Roberth
 New Member
 Posts:97
 |
12 Apr 2012 01:15 AM |
|
How much cellulose insulation can a ceiling hold. I have heard people say that cellulose can weigh too much for a ceiling. what can a 1/2 inch or 5/8 inch dyywall handle at 16 or 24" on center. What about plaster. |
|
|
|
|
|
smartwall
 Veteran Member
 Posts:1197
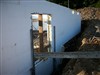
 |
12 Apr 2012 07:34 AM |
|
I did my first r-50 cellulose attic in 1980 16" on center 2x12's 1/2" drywall. I saw the ceiling about 12 years ago and was shocked by the cupping. I did my own house with furring screwed 12" on center attached to the bottom of the trusses, Above that I put r-19 fiberglass with 10" cellulose over that. I know fiberglass sucks but in this case it was a good way to dissipate the weight over a wider area and no cupping after 15 years. |
|
|
|
|
Dana1
 Senior Member
 Posts:6991
 |
12 Apr 2012 11:26 AM |
|
The dead-weight loading of R75 (~24", initial depth) is on the order of ~3lbs per square foot. For R38 it's about half that. If you want to go truly high-R it's generally better to use OSB to support the load, at which point you can apply the thinnest of gypsum on the OSB without danger of sagging or cupping over time. For 20" o.c. trusses a screw & glue approach to the OSB with a bead of construction adhesive applied to the underside of the chord enhances the structural loading capacity of the truss cords too. Pay attention to truss chord loading specs, not just the loading specs of the gypsum if you want R50+. Fatter gypsum adds dead weight without enhancing loading capacity. Using low-density fiberglass + cellulose overblow cuts the dead weight loading by about a third or more at R38, (a bit less of a cut at R50) and isn't a bad option. With at least 3" of cellulose overblow (6" is better) the sucky-aspects of low density batts falls off dramatically, since convection current between the attic-air and entrained air in the fiberglass layers can no longer occur due the higher air-retardency of the cellulose. (Obviously, putting the fiberglass atop the cellulose doesn't work nearly as well.) With 6" of cellulose over R19 you're at ~R40 (beating a code-min R38), and the weight is about 1.2 lbs per square foot, whereas cellulose only would be about 1.6lbs/ft @ R40. For mid-R gypsum-loaded applications it's a good compromise. The weight of smartwall's 10" of cellulose will compress low-density batts somewhat, taking ~R1-2 off the R19 batt layer, but smartwall's stackup is still north of R50, and only slightly more dead loading than R40 cellulose-only. It's more than a 20% increase in R for less than 10% uptick in weight. |
|
|
|
|
dleaoh
 New Member
 Posts:1
 |
13 Apr 2012 11:44 AM |
|
The experience reported by smartwall must be considered in light of the fact that cellulose insulation available in 1980 when he insulated his ceiling was twice as heavy as today's cellulose insulation. If he were insulating the ceiling with cellulose today the loading would be half that of 1980. |
|
|
|
|
arkie6
 Veteran Member
 Posts:1453
 |
13 Apr 2012 12:41 PM |
|
Also note that 1/2" drywall is more prone to sagging in a ceiling application than currently available 1/2" high strength ceiling board. I'm not sure if this stuff was even available in 1980. http://www.usg.com/rc/data-submittal-sheets/panels/sheetrock/sheetrock-interior-ceiling-sag-resistant-submittal-WB2195.pdf http://www.nationalgypsum.com/products/..%5CFile%5C09%2029%2000-06.pdf The above manufacturers literature recommends a maximum of 2.2 lbs/sq ft insulation load when installed per the manufacturers instructions with joists at a maximum of 24" oc. The above ceiling board should be able to handle R49 loose fill which has a weight of ~1.5 lbs / sq ft per this datasheet from Applegate: http://www.applegateinsulation.com/...28983&fd=0 I'm back and forth on how I plan to insulate my ceiling. I've considered installing kraft or FSK faced R13 (3.5") fiberglass batts with the facer flanges close stapled to the sides of the truss chords, then have R38 cellulose blown on top of that. The facing on the batts would provide a vapor barrier as well as help support the load of the cellulose above and provide the additional R value to get to ~R50. Using all stabilized cellulose in the attic is another consideration. I'm also considering 1x4 strapping at 16" oc under the truss chords and just blowing R49 cellulose on top of that to provide additional support. The above combined with 1/2" high strength ceiling board should eliminate most concerns with sagging. |
