the stucco finish will be below grade after backfilling, would you recommend waterproofing it (paint or otherwise)? Or is that unnecessary because the foam behind (assume closed-cell) will have a low perm rate -- and the foundation behind the foam will have its own waterproofing as well? |
|
|
|
|
Bob I
 Veteran Member
 Posts:1435
 |
05 Aug 2015 03:08 PM |
|
we always waterproof the foundation - a minor expense in the scheme of things. make certain that the waterproofing is compatible with foam, since some types will melt the foam. |
|
Bob Irving<br>RH Irving Homebuilders<br>Certified Passive House Consultant |
|
|
euler
 New Member
 Posts:11
 |
05 Aug 2015 03:13 PM |
|
Thanks, Bob. Yes, definitely going to waterproof the foundation. I am paranoid about moisture problems.
I was wondering if it is overkill to additionally waterproof the exterior of that portion of the stucco finish surface that will be below grade. I am not familiar with stucco since it has a reputation of being installed poorly in our climate zone, so perhaps waterproofing is standard with stucco and a moot point. |
|
|
|
|
Bob I
 Veteran Member
 Posts:1435
 |
05 Aug 2015 03:17 PM |
|
yes - moot point. One thing I omitted - we also installed a plastic fabric mesh over the foam which helps the stucco coating bridge the different sheets. Sold by masonry supplies who sell the Thoroseal. |
|
Bob Irving<br>RH Irving Homebuilders<br>Certified Passive House Consultant |
|
|
Bob I
 Veteran Member
 Posts:1435
 |
05 Aug 2015 03:25 PM |
|
the best ways to prevent moisture in the house: 1. Good drains (white PVC in washed stone) which goes to daylight 2. Sand backfill 3. Install and tape a heavy poly under the slab above your foam. |
|
Bob Irving<br>RH Irving Homebuilders<br>Certified Passive House Consultant |
|
|
Bob I
 Veteran Member
 Posts:1435
 |
05 Aug 2015 03:25 PM |
|
the best ways to prevent moisture in the house: 1. Good drains (white PVC in washed stone) which goes to daylight 2. Sand backfill 3. Install and tape a heavy poly under the slab above your foam. |
|
Bob Irving<br>RH Irving Homebuilders<br>Certified Passive House Consultant |
|
|
Bob I
 Veteran Member
 Posts:1435
 |
05 Aug 2015 03:25 PM |
|
the best ways to prevent moisture in the house: 1. Good drains (white PVC in washed stone) which goes to daylight 2. Sand backfill 3. Install and tape a heavy poly under the slab above your foam. |
|
Bob Irving<br>RH Irving Homebuilders<br>Certified Passive House Consultant |
|
|
jonr
 Senior Member
 Posts:5341
 |
05 Aug 2015 03:40 PM |
|
definitely going to waterproof the foundation. I am paranoid about moisture problems. My understand is that preventing water entry has more to do with eliminating the pressure via an air gap/drainage than trying to block the entry of the water with a coating. The coating is more for water vapor (damp proofing). |
|
|
|
|
smartwall
 Veteran Member
 Posts:1197
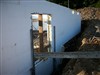
 |
06 Aug 2015 01:22 PM |
|
In NY you need R-10 to the footing. Spraying puf on the outside will leave you with a very rough surface and cost a lot more than sheet foam |
|
|
|
|
Dana1
 Senior Member
 Posts:6991
 |
06 Aug 2015 04:34 PM |
|
Posted By smartwall on 06 Aug 2015 01:22 PM
In NY you need R-10 to the footing. Spraying puf on the outside will leave you with a very rough surface and cost a lot more than sheet foam
