|
attaching Hardie Plank tp ICF forms
Last Post 07 Apr 2013 09:43 PM by sailawayrb. 30 Replies.
|
Sort:
|
|
Prev Next |
You are not authorized to post a reply. |
|
|
sailawayrb
 Veteran Member
 Posts:2274
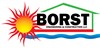
 |
17 Mar 2013 02:11 PM |
|
I wouldn't expect the vertical TF System ICF panels to have any significant advantage over horizontal ICF blocks in windy construction conditions. Perhaps it would be easier to simply replace any damaged vertical TF System ICF panels than having to rebuild a wall in order to replace any damaged horizontal ICF blocks. Building with ICF in windy conditions is always best avoided and usually can be avoided. In those areas where it difficult to avoid windy construction conditions, better contractors will often do panelizing for those ICF products that support this approach (and TF Systems is one of the companies that does) or will plan to not use ICF. Panelizing Sounds like the fastening issue is more associated with clapboard siding than with the actual ICF foam and not unique to TF System ICF either. I would expect the 3x10 T&G cedar log siding we plan to use won't have this issue (photos attached). Given the remote location, our construction logistics call for first completing the garage/shop (which also has detached living space) prior to constructing the main residence.
 |
|
Borst Engineering & Construction LLC - Competence, Integrity and Professionalism are integral to all that we do! |
|
|
Travel
 New Member
 Posts:41
 |
23 Mar 2013 06:37 PM |
|
I think the best way to install hardi plank siding is to use the foam ADHESIVE that is used which is very good and use a roofing gun to secure to the fastening strips.It works glue holds very well |
|
|
|
|
sailawayrb
 Veteran Member
 Posts:2274
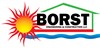
 |
06 Apr 2013 05:37 PM |
|
|
|
Borst Engineering & Construction LLC - Competence, Integrity and Professionalism are integral to all that we do! |
|
|
dmaceld
 Veteran Member
 Posts:1465
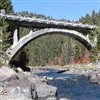
 |
06 Apr 2013 09:53 PM |
|
Posted By sailawayrb on 06 Apr 2013 05:37 PM
Relative to fastening Hardie Plank, they recommend shooting ring nails. For most other siding they recommend screwing GRK cabinet screws (8 x 1/3/4").
When I built my house with Hardie plank on ICF, I did some experimenting with ring shank and spiral nails. I found that spiral nails had a lot more holding power than do ring shank. I couldn't pull the nails out without ripping up the Hardie first. The main reason appears to be that ring shank nails tend to fill the grooves with the material they are passing through, giving them essentially a smooth shank once all the way in. The spiral shank turn as they go in, kind of like screws do. Ever try dismantling a pallet? They're nailed together with spiral nails. Gotta be a reason for that!  Spiral nails are available for coil siding guns, but you have to look to find them. |
|
Even a retired engineer can build a house successfully w/ GBT help! |
|
|
dmaceld
 Veteran Member
 Posts:1465
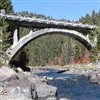
 |
06 Apr 2013 10:08 PM |
|
Posted By sailawayrb on 06 Apr 2013 05:37 PM
Well, I took the TFSystems training. I found it to be excellent and I am even more impressed with their vertical ICF products and their support than before. Attached are some photos of the their products.
From what I see in the photos it looks like that particular configuration is about 4" foam on the outside and 1" on the inside. A couple of thoughts come to mind about that. One, I wonder how the cost of all the additional plastic studs, in order to have the wiring space, compares to the cost of equal foam inside and out, less plastic webbing, and running wiring and plumbing in grooves in the inside foam. Also, going back to the discussions about foam on the interior vs. exterior according to the Oak Ridge modelling, it sure looks to me like whatever thermal mass benefit is derived by the lesser foam on the interior would be lost due to the insulating effect of the air space between the wall board and foam. The Oak Ridge model is based on a solid stack up of siding, foam, concrete, foam, dry wall. Any air space in the stack up is going to throw those analyses out the window. What's your thinking about the total final cost of the TF wall in the photo above vs usual ICF blocks? |
|
Even a retired engineer can build a house successfully w/ GBT help! |
|
|
sailawayrb
 Veteran Member
 Posts:2274
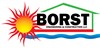
 |
07 Apr 2013 12:15 AM |
|
That configuration is 5" exterior and 3/4" interior and what was apparently used on Pensmore. They use solar collectors to heat the walls and use Geo to cool the walls in Pensmore. They have a zero inch option for the interior (removable plastic pans) and you can specify whatever you want for the exterior. They apparently determined that they needed the 3/4" to actually slow down the heat transfer into the house. It is okay to have air space in the assembly, but you certainly have to include it in your heat transfer analysis just like every other material. Air space R-value depends on the emittance of the air space surfaces, but a 3.5" vertical air space with horizontal heat flow is about an R-value of 1. Their foam is 4.6 per inch so 5" is 23 R-value and 3/4" is 3.45. So you are looking at about a 5/1 internal/external heat transfer ratio with this configuration. With the zero inch option (even with the 3.5" air cavity) you can obtain ratios in excess of 20/1. So this seems like the perfect ICF product for those of us who properly design buildings with thermal mass. Relative to cost, their standard vertical ICF (2.5" foam on both sides) is comparable to standard horizontal ICF. Their high end Pensmore vertical ICF product is currently about twice the takeoff cost than their standard product, but when you factor in the concrete, it is only about 35% higher per square foot of wall. I posted the takeoff/estimate details someplace here recently for both their standard and high end products, but I can't seem to find it at the moment. You are not limited to 4' lifts and can apparently pour full height 12' walls with their high end product. It should be relatively easy to achieve straight, square, and plumb walls with both products given the vertical panels, lower/upper channels, and bracing approach. They claim they didn't have a single failure pouring Pensmore and stayed within 1/8" dimensionally. Both look like excellent products, but I will reserve final judgment until after I use them for a couple buildings. |
