|
Shotcrete home building
Last Post 12 Sep 2014 04:52 PM by cathsand. 26 Replies.
|
Sort:
|
|
Prev Next |
You are not authorized to post a reply. |
|
mrasmussen
 New Member
 Posts:7
 |
03 Jul 2014 09:56 AM |
|
I'd like to have an insulated shotcrete home built in central Texas. While it looks like there are builders in other parts of the country, I'm having difficulty finding one here. Any recommendations would be greatly appreciated.
|
|
|
|
|
|
Alton
 Veteran Member
 Posts:2157
 |
03 Jul 2014 03:00 PM |
|
Do you need help setting the panels or just with shotcreting? Or are you looking for a builder with shotcrete experience? By the way, the term shotcrete includes dry and wet mix. A structure as small as a residence is usually done with the dry mix. That is, the mix is dry through the hose and then water is added to the mix at the nozzle. Be sure that the nozzleman is certified. Avoid mistakes and extra cost. You might benefit by reading this blog from beginning to end: http://waterfrontbuildinginpanamacity.blogspot.com/ Also feel free to e-mail me about alternative technology such as gunite (dry mix), shotcrete (wet mix), etc. |
|
Residential Designer & Construction Technology Consultant -- E-mail: Alton at Auburn dot Edu Use email format with @ and period . 334 826-3979 |
|
|
McFish
 New Member
 Posts:77
 |
04 Jul 2014 06:40 AM |
|
I realize domes are not everyone's cup of tea. But they are shotcrete built, and the leading builder is located in Italy, Tx. See Monolithic domes. Extremely energy efficient, extremely safe. |
|
|
|
|
mrasmussen
 New Member
 Posts:7
 |
04 Jul 2014 09:32 AM |
|
Hi, Alton.
Thank you for the quick response. Yes, I'm looking for a builder that has experience with dry mix shotcrete. I've read that shotcrete was another name for gunite. Is that not the case? If not, can you tell me the difference? I appreciate the link and will give it a good read today.
Michael
|
|
|
|
|
mrasmussen
 New Member
 Posts:7
 |
04 Jul 2014 09:42 AM |
|
Thank you, McFish.
I wouldn't mind a dome. But, it was all I could do to convince my wife of the benefits of a concrete home. When I mentioned the dome, well, I got a serious eye roll and silence.........
|
|
|
|
|
Alton
 Veteran Member
 Posts:2157
 |
04 Jul 2014 10:45 AM |
|
It would be helpful to have a builder that has experience with gunite and shotcrete but not necessary with a qualified spray concrete crew. The terms gunite and shotcrete are used by a lot of people simply to mean sprayed concrete. But within the industry, gunite refers to dry gunning and shotcrete refers to wet gunning. Google "gunite versus shotcrete".
The project in the blog I mentioned used the shotcrete method (wet gun). That is, the ready-mix truck delivered a mix with water already added similar to ordering concrete for a driveway. However, the mix plant delivered some loads that were not shotcrete friendly. For example, gravel was so large that it bounced off of the wall and left holes in the finish. Another serious problem was that the finish crew could not keep up with the nozzleman. The ready-mix truck had to be emptied within a short period of time due to local conditions. The blog I mentioned should be required reading for anyone considering sprayed concrete.
Small projects usually are sprayed with a dry mix that has water added at the nozzle. Large projects often use the wet mix. The gunite method lends itself to stopping and starting without worry about wet concrete setting up in a ready mix truck. For typical residential projects, I would not consider shotcrete. I like the idea of using a bag mix with aggregate not exceeding 3/8" that does not depend upon rushing to empty a ready-mix truck before the concrete sets.