(probably putting too fine a spin on it but...) It only need R10 because NY code is based on IRC 2009. If bumped it to IRC 2012 (or IRC 2015) levels R10 would only valid for US climate Zone 4 (Long Island, NYC, Westchester County). In the rest of NY ( zones 5 & higher) it would need R15, which would be even more expensive and difficult. 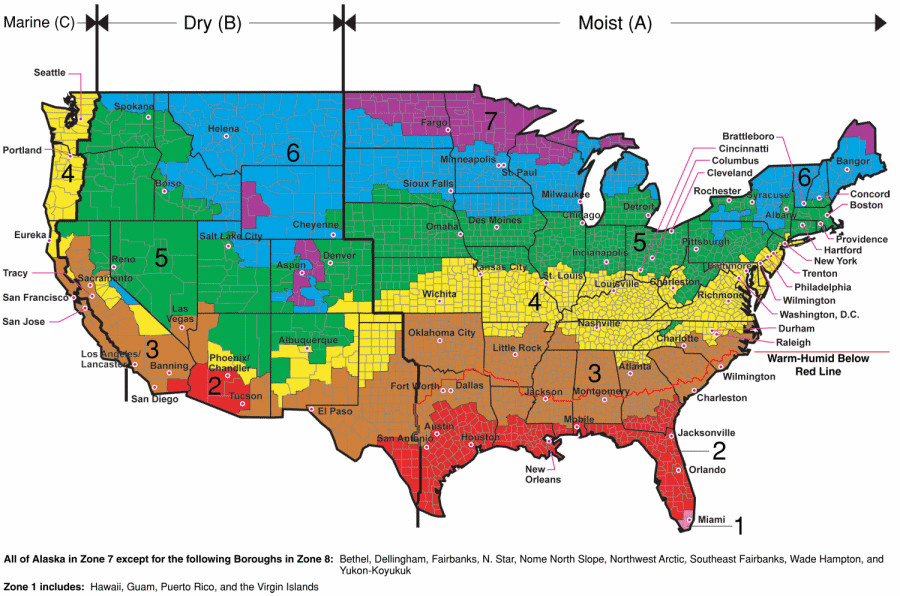 |
|
|
|
|
euler
 New Member
 Posts:11
 |
06 Aug 2015 04:55 PM |
|
Yes, our state (Minnesota, covering zones 6 and 7) adopted IRC 2015 this year and requires R-15 total for the foundation, R-10 of which must be on the exterior. With our house plan ideas, we are also considering ICF as an alternative to a traditional pour with 2" of XPS board/closed-cell spray on the outside and >= 1.5" of foam (XPS or spray) on the inside. I'm not a builder but I imagine the new code is going to be a headache for many of them. All things considered, perhaps ICF would make things easier, though finishing details will loom large either way. |
|
|
|
|
Dana1
 Senior Member
 Posts:6991
 |
06 Aug 2015 06:03 PM |
|
Posted By euler on 06 Aug 2015 04:55 PM
Yes, our state (Minnesota, covering zones 6 and 7) adopted IRC 2015 this year and requires R-15 total for the foundation, R-10 of which must be on the exterior. With our house plan ideas, we are also considering ICF as an alternative to a traditional pour with 2" of XPS board/closed-cell spray on the outside and >= 1.5" of foam (XPS or spray) on the inside. I'm not a builder but I imagine the new code is going to be a headache for many of them. All things considered, perhaps ICF would make things easier, though finishing details will loom large either way.
There is no requirement for R10 to be on the exterior in the IRC 2015 Table 401.1.2 , allows the R15/R19 requirement to be met with any arrangment of insulation, including R5 continuous foam on either the interior or exterior of the foundation in combination with an R13 studwall. See note "c" below the Table. MN has a history of making modifications to the IRC regarding foundation insulation, and even disallowed having more than R10 until recently, apparently out of concern about frost heaving(?). The MN modification to IRC 2015 regarding basements found on the state website reads: ----------------------- Subp 3.
Section R402.2.8, Basement walls.
IECC section R402.2.8, Basement walls, is amended to read as follows:
R402.2.8 Basement walls. Walls associated with
conditioned basements shall be insulated from the top of the basement
wall down to 10 feet (3048 mm) below grade or to the top of the footing,
whichever is less. Foundation insulation shall be installed according
to the manufacturer's installation instructions. Walls associated with
unconditioned basements shall meet the requirements of this section
unless the floor overhead is insulated in accordance with sections
R402.1.1 and R402.2.7 and the following requirements:
a. R-15 insulation for concrete and masonry
foundations shall be installed according to R402.1.1.1 to R402.1.1.8 and
a minimum of a R-10 shall be installed on the exterior of the wall.
Interior insulation, other than closed cell spray foam, shall not exceed
R-11. Foundations shall be waterproofed in accordance with the
applicable provisions of the International Residential Code (IRC).
