RGates
 New Member
 Posts:59
 |
29 Nov 2011 08:21 PM |
|
Hello to All, I am building my timber frame in Feb. 2012. I am in MD. zone 4. I would like some opinions on my plans to insulate. The wall system is as follows from the outside in: stone + 1" air space + 2" - 2 lb. SPF + 1/2" cdx + 2X4 Af with 3 1/2" dense pack cellulose + 5/8" drywall + paint The foundation will be as follows from the outside in: 2' - 2lb. SPF + 10" poured walls The roof system is as follows from the outside in: roofing (type tbd) + 5/8" plywood + 5" - 2 lb. SPF + 2X6 T&G The foundation SPF will continue from the footer up to the stone shelf then jump back to the wall face and continue up to the roof section. It will be basically be seamless except for the break at the stone shelf. The windows and doors will be extended out with 3/4" jamb extensions. The roof system will have 2X6 rafters on top of the 2X6 T&G with blocking underneath to allow foam under the rafter to avoid thermal bridging. I will then fill the cavity with 2lb. SPF. either to the top or stopping it to allow for a cold roof. Then the 5/8" plywood. Questions: 1.) I have the ability to make the system a cold roof, is it worth it? Thank you in advance for your time and consideration. Be gentle, I am delicate !  Ron |
|
|
|
|
|
Dana1
 Senior Member
 Posts:6991
 |
30 Nov 2011 12:01 PM |
|
SPF has a spotty track record when in direct contact with soil- is the foundation insulation intended to be interior only? 5" of 2lb foam cavity fill on a roof is a waste of money. A 2" shot would be more than sufficient for an air-seal and condensation control, and would allow you to use much cheaper fiber insulation on the interior to achieve your final center-cavity R. see: http://www.buildingscience.com/documents/reports/rr-1001-moisture-safe-unvented-wood-roof-systems If the roof lines are relatively simple it's cheaper & better to use rigid foam (or SPF, if you go deep enough) on the exterior of the roof deck, placing all of the susceptible wood at least partly inside the thermal boundary where it stays warmer & drier. |
|
|
|
|
WindowsonWashington
 New Member
 Posts:96
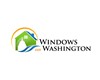
 |
30 Nov 2011 12:19 PM |
|
Ron,
I will detail out the roof insulation and I am sure that Dana and the other sharp guys on here can help with the other details.
Eric
|
|
The difference is clear |
|
|
RGates
 New Member
 Posts:59
 |
30 Nov 2011 06:12 PM |
|
Dana, thanks for the reply. This is a timber frame therefore the underside of the T&G is the inside ceiling. This is the reason for everything on top of the T&G. I have looked at using rigid foam on the roof and 2X4 sleepers on top of the foam with plywood on top of the sleepers then the roofing, commonly known as the rap & strap system. I believe the cost would come out the same and the SPF would be a much better system.
Thanks
|
|
|
|
|
Dana1
 Senior Member
 Posts:6991
 |
30 Nov 2011 06:26 PM |
|
SPF would be more air-tight, but the installed cost of 2lb foam is about 17 cents/R per square foot, installed, whereas iso usually comes in at about 9-10cents f.o.b. the distributor's yard, which still gives you a lot of room to pay for installation. Detailing sheet goods a primary air barrier isn't difficult. The key is whether the roof lines are so complicated that there's a lot of scrap and excessive labor. On simpler roofs it can be a lot cheaper than 2lb foam. With a rococo-architect's collection of artful hips,valleys and dormers, maybe not. Using reclaimed goods from commercial re-roofing you can bring the material cost down to ~3cents/R/foot (InsulationDepot.com or similar.) That's my plan when it's time to re-roof in short years (despite the oh-so-charming hipped roof, 2 big valleys, 3 dormers, and 2 skylights. ;-) ) |
|
|
|
|
RGates
 New Member
 Posts:59
 |
30 Nov 2011 06:48 PM |
|
I agree with an up and over simple roof that the ISO approach would be less costly. This roof is an 8/12 and there are numerous dormers, hips and valleys. I looked at the labor of dealing with 2 layers of rigid foam, detailing all of the joints ie. stagger, tape, foam,waste and then the 2X4 strapping on top. There is a lot of labor associated with the preceding system. The SPF system, in my situation as per the original post, simply requires a 2X6 rafter on top of the T&G and then let the foam guy go to town. Beyond all of the labor issues the SPF will be a far tighter system thus eliminating any air leaks and ultimately condensation issues in the rigid foam scenario.
|
|
|
|
|
RGates
 New Member
 Posts:59
 |
30 Nov 2011 08:48 PM |
|
Dana
Could you elaborate on your comment with regards to CC SPF on exterior foundation walls. What are your thoughts on a vapor barrier in the rigid foam roof system?