By the way, Gulf Concrete Technology uses a structural mortar that may be more user friendly than either gunite or shotcrete for small projects such as residences. It is a bag mix that can be made in small batches with water added to the mix on site. This reduces the need to rush. Less air pressure is needed and thus smaller equipment can be used. From what I have seen, the small batch, wet mortar mix method with less air pressure results in less rebound (waste). No gravel in the mix makes it easy to get a smooth finish as opposed to shotcrete with aggregate. GCT also has a mix that contains color which eliminates the need to paint. |
|
Residential Designer & Construction Technology Consultant -- E-mail: Alton at Auburn dot Edu Use email format with @ and period . 334 826-3979 |
|
|
jonr
 Senior Member
 Posts:5341
 |
04 Jul 2014 10:48 AM |
|
The term shotcrete includes both wet and dry methods. Perhaps: http://www.centexplaster.com/gunite.htm |
|
|
|
|
mrasmussen
 New Member
 Posts:7
 |
04 Jul 2014 11:56 AM |
|
Very good info. Thank you. I just finished reading that blog you suggested. The owner certainly encountered some obstacles. I'm convinced that gunite is the way to go, not the wet mix he used. I'm hoping he will continue updating his blog, as I would like to see how how finishes out the interior, now that he has the 2x4 framing up. Interesting tip on Gulf Concrete's structural mortar. I'll investigate. Thanks, Alton.
|
|
|
|
|
mrasmussen
 New Member
 Posts:7
 |
04 Jul 2014 11:59 AM |
|
Good tip. Their website indicates they spray gunite for more than just pools. They'll be getting a call from me Monday. Thank you, jonr.
|
|
|
|
|
Alton
 Veteran Member
 Posts:2157
 |
04 Jul 2014 04:40 PM |
|
The quote for gunite and shotcrete depends upon the thickness of the coat, type of finish and whether it is a wall or ceiling. Various finishes are available. Overhead work costs more. The quote will usually include materials and labor, except for reinforcement. Placed concrete is usually less costly than gunite or shotcrete for a floor or roof. Using white cement instead of gray may double the price.
Be sure to determine which finish the quote includes. A finish requiring more man hours will cost more.
I would be curious about the price per square foot you get for walls and ceilings. Maybe you could e-mail me the prices so I can compare for my area.
Some spray concrete companies travel nationally and also to the islands.
I have conceptual window buck drawings I can share with you. |
|
Residential Designer & Construction Technology Consultant -- E-mail: Alton at Auburn dot Edu Use email format with @ and period . 334 826-3979 |
|
|
jonr
 Senior Member
 Posts:5341
 |
04 Jul 2014 06:11 PM |
|
It would be interesting to know how hard it is to learn to do a good job with something like this: http://www.gunitesupply.com/gunite-machine-c-10sl.php
|
|
|
|
|
TLP
 Basic Member
 Posts:207
 |
05 Jul 2014 07:50 PM |
|
Alton, it that your blog and build? Read about the history of the terms here: http://en.wikipedia.org/wiki/Shotcrete
"Shotcrete has emerged as the all- inclusive industry term to correctly
describe "pneumatically applied concrete" - either by the wet or dry
process. The term "Gunite" is a noun (product name) and should not be
used as a verb (as in, to "gunite" something). As Per the American
Shotcrete Association (ASA) the correct terminology is "shotcrete - wet
mix" or "shotcrete - dry mix."
I've talked to GCT if you go down there they will train you how to shoot their mix. They also have crews around different states that will train your local trades if need be. $$$ Yep, local pool industry good place to start.
I also talked to Richard in CO: http://simsbuilt.com/SCIP_System.html He has both made his own panels then decided it was not worth it now purchases.
For a one-off job this is going to be expensive especially if you need to train someone to shotcrete. You can hand trowl, have a work party with family and friends you can shoot the first scratch coat with a hopper you rent locally, you can make your own mix as many like Richard have proven no issues. I'm looking at production homes so heavy equipment makes more sense since the moment gets going to make it more cost effective.
I'm looking at shooting or casting my own mortar mix since there are better ones out there than concrete, far better! I think it is important to understand local resources as part of the design phase, design to your local trade capabilities and available materials.
The SKIP structure and moment of inertial is that of an I-beam and far superior compared to ICF as stated in the ref blog above. It also out performs ICF thermally, better as dynamic mass. If you use the right mix it will also provide dynamic humidity control. Why ICF is growing in popularity is just baffling!
