|
One that didn't work out.....
Last Post 28 Jul 2007 08:54 AM by Mark Ross. 22 Replies.
|
Sort:
|
|
Prev Next |
You are not authorized to post a reply. |
|
photogman
 New Member
 Posts:10
 |
|
|
Cattail Bill
 Basic Member
 Posts:206
 |
01 Mar 2007 07:51 PM |
|
It appears from the article someone made a bad decssion in regards to consolidation I would question how much of an expert they are!!!!! Any one can claim that they are an expert but the proof is in the pudding. This was not the fault of the product but it was human error always vibrate, it does prove the point that most of us have made in the post that we have sent in. |
|
|
|
|
yogia
 New Member
 Posts:42
 |
01 Mar 2007 10:38 PM |
|
Hi photogman:
As stated in the article, decision not to vibrate the concrete was made at the job site without the concurrence of the design professionals. The decision to tear down the structure in my opinion is premature and at the moment an emotional reaction.
Even if the voids have been discovered in the concrete at some spots, it needs to be determined how extensive are the voids -- has the load carrying capability of the walls been impaired to the extent that the walls will not be able to carry all the intended dead and live loads.
I hope the decisions will be made rationally after making detailed analysis regarding the strength of the walls as-built. And I hope the needed repairs will be made in a cost-effective manner and the project would be put back on track. It is too bad that even if the project can be saved, it will take herculean effort to complete the project by the desired completion date because of the legal wrangling and the liability issues.
Problems do occur but it takes a great project manager to cut through the chase, come to a sensible solution, have every one buy into that and move on. Delays, and long completion times with ICF construction are common, and even though these problems are not unique to ICF construction, it is too bad that people have begun to associate these problems with ICF construction.
I am currently associated with a residential project where in addition to the issue of voids, the walls being out of plumb is a major issue and the home-owner demanded that the house be torne down. The shell is complete, even some finishing work had begun. It is a shame that instead of looking at the situation realistically and solving the problems, some times the emotions can flare up and rational thinking takes the back seat. This case has gone to arbitration. |
|
Regards!<br>Yogi Anand, D.Eng, P.E.<br>Energy Efficient Building Network LLC<br>http://www.energyefficientbuild.com |
|
|
PanelCrafters
 Advanced Member
 Posts:680
 |
01 Mar 2007 10:51 PM |
|
Wow, that is amazing. What where they thinking?
Posted By yogia on 03/01/2007 10:38 PM It is too bad that even if the project can be saved, it will take herculean effort to complete the project by the desired completion date because of the legal wrangling and the liability issues. Not likely, the College World Series starts in late May/early June. So, my guess is that the schedule was already a big issue. And, I love this:
Architect Leon Lauver: Workers from the Omaha offices of Terracon, an engineering consulting firm, tested the compressive strength of the concrete in the hotel's walls, Lauver said.
"The walls are of the proper strength," he said. "We just need to take care of the voids." Sorry, don't buy it. The concrete is of the desired strength, but that has nothing to do with the actual strength of the walls themselves. Unless they actually tested the walls. And, how would one do that? |
|
....jc<br>If you're not building with OSB SIPS(or ICF's), why are you building? |
|
|
James Eggert
 Basic Member
 Posts:411
 |
02 Mar 2007 07:50 AM |
|
yogi I dropped you a PM about your current situation. |
|
Take Care<br>Jim<br><br>Design/Build/Consulting<br>"Not So Big" Design Proponent |
|
|
walltech
 Basic Member
 Posts:390
 |
02 Mar 2007 08:25 AM |
|
Have too agree with Yogia on this one, it appears emotions may have gotten in the way. Without pictures we really can't pass to much judgement, but if a engineering firm has checked the compression and the concrete's up to par then a high psi grout mix will surely fix the problem. Surely doesn't help the ICF industry any but voids are always blown out of proportion.
Walltech |
|
|
|
|
vermaraj
 New Member
 Posts:34
 |
02 Mar 2007 11:19 AM |
|
Sounds like the business issue is getting tangled into the structural issue. They are trying to get this built in time for a specific event. In most cases either the project owner would take out continuity insurance or the primary contractor would take out a non-performance bond to protect the event cash flows that most likely underpin the financing of this project.
The insurance company and the bond company will bloody each other in an attempt to avoid paying out. When you add in the cost of 100% verifiable inspection of the reinforcement encasement and the inability to get future insurance on a tainted building, this thing is coming down.