Thanks Ron
|
|
|
|
|
WindowsonWashington
 New Member
 Posts:96
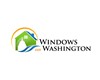
 |
01 Dec 2011 12:58 PM |
|
Ron, If the roof is chopped up, CC SPF is going to be easier, however, you will not get the performance out of that assembly at 5" of foam. Even assuming 2x6 at 24" OC with the foam isolation block (1" iso @ R-6), the R-Value of the assembled roof is only about R-25. This is figuring on the CC SPF at R-6.5 per inch. All the 2x6 framing on the roof deck is certainly no easy task either and should be considered when looking at the rigid option. T&G decking would be sealed with all peel and stick ice and water membrane prior to first course of rigid foam for proper air seal and vapor barrier on the T&G. The surface temperature of the T&G should never get that low with proper insulation detail to the exterior so condensation should not be an issue. Given that you are only building it once, I would want to put an R-40 or better across the roof.
|
|
The difference is clear |
|
|
Dana1
 Senior Member
 Posts:6991
 |
01 Dec 2011 03:22 PM |
|
Posted By RGates on 30 Nov 2011 08:48 PM
Dana
Could you elaborate on your comment with regards to CC SPF on exterior foundation walls. What are your thoughts on a vapor barrier in the rigid foam roof system?
Thanks Ron
I've not seen the evidence but have heard multiple reports recently verbally that 2lb foam in soil contact below grade both on walls and under slabs have failed- ends up crumbly. I don't have specific products or installers, don't know the specifics, but I know of at least one design that got changed to XPS after a bad experience by the contractor with 2lb foam under a slab. EPS based ICFs have a long and pretty-good history below grade, but in termite zones it's best to use a sand backfill material to limit tunnelling in the EPS, and use a copper sill plate that extends out beyond the foam. There's no point to an interior-side vapor barrier on a roof with only rigid-foam above the roof deck as insulation. Foam is air-impermeable, and the susceptible wood is all inside of conditioned space- it dries toward the interior, but is already largely protected from exterior moisture drives by the foam, and since it's entirely inside conditioned space, is inherently protected from interior moisture drives. Depending on the type of foam it may already be lower permeance than a kraft facer.(~0.4 perms). At 3" XPS would be there but you'd have to be at 8-10" with Type-I EPS to hit that range. With fiber-faced iso it's all about the number of facers, since the foam itself is quite permeable. Most fiber faced goods are between 0.5-1 perms in a single layer, half that if you double up (say 2 layers of 3" goods, to hit R36-ish). Foil facers are true vapor barriers- which is OK as long as you're not sandwiching wood between a foil facer and some other vapor barrier. With either rigid or SPF on the exterior, a furring-mounted vented nailer deck is still advisable to protect the nailer deck from degradation, since it can't dry through the foam. In complex roof lines it's better to segment the furring with ample gaps to allow cross ventilation as well. |
|
|
|
|
RGates
 New Member
 Posts:59
 |
01 Dec 2011 08:41 PM |
|
Dana & Windows, I have seen examples of the rigid built up systems. All of them contain either a peal & stick or a poly vapor/air barrier below the first sheet of rigid. Could the barrier step be eliminated due to the fact that the foam, obviously based on the type and surface treatment ie ISO, EPS, XPS with or with out foil or fiber, would become your vapor/moisture barrier as you staggered and sealed the joints in the layers?
|
|
|
|
|
WindowsonWashington
 New Member
 Posts:96
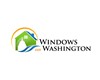
 |
01 Dec 2011 08:53 PM |
|
Technically speaking...yes. The difference in this application is that when you are figuring on this sort of investment (structure and foam), many folks will opt for the additions $0.50-0.60 per foot of materials. In a near perfect new construction format, the deck will be nearly level, however, such is not the case is most retrofit applications.