As far as tornado and hurricane proof, I was just at Pigler, NE recent EF4 tornado last week doing some research. The CMU and brick walls held up to the bond beam then buckled in and blew the stick roofs off, flat concrete roofs do well. High pitched gabled roofs create a load point at the apex and are more prone to being hit from flying debri (2 X 4 @ 100 mpg, etc) studs make no sense in these alleys. Mass does, dome roofs create evenly distributed loads just as an aft pressure dome in a pressurized aircraft. These alleys need to loose the love for gable steep roofs and put lives first. Hip roofs with internal corner radii are next in line, 4-6:12. That could be stick there are still strawbale homes built in the 1900's 300 mile to the west of Pilger, in NE (church and homes in Arthur, Alliance, NE) with low pitch hip stick roofs still standing after seeing tornado's, extreme temps, winds, hails, etc....mass roofs would be better if they are skinned into the walls and monolithic like SCIPS, no mortar bricks and bond beams. Basements last but the best ones are not view or walk out with big windows.
Hurricane and tornado "proof" impossible when a semi lands on your home. I seen one home with two semi trailers on it they were just unlucky but, we can do 'resistant' ...ballistic studs are one of the biggest threats. TX tech as some test videos on that mass concrete does well over 4" thick. Guam has homes built back in the mid 1900s cast-in-place low pitch concrete roofs and walls still standing. It does not have to be shot.
|
|
|
|
|
Alton
 Veteran Member
 Posts:2157
 |
05 Jul 2014 08:46 PM |
|
That is not my blog or build. I have been following the blog for some time. I have assisted in designing and building with Insteel panels some years ago. (Insteel panels were made in Georgia - not much freight for shipping to east central Alabama. I think the panels are now made in Mexico.) The panels referenced in the blog were site built. |
|
Residential Designer & Construction Technology Consultant -- E-mail: Alton at Auburn dot Edu Use email format with @ and period . 334 826-3979 |
|
|
Alton
 Veteran Member
 Posts:2157
 |
05 Jul 2014 09:10 PM |
|
I failed to mention that re-mobilizations can add to the quote. Even if all of the panels are installed, a second trip may be required to add the second coat to the ceiling. I say this because some panel companies will not want the finish coat added to the ceiling until the roof slab has gained sufficient strength to support itself without shoring. Unless the spray crew is local, there will probably be a re-mobilization charge. I have seen re-mobilization charges range from $700 to $1500.
Here is the lowest quote for gunite that I have seen lately in my area. This does not include the panel, installation or re-mobilization. Walls = $2.70 per square foot for each side of the wall for a total of $5.40. Ceilings = $4.00 per square foot.
Thicker concrete will cost more since the quote includes labor and mix.
Another crew usually places the concrete roof slab.
I suspect that quotes will vary according to the area. |
|
Residential Designer & Construction Technology Consultant -- E-mail: Alton at Auburn dot Edu Use email format with @ and period . 334 826-3979 |
|
|
TLP
 Basic Member
 Posts:207
 |
06 Jul 2014 08:48 AM |
|
Void
|
|
|
|
|
TLP
 Basic Member
 Posts:207
 |
06 Jul 2014 08:51 AM |
|
<!--[if gte mso 9]>
The SCIP build process needs no shoring, the light weight
panels and steel stabilizes the walls and roof well enough to be shot. If you
need the scratch coat to be stable before the finish coat the steel gage is too
thin per span. If you watch the many videos out, the finish coat s/b done the
same day as the base scratch coat and there should be no “re-mobilization
charge”. Perhaps some panel company’s
mix takes longer to dry than others. Gypsum (plaster of pairs) accelerates
drying and stabilizes soils, there are other accelerators for commercial grade
concrete but, that should not be necessary with a skilled crew and mix. One
could change the finish mix if the finish grew is struggling to keep up with
the shotcrete application.
This is where it gets complex where to put the $. ORNL
showed a 4" thick interior mass to produce lower heating and cooling loads
than 2. You can run their mass calculator that compares mass effect DBMS to
stick frame energy loads in a home close to your climate zone, and read their
test reports. If designing solar passive, the south interior walls may benefit
from more thickness as in green house effect. Whereas the rest of the interior
is being used to stabilize hot-cold spots may not need to be as thick. The
exterior needs to be thick enough to breathing in hot-cold air, so 1.5-2"
depending on how drastic temps fluctuate in your climate zones. The foam
thickness needs to prove a thermal break between the interior and exterior mass
as in breaths in what is preferred to be a 12 hour lag time. You can find
Engineering out there on all this but I would not trust it, it is too costly
and complex to model. Structurally, the skins can be design to take load or not
allowing a difference in thicknesses.