Black eye for the ICF industry for no good reason. If this was standard concrete forming there would be no debate about whether or not to consolidate. |
|
|
|
|
photogman
 New Member
 Posts:10
 |
02 Mar 2007 01:48 PM |
|
This fiasco brings me to the question, what can I do to avoid what happened here. Ego's often tend to get in the way of things. When I had my home built I'm living in in 1983, the concrete man(flat work and conventional cement block) said he had been doing it for 25 years. Is it possible he could have been doing it wrong for 25 years?? Not trying to be funny, but everybody likes to eat and keep their bills paid. If you're looking for a contractor to do ICF they're not going to say that they're no good and can't do a good job. They all are going to bring up their good aspects because they are human and trying to land the job just like the next guy. Sooooooo, what exactly do you look for in a contractor when you plan to go ICF and what questions do you ask? Thanks! |
|
|
|
|
Cattail Bill
 Basic Member
 Posts:206
 |
02 Mar 2007 04:22 PM |
|
Probably the most important is to ask for references! The next thing is to ask some of the questions that we have already given you the answers to and see what kind of response you get, that in it self should be evidence of the contractors ability to give you a good product or not. If you really want to be sure that the job is done correctly you can inspect for voids well at least for major voids. How that is done is at night preferablly overcast skies, take a high intensity work light form the inside of the foundation and move it in a grid pattern up and down the wall moving about 3' over every time you make a vertical run. Have some one on the outside watching for light to show through the forms (it will! This is how we found voids on a project we where called in on to fix the incompetance of another contractor). This did not show us any partail voids only the ones that went all the way through. For the most part an experianced contractor will always consolidate a wall and you should be in good hands. |
|
|
|
|
yogia
 New Member
 Posts:42
 |
02 Mar 2007 08:03 PM |
|
Hi photogman: "When I had my home built I'm living in in 1983, the concrete man(flat work and conventional cement block) said he had been doing it for 25 years. Is it possible he could have been doing it wrong for 25 years??"
Very astute observation ... this brings the point home -- practice makes permanent and not necessarily that practice maked perfect!
----------------------------------------------------------------------------------------------------------------------------------------------------------------------------------- Here is something we can all learn from ... Following is a drawing and a photograph of what was allegedly built -- COEngineer had posted this on eng-tips.com I gave this picture a befitting title ... Needed Good Drawings And Contractor With Common Sense ----------------------------------------------------------------------------------------------------------------------------------------------------------------------------------- So, we need to have our act together from every angle -- and there is no substitute for the right knowledge and skill. |
|
Regards!<br>Yogi Anand, D.Eng, P.E.<br>Energy Efficient Building Network LLC<br>http://www.energyefficientbuild.com |
|
|
jredburn
 New Member
 Posts:51
 |
02 Mar 2007 08:44 PM |
|
Photogman, I have been in the business of repairing concrete for over 30 years and can state flatly that the house can be repaired and certified by a PE thaqt is structually sound. Wheather the cost would be excessive or meerly high is a matter of budgets and opinions. If the existing concrete was not structually strong the solution would be to tear it out and replace it or if it was all deficient, then tear the whole thing down. There are established proceedures for this type of problem that have been codified and tested by various agency's over the years. The statements that the outcome will be determined by emotion rather than reason is probably accurate. Sticking a small vibrator down in the form would have prevented this whole mess. If they had paid one man for an hour it would have been cheap insurance. Regards, Joe
|
|
|
|
|
woulfcc
 Basic Member
 Posts:147
 |
04 Mar 2007 01:31 AM |
|
If you look a little harder into this google the add and you can see what is the real problem.
If you sell a form in your back yard to a non-trained and installer, you, the seller are wrong!
Come out with it own up to the problem, we are here to help the whole industry and you will grow with it. If more jobs go this way the icf name and your name will get hurt. Sale forms to certified installers that have been trained on what can go bad if you play with the standard methods on placing concrete. Just sell block ,to any one and this is what will happen over and over again, how long will you stay in demand like this. Price does not equal value. You get what you pay for. What do I know I just pour concrete for a liveing? |
|
Changing How the World BUILDS!<br>Green , Done , Easy<br>Woulf c.c. of Wisconsin |
|
|
PanelCrafters
 Advanced Member
 Posts:680
 |
06 Jul 2007 06:53 PM |
|
I visited Omaha this week, and the structure is still there, abandoned and surrounded by a chain link fence. I didn't have a camera handy, or I would've gotten some pics. It looks like they stopped after 2 or 3 floors, and the height of the elevator shaft(it looked like cinderblock) indicates that they had at least another floor to go.