|
|
The difference is clear |
|
|
RGates
 New Member
 Posts:59
 |
01 Dec 2011 09:22 PM |
|
Decisions decisions, I have been balancing the two systems, rigid vs. SPF, for a long time. The SPF will fill all of the imperfections eliminating that air leak/condensation issue ultimately becoming a near perfect barrier. The rigid system will be much harder to detail to obtain a good barrier therefor the need for a membrane. With regards to the R-Value calcs. I was thinking of a 1 1/2" spacer under the 2X6 to help with the thermal bridging. I can add more foam to the system and still have the cold roof.The costs of of the applied barrier material in the rigid system would buy me another1" of SPF. |
|
|
|
|
WindowsonWashington
 New Member
 Posts:96
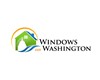
 |
01 Dec 2011 09:35 PM |
|
It is a substantial investment for certain. I prefer the bang for the buck out of the rigid vs. the spray foam in this application and also the fact that PolyIso is so well tested in roof applications. Peel and stick is the most common air barrier across the roof deck because of its self sealing properties, however, you could put down a synthetic underlayment and seal that straight to the roof deck via caulking/sealants and have the similar air barrier. You can go straight with the foam as well, but the added protection given the self stated complexity of this roof is what has me leaning towards the peal and stick membrane. SPF is certainly the easiest but the R-Value as the depths you were throwing out before just aren't there. |
|
The difference is clear |
|
|
Dana1
 Senior Member
 Posts:6991
 |
01 Dec 2011 10:15 PM |
|
Posted By RGates on 01 Dec 2011 09:22 PM
Decisions decisions, I have been balancing the two systems, rigid vs. SPF, for a long time. The SPF will fill all of the imperfections eliminating that air leak/condensation issue ultimately becoming a near perfect barrier. The rigid system will be much harder to detail to obtain a good barrier therefor the need for a membrane. With regards to the R-Value calcs. I was thinking of a 1 1/2" spacer under the 2X6 to help with the thermal bridging. I can add more foam to the system and still have the cold roof.The costs of of the applied barrier material in the rigid system would buy me another1" of SPF.
You don't need a membrane to make it a decent air-barrier. With virgin stock you can use housewrap tape (or 1-part foam) on the seams & edges. With foil-faced goods you can use FSK tape. Or, you can use housewrap over the rigid foam, detailed as an air barrier. All of which is a heluva lot cheaper than the $1/square foot you'd be paying for another inch of SPF. (But an inch of SPF sprayed over the rigid foam would also make a nice near-perfect air barrier.( There is no point to thermally breaking between the 2x6s and the rafters if all of the insulation is above the roof deck- both the rafters and the roof deck are fully within the thermal boundary, already at the same temperature. Even if you had insulation between the rafters, the foam over the roof deck would be your thermal break, and far in excess of 1.5" of foam at the rafter. Similarly, there is no condensation issue to be concerned about even with minor air leaks- the 2x6 roof deck is always at the temperature of the conditioned space, and has roughly the same vapor permeance as 1" of closed cell foam- any condensation during the cooling season from minor air leaks through the rigid foam would still dry toward the interior just fine. The foam is air-impermeable, it's nothing like having a leaky fiber-filled cavity insulating the roof deck from the exterior. |
|
|
|
|
RGates
 New Member
 Posts:59
 |
02 Dec 2011 07:58 AM |
|
Dana, The point I was trying to make is that if I use SPF the assembly would be much tighter. I was looking at the costs of each assembly, SPF vs. rigid. If the rigid assembly could be detailed enough I could possibly do away with the membrane. With the complexity of the roof this is a tough detail with rigid. With regards to the thermal breaking of the 2x6. I do not think you are understanding the assembly.It is like a standard roof assembly in reverse. The rafters are on the outside. The function of the rafters is to provide a nailing surface for the plywood. In my case a 2x6 spaced up off of the T&G by 1.5" would make the top of the 2x6 7" off of the T&G . If I put in 5" of foam I have a 2" air gap between the underside of the plywood and the foam.By keeping depth of the foam below the top surface of the 2x6 it allows
an air gap between the SPF and the plywood giving me a cold roof.