Alton: How does your wall cost stack up to mainstream
stick and what percentage wall cost of total cost? Considering you don't need
drywall, paint perhaps, cladding, vapor barriers, trim, rain screen,
insulation, etc...I'll have mine soon after I interview a “shotcreter". Have
you built a SCIP home yet?
Remember "gunite" is a noun or product not a
verb. The "pool" industry makes a distinction, not residential. The
wet mix is preferred to reduce rebound or waste, and is the preferred method based
on many successful builds on the internet, etc. The dry mix process is useful in repair applications when it
is necessary to stop frequently, as the dry material is easily discharged from
the hose. Shotcrete – Dry Mix will require more skill and will harder to
find…. (Read the link I posted). At the end of the day, the method chosen will
depend on the skill set available in your local area.
Here is a hopper: http://blog.buildfast.com/2009/11/hopper-sprayers-great-tool-to-plaster.html
<!--[if gte mso 9]>
Normal
0
false
false
false
EN-US
X-NONE
X-NONE
|
|
|
|
|
Alton
 Veteran Member
 Posts:2157
 |
06 Jul 2014 11:11 AM |
|
I have limited experience with SCIPS - meaning just a few projects. My role was limited to designing, consulting and building with SCIPs. I found working with SCIPs can be very demanding but easy to learn. Troweling the wet mix and shoveling rebound is not easy labor when done in hot weather. Been there and done that. I have reached the age where my current activities are now limited to designing and consulting. I still make field inspections but try not to get involved with the actual labor. I do encourage clients to use a qualified spray crew with a certified nozzle man.
I do not know how the cost of SCIP walls compare to stick building. The homeowners select the technology and then I assist them in the design and building with the selected technology. As a consultant I have no vested or financial interest in the selected technology. I just try to help the homeowner/builder get what they want. It is up to them to make price comparisons. Sometimes the selected technology will change after quotes are received. In those cases, either I or the architect will modify the plans for the latest selected technology. I work with various technologies such as ICFs, SIPs, SCIPs, stick-built, etc. The pricing is done by the homeowner or builder. Oftentimes I do not know the cost, unless I happen to see a quote.
Sorry, I cannot help you with price comparisons but feel free to share. I try to learn new things every day.
GCT roof panels require support on four to 6 feet centers until the roof slab has gained sufficient strength. The support can be either temporary shoring or permanent beams.
I would really like to know more about not having to use shoring to support the panels during the spraying of concrete and placing of the roof slab. Not having to rent two and three story shoring and avoiding re-mobilization charges would really help to make the SCIP technology more competitive. I think more homeowners would insist upon SCIPs if the cost was less.
Notice that I used the term "spraying of concrete". I used this term so it would include placing concrete or mortar mix with air pressure regardless whether the mix is dry or wet or the pressure was low or high. Some countries already use the term "sprayed concrete" to distinguish it from placed concrete. |
|
Residential Designer & Construction Technology Consultant -- E-mail: Alton at Auburn dot Edu Use email format with @ and period . 334 826-3979 |
|
|
TLP
 Basic Member
 Posts:207
 |
06 Jul 2014 06:08 PM |
|
IF GCT needs temporary supports every 6 feet we have a prob Houston. What will happen when the supports are removed is the skins will see a pre-load since that load has to go somewhere. That pre-load or deflection ends up putting the inner skin in tension which is how cracks occur. I would suggest not more than 1/8 deflection per 4-foot, otherwise the steel gage needs to increased. I would expect more of a problem at the panel interfaces where the hog ties are. If you are seeing large deflection add some rebar to take them out. The way these things should be engineered as roof panels especially is, deflection based on dead and live weight, no one size will fit all. All the mortar or concrete should do is carry load between the wire mesh from the roof to the foundation smoothly(no kinks), seal the envelope, provide mass effect. The skins also add stiffness to the composite sandwich construction or create a high modulus of elasticity. The w-trusses carry lateral loads between wire mesh at the skins to resist bending and reduce foundation loads. 8" of foam would provide a better aspect ratio of width to height or wall foot print on the foundation to resist buckling. That is why straw bale construction, which is similar in concept expect, the loads are distributed better due to more reactive mass (16-18" walls), where as SCIP the bulk of the load should be transferred through the steel matrix in a 8-10" wall. So, in conclusion, it is possible to design without any shoring and the steel grid should hold true configuration prior to shotcrete and after. If the inner skin is cracking, and I would shoot it first, after the outer roof is shot then the panels can not even take dead loads or further live, bad design stop, rethink it since the skins will crack sooner or later, especially if you are in a cold climate zone subjecting them to large thermal cycles. Concrete is not that ductile, especially high levels of portland cement. Cure accelerators are the answer to faster drying time for scratch coats. SKIP will never make it in production design if the finish coat cannot go on in a day or two, preferable same day. Despite all the claims how skips has high tolerances that straighten themselves out with shotcrete, well don't believe everything you read. I bet GCT wants to keep panels cheap so they can sell, so they size the steel gage for general use pushing shoring to the builder. If their design requires supports every 6 ' make them permanent and watch deflection as you build.