Even if they punt, it's still going to cost some decent bucks to destroy it and haul away the debris. It is not a small building!
Also a bit of trivia: This hotel may actually be in Carter Lake, Iowa instead of Omaha! |
|
....jc<br>If you're not building with OSB SIPS(or ICF's), why are you building? |
|
|
Mark Ross
 New Member
 Posts:73
 |
12 Jul 2007 12:17 PM |
|
Okay, I guess its time to post on this.
Having investigated and provided expert testimony on many failed ICF projects, completion of numerous reparative measures reports, provided chapter 17 special inspections, compiled research reports on ICF's and written install manuals for ICF manufactures, I think I can safely state the following.
Although the product "self consolidating concrete" works well in wood forms, of which have a release agent sprayed on them, as well as having a very limited about of obstructions for placement, such as the "ties" used to hold the forms together, ICF's have one major concrete placement disadvantage.
Consolidation
John Gadja's recent consolidation in ICF report, clearly states that external means of consolidation (pounding on a wall eg), or no consolidation does results in voids. This is based on actual placement tests conducted by the PCA in ICF's.
Research conducted by myself on installed projects, for many different brands, and with many different installers proves one thing. Proper consolidation techniques by internal vibratory means, is a must to ensure several concerns with consolidation.
Skip the voids, they are obvious and easy to find, go on to an issue I have termed "graveling".
This results due to several issues particular to ICF forms, and is primarily only found in ICF forms. It primarily occurs at the bottom of a wall section that is being poured, and is usually the result of additives that attach to Portland molecules’. And there are many additives that can cause this. You know you are in trouble, and need to do something, if the forms become coated in a grey "Maalox" type coating. This coating is a mixture of your Portland and fine aggregate, and due to the extensive exposed plastic area on the inside of the wall (remember this includes the tie area). AS the concrete is placed, (most people simply dump it in), the falling coarse aggregate of the concrete mass impacts reinforcing steel and ties, effectively spraying the walls and components with the Portland and fine aggregates that "stick" to the forms and components, leaving the coarse aggregate to arrive at the bottom of the form prior to any real "filler" of Portland and fine aggregate. This situation can be exacerbated by dry, windy conditions creating static attraction.
Basically, the result is that the lowest portions of the wall pour, usually the bottom 2-4 inches, is simply, very loosely bound coarse aggregate, with voids between the individual larger aggregate components. In effect, your structural wall is now sitting on a pile of ball bearings, contained by the non structural ICF forms.
BTW this is a very, very common issue, so even though an investigator finds no open voids, they overlook the lowest portions of the pour, usually located at the floor or foundation line, and in the case of many wood floor systems in ICF's, behind the ledger and band boards used for floor support.
So although an ICF wall looks good and sounds solid when tapped or pounded, it very well may not be. These situations are difficult to repair, structurally inadequate, allow water infiltration which exposes reinforcement to rapid deterioration or "rusting", and often results in post construction movement such as backfilling lateral movement at the footings, or simply spreading of the lowest portions of upper wall sections.
This, my friends, is the biggest reason to consolidate your walls, I have had to condemned and remove ICF structures for this issue, a few times now, and once the finishes are on, the repair bills are usually close to 75% of the construction costs, as you have to access both sides of the wall to repair, and that is IF it is repairable. I know of several contractors, who are out of business because of this "gravelling" issue. Don’t let it happen to you.
I can say that I have been working on ways to solve concrete placement issues in ICF's, and what I show below is what works best, and solves all issues, however requires additionally training to understand.
Although many people laugh and say we are crazy for pouring a standard mix, using only 5/8" crushed granite (no river rock, and in many cases we have to import our material), at 4.5" slump max, and using 1.5" plus diameter vibrators....consider this. We completed a project, in which the poured wall strength was 3,000 PSI. Core drilled and compression tests, 3 months later peaked over 9,000 PSI.
There is a trick to placing concrete such as this, but the great thing about the placement technique, is that it is cleaner, easier and faster than you would think.
Is it true.... Yes, on a large project, same day, identical walls, identical openings, I had an 11 man crew insisting that my way was incorrect and difficult. So I ordered their 6-1/2 slump concrete with pea gravel and water reducers. They took 5 hours to pour and consolidate 200' straight wall, 3 hours to clean up and align, with bulging issues, form failures and line/plumb issues....again with eleven men (five very qualified).