|
|
|
|
lzerarc
 Basic Member
 Posts:423
 |
13 Apr 2012 02:22 PM |
|
why not just use 5/8" gyp? 5/8" on ceilings is typical around here. |
|
|
|
|
jonr
 Senior Member
 Posts:5341
 |
13 Apr 2012 02:29 PM |
|
I have cellulose blown over fiberglass and it seems to work fine. In a new home, I would consider stabilized cellulose (add a little water (damp, not wet) and it sticks together and supports its own weight). |
|
|
|
|
Dana1
 Senior Member
 Posts:6991
 |
13 Apr 2012 04:16 PM |
|
arkie6: The Applegate spec numbers are MINIMUM weight per square foot, not the nominal, not the max, and not over the long term. Don't design for on the min-spec density. Few installations would meet the min-density on day 1, and none that were min-density when initially applied would remain at that R-value over the long term, but the defree of sag is climate dependent. Seasonal humidity cycling causes settling, leading to over-topping it a decade or two down the line. For the long term weight per square foot at any R value, a 1.2-1.3x multiplier needs to be applied to the min-density spec (and even that might not be enough of a fudge-factor in some particular cases.) |
|
|
|
|
smartwall
 Veteran Member
 Posts:1197
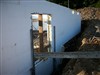
 |
15 Apr 2012 07:35 PM |
|
Dleaoh, That's what amazes me , the primary componets of cellulose insulation have remained the same since the 50's but the coverage per bag has increased kind of redefining the laws of physics. |
|
|
|
|
Dana1
 Senior Member
 Posts:6991
 |
17 Apr 2012 11:10 AM |
|
Posted By smartwall on 15 Apr 2012 07:35 PM
Dleaoh, That's what amazes me , the primary componets of cellulose insulation have remained the same since the 50's but the coverage per bag has increased kind of redefining the laws of physics.
Better blower technology in combination with improvements in the shred in manufacturing may give newer cellulose a lower density/higher performance edge in open blow installations over the goods from decades past, but it's not clear that the long term settled density has been improved as dramatically. It's always been possible to "fluff" the goods with a higher-air mix at installation, but that usually results in rapid settling & loss of performance in short years, requiring re-topping to restore performance. If installing below 1.3lbs per cubic foot initial density it's good to add 15-20% to the initial depth to make up for it, but in very dry climates and an air/vapor tight ceiling you may be able get away with less. The rate and degree of settling is dependent on seasonal humidity cycling. |
|
|
|
|
GTJON
 Basic Member
 Posts:112
 |
17 Apr 2012 11:57 AM |
|
Been selling by the tight packed bag. So estimated is the Day 1 result, but sold is the number~ lbs, bags on contracts.
D1: Do you ever concur with some wetting over sealing fiberglass...?
-Never thought of that, just put 6" on and said it will be a good 4" seal later.
JP
|
|
|
|
|
Dana1
 Senior Member
 Posts:6991
 |
17 Apr 2012 01:00 PM |
|
Misting/wetting the cellulose right after installation keeps high-winds-through-the-soffits from moving it around on you creating thin spots, but wouldn't be necessary for achieving sufficient air-retardency to stabilize R-values over temperature. Some experiments indicate that as little as 3" is enough, but it's hard to get a consistent 3" in an attic (as opposed to a laboratory). A 6" overblow would pretty much guarantee 3" even at the thin spots, (and is less than 2x the cost of a 3" overblow.) |
|
|
|
|
kiwielectric
 New Member
 Posts:5
 |
30 Apr 2012 08:30 PM |
|
This may show my ignorance but why not get spray on foam insulation? It's R value is great and it adds to the structural strength. I ask because that is what I am about to use.
|
|
|
|
|
Lee Dodge
 Advanced Member
 Posts:714
 |
30 Apr 2012 09:50 PM |
|
kiwielectric-
The reason for the interest in cellulose or fiberglass for attic installations in preference to spray on foam is the much lower cost per unit of R-value for those first two. Sometimes spray foams are used in a thin coat for air sealing, and the loose fill is used on top of that as a cost efficient way to get air sealing plus a high R-value at a reasonable cost.