Our "mainstream" around here is 2 x 4 framing, we'll put together a baseline cost so we can compare. I want to validate this myth that better construction techniques cost more since I don't believe it. There are some cost most don't consider like zero utility bills if you know how to get there, but I read some banks are starting to use it to qualify home loans.
|
|
|
|
|
TLP
 Basic Member
 Posts:207
 |
07 Jul 2014 07:41 AM |
|
Here is a SCIP home that only had $1500 worth of damage from other stick homes in Crystal Beach, TX after hurricane IKE in 2008: http://www.aspillc.com/docs/information.pdf When I emailed FEMA recently asking what design guides are available to withstand hurricanes and tornados at the whole house level they said there are none it is impossible, you need a bunker storm room to be completely safe follow their guides. True, but there are things as proven by this SCIP build and many others that they could point builders to be more resistant. Flying studs has no place in these locations they fail to mention they are the biggest threat. If all the homes were built like this, this home would have very little to no damage. This homes biggest threat is its neighbors. Our government must be making some big money from the wood building industry to keep quiet. Moore, OK, I wrote the city developer and informed them of a SCIP build and others like straw bale per new IRC 2015 code, Guam, etc, have not heard back yet. Now here is a town that didn't learn from the 2011 massive destruction rebuild from wood that was destroyed again in 2013 massive loss of property and lives, go figure! He did say there was interest in ICF but it is not as structurally sound as SCIP as I explained in detail in the email I wrote him. They do have some new code that homes have to withstand a EF2 and that is all wood will take. I guess they choose to ignor the EF5's that kill. This developer probably has no control over what people choose and the lack of knowledge, that is going to take getting the word out to the general public and getting codes approved to make it happen. A dome roof is best, next a hip with large fillets radii that can be made with mesh in a SCIP roof easy. |
|
|
|
|
Lbear
 Veteran Member
 Posts:2740
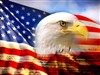
 |
07 Jul 2014 02:17 PM |
|
Posted By TLP on 07 Jul 2014 07:41 AM
Here is a SCIP home that only had $1500 worth of damage from other stick homes in Crystal Beach, TX after hurricane IKE in 2008: http://www.aspillc.com/docs/information.pdf Our government must be making some big money from the wood building industry to keep quiet. The timber industry has a lot of power and lobbyists in Washington. No doubt that catastrophic weather events like this are a big money maker for them as people rebuild using the same failed techniques as they did before. I guess they never read The Three Little Pigs book in grade school. The timber industry send out a fleet of reps anytime a tornado, hurricane or flood hits an area. There are millions of dollars to be made. SCIPs, ICF and other concrete systems are not represented properly like the wood industry is. What is "green" about building a wood frame home only to have it get knocked over every 10-30 years and what is the embodied energy of having to rebuild all the time? What about the cost of human life? In that photo you linked, there is another home in the background that is still standing. Do you know what it was built out of? |
|
|
|
|
You are not authorized to post a reply. |
|
Active Forums 4.1
 |
Membership: |
 |
Latest:
dliese |
 |
New Today:
0 |
 |
New Yesterday:
0 |
 |
Overall:
34724 |
 |
People Online: |
 |
Visitors:
96 |
 |
Members:
0 |
 |
Total:
96 |
|
|
|