That same pour I took my 5 man crew, my mix, placement and consolidation methods, and completed the other identical 200' wall sections including clean up and alignment, before they where done their 3 hours of cleaning up and straightening their walls.....Again with less men.
In short, Installation of an ICF is difficult at best, it involves knowledge and skiils in trades such as carpentry, concrete forming, blockwork, reinforcing placement and concrete placement. Dont be mislead by "simply stack and pour". There is a lot more to it than you would expect.
For those that were a part of the “experience” on the site for the pour I spoke of above, please post your opinions, I would really like people to understand that there is a better way, even if it is a bit “off the wall”.
Mark Ross www.powersmartbuilding.com |
|
|
|
|
icfblocks
 Basic Member
 Posts:202
 |
15 Jul 2007 08:32 PM |
|
It was a great experience, working on the project that Mark refers to in his post. We poured about 2300 yds. of concrete in abt. 1.5 miles of walls and 65,000 sq. ft. of floors. All of that in about 100 days. We had the opportunity to strip walls and look at the results of the pours Mark referred to. The things revealed were eye opening. We used vibrators as large as 2.5" on 5" walls. The gravelling that Mark refers to can occur between lifts in a wall also. Because of the experience I have several size vibrators on the job. We "punch vibrate" narrow columns and places that, due to web and steel placement, we recognize as problematic. We "punch vibrate with the smallest vibrator available usually 7/8" or 1". We stick it right through the foam into the concrete going up the pour to assure proper consolidation in tight places.
It is my hope that all ICF professionals learn to use internal vibrators and the salesmen selling ICF,s refrain from telling people that internal vibration is optional. |
|
Thanks,<br>Tom<br>www.advbuildingtech.com |
|
|
dmaceld
 Veteran Member
 Posts:1465
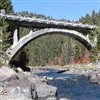
 |
17 Jul 2007 11:04 AM |
|
Tom & Mark,
Have you guys by chance prepared any kind of report documenting your findings? This sounds like very valuable information that ought to be captured, and not lost, for the good of the entire ICF industry.
Mark, do you have a link to the John Gadja report? I would like to get a copy of it.
I plan to pass along all this information to the guy who's going to do the concrete for me on my house. He hasn't poured ICF before but is very concientous about quality and doing jobs right. His price reflects it. He prides himself on never having had a call back on a concrete job, except once when the customer insisted he pour the slab her way. He told her it would crack badly, and sure enough it did! We will have an ICF builder on site for guidance and direction.
|
|
Even a retired engineer can build a house successfully w/ GBT help! |
|
|
fturkdal
 New Member
 Posts:27
 |
18 Jul 2007 05:35 PM |
|
I will not recomend new ICF users 4.5 in slump concrete with narrow cavity ICF block.
Frank |
|
|
|
|
icfblocks
 Basic Member
 Posts:202
 |
19 Jul 2007 08:14 PM |
|
The experiments we did in the motel were done to further the training of the ART crew members. Many of the things we do are not for "new icf users" or the faint of hart. There has been documented testing done concerning the use of internal vibrators. There is nothing like a "hands on" experience to bring it home. People are still being trained how to install ICF,s in "one day classes", most of which either choose to ignore the subject of consolidation or mention some sort of external attempt to consolidate which is a big mistake. |
|
Thanks,<br>Tom<br>www.advbuildingtech.com |
|
|
dmaceld
 Veteran Member
 Posts:1465
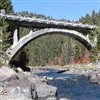
 |
19 Jul 2007 08:31 PM |
|
Posted By icfblocks on 07/19/2007 8:14 PM The experiments we did in the motel were done to further the training of the ART crew members.
Is that ART as in ART of ARIT.com, which has gone belly up? |
|
Even a retired engineer can build a house successfully w/ GBT help! |
|
|
icfblocks
 Basic Member
 Posts:202
 |
20 Jul 2007 05:00 AM |
|
Not "belly up", just split up! Better to have all the facts. |
|
Thanks,<br>Tom<br>www.advbuildingtech.com |
|
|
You are not authorized to post a reply. |
|
Active Forums 4.1
 |
Membership: |
 |
Latest:
johnmcd |
 |
New Today:
0 |
 |
New Yesterday:
0 |
 |
Overall:
34739 |
 |
People Online: |
 |
Visitors:
60 |
 |
Members:
0 |
 |
Total:
60 |
|
|
|