The roof system is as follows from the inside out: 2X6 T&G + 2x6 rafters (spaced off of the T&G 1.5")+ 5" - 2 lb. SPF+ 5/8" plywood + roofing (type tbd) When we are filling the 24" spaces between the rafters the 1.5" space between the T&G and the 2X6 rafter would allow the foam to flow in between providing a thermal break between the rafter and the T&G . So ultimately the 2x6 would be encased in foam except for the points were it is held up off of the T&G. This would eliminate some of the R value derating of the assembly. I need to calculate this deration to obtain how much foam will be required. I can then do the cost comparison of rigid vs. SPF. The costs of the SPF become cheaper as the depth increases, the cost factor is not linear . My guess is that in my case because of the roof complexity there will not be that much of a difference. I have no love affair with either assembly,money is not the only driving factor, I am trying to figure out which will be the best in the end. Respectfully, Ron
|
|
|
|
|
WindowsonWashington
 New Member
 Posts:96
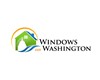
 |
02 Dec 2011 08:25 AM |
|
Ron, I calculated the R-Value of that assembly based on what you provided me from before. Based on what you had said before (5" CC SPF, and 1" isolators). If the roof is chopped up, CC SPF is going to be easier, however, you will not get the performance out of that assembly at 5" of foam. Even assuming 2x6 at 24" OC with the foam isolation block (1" iso @ R-6), the R-Value of the assembled roof is only about R-25. This is figuring on the CC SPF at R-6.5 per inch. Even if you put down 6" of SPF and a 1.5" foam isolation, the total assembly R-Value is still less than 30 (R-29 by my calculations). This is figuring on 15% area being the 2x6, 1.5" of iso at R-9, 6" of CC SPF at R-36. In a cathedral ceiling, R-38 would be the minimum you would like to see. You can certainly help the efficiency of that assembly with the heat gain in the summer month with an air gap and some over deck venting as well as using metal (please don't tell me you are going to use asphalt on a beautiful timber frame roof), but this will have no application value in the winter months.
|
|
The difference is clear |
|
|
RGates
 New Member
 Posts:59
 |
02 Dec 2011 09:17 AM |
|
I will be using metal or slate. By my calculations the 2x6 will only be 6.2% of the assembly. There are no top & bottom plates in the assembly. |
|
|
|
|
WindowsonWashington
 New Member
 Posts:96
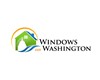
 |
02 Dec 2011 09:27 AM |
|
6.2% is a near ideal calculation. The reality is that if the roof is cut up, it require more than than and you are also going to need blockers and probably a top and/or bottom tie in. 7" of total height that has the base of it sitting on 1.5" of foam is not exactly very stable and while the roof deck you are making is not structural, it needs to be sturdy and rigid enough to get the materials on and maneuver. Once the CC SPF goes down, it will lock it all together pretty nicely but 6.2% is still on correct in theory. Even using your math at 6%, average R-Value is R-33. If you go to what is a much more likely 9-10%, R-Value is R-31. |
|
The difference is clear |
|
|
RGates
 New Member
 Posts:59
 |
02 Dec 2011 10:02 AM |
|
The roof deck is structural. The 2x6 will be attached to the T&G . You are correct, I am planning on the foam to lock it all together. I realize I am still low on the R value. It may be that ISO is the way to go. There is a lot to balance. A ton of labor versus hello Mr. Foam Guy, its ready, spray away!  |
|
|
|
|
Dana1
 Senior Member
 Posts:6991
 |
02 Dec 2011 04:23 PM |
|
Somehow I'd had the impression that the 2x6s was the roof deck, supported by rafters/beams on the interior. It's becoming somewhat clearer now. In MD zone 4A you only need R15 above the roof deck to be able to use fiber on the interior without incurring condensation risk. (See: http://publicecodes.citation.com/icod/irc/2009/icod_irc_2009_8_sec006_par003.htm ) That's 2.5" of iso (or 2lb foam) applied above the roof deck, which would also give you R15 of thermal break rather than R9 you're considering. Dense-packing the cavites with 3lb-3.5lb cellulose from the exterior would make it sufficiently air tight from a thermal point of view (it really does), and gives you ~ R20 center cavity before exterior foam. With R15 above the roof deck you'd be at R35 center-cavity plenty of margin from a code point of view, but going with 3-4" goods on the exterior may still be worth it. With that much thermal break the whole-assembly R isnt undercut nearly as much R20 iso + R20 cavity fill (R40 center-cavity) even with a 15% framing fraction that would yield north of R35 whole-roof, (it may even R38, depending on the species of the t&g ceiling.) With a 10% framing fraction you'd be at least R37 whole-roof. There is no such thing as a 6.25% framing fraction in a 24" o.c. raftered roof- that's a "clear-assembly" fraction valid only if it's a featureless single-pitch shed roof. Even a 10% framing fraction would usually imply a fairly simple roof- no hips or valleys, maybe a couple of dormers and a skylight. In a roof of any complexity it's usually more like 12-15%. Furring through-screwed to the structural roof deck would let you install an OSB nailer on which to hang the slate. If metal, purlins (no nailer) can often work, but depends on the system. If you're loving the spray foam from a mechanical integrity point of view, 2-2.5" shot against the t & g becomes glues it all together- it becomes structural. It usually forms an excellent air barrier & ~0.6 perm vapor retarder, at which point you could install low-density cellulose in the 3-3.5" remaining cavity for a center-cavity R of R23-R25, adding the R15 iso above.
|
|
|
|
|