In rare cases, the spray foams do not harden properly, and lead to a stench that is hard to get rid of. |
|
Lee Dodge, <a href="http://www.ResidentialEnergyLaboratory.com">Residential Energy Laboratory,</a> in a net-zero source energy modified production house
|
|
|
smartwall
 Veteran Member
 Posts:1197
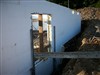
 |
01 May 2012 08:57 AM |
|
My customers pay about $1.10 per ft for r-60 |
|
|
|
|
Dana1
 Senior Member
 Posts:6991
 |
01 May 2012 10:57 AM |
|
Posted By kiwielectric on 30 Apr 2012 08:30 PM
This may show my ignorance but why not get spray on foam insulation? It's R value is great and it adds to the structural strength. I ask because that is what I am about to use.
At anything above R15 or so closed cell polyurethane oam becomes a net greenhouse effect increase over it's lifecycle- the HFC245fa blowing agent's have a larger greenhouse effect than the source energy use it's offsetting, and that's across a broad spectrum of heating fuels & electrical power sources for heat pumps/air conditioning. Open cell foams are more benign (nowhere near as benign as cellulose or rock wool) but offers no structural strength. EPS and polyisocyanurate rigid board is blown with pentane, which has something like two orders of magnitude less greenhouse gas potential per unit R than closed cell foam or XPS. Unlike cellulose or rock wool rigid board foam is air-impermeable, making it useful for condensation control, but it's still way more than 2x as expensive as fiber insulation. Reclaimed rigid foam from commercial roofing demolition can be comparable to or even less expensive per unit-R than virgin-stock fiber insulation, and is greener than any virgin-stock foam, since the environmental hit has already been taken, and re-use is extending the benefit side of the cost ^ benefit equation. |
|
|
|
|
Dana1
 Senior Member
 Posts:6991
 |
01 May 2012 11:00 AM |
|
Posted By smartwall on 01 May 2012 08:57 AM
My customers pay about $1.10 per ft for r-60
... or ~10% of the financial cost of doing it in closed cell spray polyurethane... ...and ~0.00001% of the environmental cost of closed cell spray polyurethane. |
|
|
|
|
Lbear
 Veteran Member
 Posts:2740
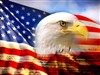
 |
01 May 2012 11:37 PM |
|
What would be the insulation costs for a 1,600 square foot roof area with R-50 cellulose? Ballpark, how much in cellulose and labor costs?
|
|
|
|
|
arkie6
 Veteran Member
 Posts:1453
 |
02 May 2012 06:50 AM |
|
Around here, blown cellulose in the attic is ~$1.00/sq ft for standard R38. That includes all materials and labor. The incremental material costs for additional R value are minimal, so the above post showing $1.10 for R60 would probably be a good number to use to estimate the cost for R50. So 1600 sq ft @R50 would be on the order of $1750 for labor and material. But, AZ labor prices may be significantly different than AR labor prices.
I priced the material to DIY blow in an additional R19 of cellulose in my mom's ~1200 sq ft attic and the material cost from Lowes was <$300. The insulation guys buying this stuff in big bags by the truckload can probably buy it for less than half that.
|
|
|
|
|
Lbear
 Veteran Member
 Posts:2740
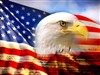
 |
02 May 2012 09:52 AM |
|
Posted By arkie6 on 02 May 2012 06:50 AM
Around here, blown cellulose in the attic is ~$1.00/sq ft for standard R38. That includes all materials and labor. The incremental material costs for additional R value are minimal, so the above post showing $1.10 for R60 would probably be a good number to use to estimate the cost for R50. So 1600 sq ft @R50 would be on the order of $1750 for labor and material. But, AZ labor prices may be significantly different than AR labor prices.
I priced the material to DIY blow in an additional R19 of cellulose in my mom's ~1200 sq ft attic and the material cost from Lowes was <$300. The insulation guys buying this stuff in big bags by the truckload can probably buy it for less than half that.
$2k for R-50 is a great deal. How many inches deep would R-50 be with blown cellulose? |
|
|
|
|