Exception: R-10 continuous insulation on the
exterior of each foundation wall shall be permitted to comply with this
code if the tested air leakage rate required in section R402.4.1.2 does
not exceed 2.6 air changes per hour and the total square feet between
the finished grade and the top of each foundation wall does not exceed
1.5 multiplied by the total lineal feet of each foundation wall that
encloses conditioned space. Interior insulation, other than closed cell
spray foam, shall not exceed R-11. See footnote c to Table R402.2.1. ------------------------------ This requirement in Minnesota apparently related to frost heave potential doesn't have much in the way of building science behind it, and is not a requirement anywhere else. It's not clear why no more than R11 on the interior is allowed unless it's closed cell foam either, but they seem to be (once again) going out of their way to make it complicated & expensive in MN.  |
|
|
|
|
Rvcrusin
 New Member
 Posts:1
 |
14 Sep 2015 09:22 PM |
|
Major gripe here with new MN energy code. Last week I installed LiteForm Flexxblock up 4' for a bi-level house. I had the inspector show up and tell me that I need more insulation on the exterior of my wall. I was totally blind sided. LiteForm has a R-18 empty, R-23 with 8" fill (EPS is R-4.5 per inch). So now I am left dumb founded as to any excuse/code reference to not have to put additional insulation on the outside of my ICF wall. Are they seriously thinking that the 1/4" fan-fold insulation with R-1 is really going to benefit this house? (Because that is what I am ultimately going to end up doing) Any comments/help on this R-10 to the exterior of an ICF wall is greatly appreciated. Thanks |
|
|
|
|
arkie6
 Veteran Member
 Posts:1453
 |
15 Sep 2015 12:43 AM |
|
In Dana's link above to the state website, it shows in table 402.1.1 that the minimum Mass Wall R-Value is 15 in Zone 6 and 19 in Zone 7. ICF is considered a Mass Wall. What zone are you in? It is not clear to me exactly what your construction is, but maybe this also applies:"Crawl space insulation: R‐15". If the area enclosed by the ICF is considered crawl space, then your R-18 ICF exceeds the minimum. But there is exception 402.2.8 for walls associated with conditioned basements that requires a minimum of R10 exterior insulation.
|
|
|
|
|
Dana1
 Senior Member
 Posts:6991
 |
15 Sep 2015 11:17 AM |
|
As pointed out in my prior post, Minnesota heavily modifies the IRC relative to foundation insulation, with lots of prescriptions & restrictions including minimums for exterior foundation insulation, and maximums for interior insulation over some sort of paranoia about frost heaving foundations. (The source of or real-world data behind that paranoia is unknown to me.) Minnesota code currently requires R15 minimum for foundtations, with a minimum of R10 on the exterior under the most recent revision. R18 is more than R15, but R9 isn't R10 ( but R9+ R1 is.) Is the inspector just being a shmuck, or just doing his job? It could be argued both ways. EPS is not R4.5 per inch, unless the average temp through the foam is 40F, with the warm side at 65F and the cold side at +15F (one of the standard ASTM C518 test conditions.) That may approximate the mid-winter averages in Minneapolis, but not the early or late winter conditions, and in warmer weather it's much lower than that. The spec for Flexx-Block is R4.00/inch minimum under the standard 75F ASTM C518 test condition required for labeling insulation per the FTC. If the inspector is allowing you to use the 40F number and calling it R18 instead of R16, he's being generous. But even using the 75F /50F delta-T labeled R-values for EPS the above-grade portion would meet code on performance without the R1 XPS in zone 6, but not foundations, since there's only R8-9 on the exterior. The whole-wall R of a Minnesota 2015 code min 2x6/ R21 wall is about R15, and even without thermal mass effects the continuous R18 EPS would meet Minnesota code on a PERFORMANCE basis, but not for zone 7 as drafted into code, which (like the IRC), requires R19 for mass walls. In zone 7 (but not zone 6) MN code would fail an R18 mass-wall per Table 402.1.1, of current MN code: http://codes.iccsafe.org/app/book/content/2015_Minnesota/Residential/Chapter%204%20%5BRE%5D.html You might be able to argue it on a U-factor basis, adding in the effective R values of the finish wall and siding, and the choices used there may actually make the difference. Take a close look at Table R402.1.3, and pay a registered professional engineer to calculate the U-factor. Or maybe you can just use some of the EPS loaded vinyl clad siding or something, sufficient to make it dead-obvious that it meets code. If you're not in zone 7, the inspector is simply dead wrong, except for the foundation. |
|
|
|
|