|
Borst Engineering & Construction LLC - Competence, Integrity and Professionalism are integral to all that we do! |
|
|
sailawayrb
 Veteran Member
 Posts:2274
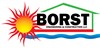
 |
07 Apr 2013 12:32 AM |
|
Okay, found it...here's the takeoffs and ROM estimate: ICF Walls: (36' X 2) + (56' X 2) = 184' X 12' height = 2,208 SF Conservative Estimate of Concrete & Rebar: 2,208 SF x 0.5’ / 9 = 123 Yards x $100/Yard = $12,300 TFSystems ThermoForm Takeoff: $6,464 (without Concrete & Rebar) Total (without Labor): $18,764 / 2,208 SF = $8.5/SF TFSystems TransForm Takeoff: $12,795 (without Concrete & Rebar) Total (without Labor): $25,095 / 2,208 SF = $11.4/SF
|
|
Borst Engineering & Construction LLC - Competence, Integrity and Professionalism are integral to all that we do! |
|
|
dmaceld
 Veteran Member
 Posts:1465
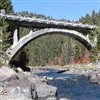
 |
07 Apr 2013 03:10 AM |
|
Posted By sailawayrb on 07 Apr 2013 12:15 AM
It is okay to have air space in the assembly, but you certainly have to include it in your heat transfer analysis just like every other material. Air space R-value depends on the emittance of the air space surfaces, but a 3.5" vertical air space with horizontal heat flow is about an R-value of 1. The numbers I find show the R value of 3.5" air space more like 5 to 6, not 1. Is the air in the vertical air space allowed to convect into and out of the space, i.e., are there vents at the top and bottom of the wall? If that is the case then I can see where the thinner foam on the interior will help with the thermal mass benefit. If the air is trapped in the space then it is a significant insulator. I was of the thinking that the less foam on the interior increases the thermal mass benefit by a combination of conductance from the wall surface into the room air, then of course carried throughout the room by convection, and by radiation from the wall surface. The air space in the TF wall will kill the radiation from the concrete into the room. Thinking back to the graphs I showed in an earlier thread about the relative benefits of interior mass vs exterior mass according to the ORNL model, I am skeptical, without doing an economic analysis, that the added cost of the TF system you show would be repaid in energy savings in a reasonable time period. As an aside, radiant heat transfer in a house structure is not a well studied subject, other than in the realm of floor heat radiation into the living space. When I was designing my house I tried to come up with an estimate of the heat loss by radiation from the floor to the ground below in the crawl space. I found only one paper several years old on the subject, and I couldn't transfer the info in it into a reasonable assessment of the heat loss number I was looking for. |
|
Even a retired engineer can build a house successfully w/ GBT help! |
|
|
cmkavala
 Veteran Member
 Posts:4324

 |
07 Apr 2013 08:59 AM |
|
Posted By dmaceld on 07 Apr 2013 03:10 AM
Posted By sailawayrb on 07 Apr 2013 12:15 AM
It is okay to have air space in the assembly, but you certainly have to include it in your heat transfer analysis just like every other material. Air space R-value depends on the emittance of the air space surfaces, but a 3.5" vertical air space with horizontal heat flow is about an R-value of 1. The numbers I find show the R value of 3.5" air space more like 5 to 6, not 1. Is the air in the vertical air space allowed to convect into and out of the space, i.e., are there vents at the top and bottom of the wall? If that is the case then I can see where the thinner foam on the interior will help with the thermal mass benefit. If the air is trapped in the space then it is a significant insulator.
I was of the thinking that the less foam on the interior increases the thermal mass benefit by a combination of conductance from the wall surface into the room air, then of course carried throughout the room by convection, and by radiation from the wall surface. The air space in the TF wall will kill the radiation from the concrete into the room.
Thinking back to the graphs I showed in an earlier thread about the relative benefits of interior mass vs exterior mass according to the ORNL model, I am skeptical, without doing an economic analysis, that the added cost of the TF system you show would be repaid in energy savings in a reasonable time period.
As an aside, radiant heat transfer in a house structure is not a well studied subject, other than in the realm of floor heat radiation into the living space. When I was designing my house I tried to come up with an estimate of the heat loss by radiation from the floor to the ground below in the crawl space. I found only one paper several years old on the subject, and I couldn't transfer the info in it into a reasonable assessment of the heat loss number I was looking for.
dmaceld, according to many resources, air spaces ....1/2" thru 4" are equal to 1 |
|
Chris Kavala<br>[email protected]<br>1-877-321-SIPS<br /> |
|
|
dmaceld
 Veteran Member
 Posts:1465
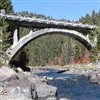
 |
07 Apr 2013 08:06 PM |
|
Posted By cmkavala on 07 Apr 2013 08:59 AM
dmaceld, according to many resources, air spaces ....1/2" thru 4" are equal to 1
I stand corrected.  Doesn't alleviate my concern about the impact on the thermal mass benefit by having that air space between the concrete and the living space. Here's a quote from the Conclusion section of the ORNL report about thermal mass benefit. Thermal mass layers must be in good contact with the interior of the building in these walls. |
|
Even a retired engineer can build a house successfully w/ GBT help! |
|
|
sailawayrb
 Veteran Member
 Posts:2274
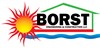
 |
07 Apr 2013 09:43 PM |
|
Yes, ASHRAE tables indicate about 1 R-value for 0.5" to 3.5" wide air space for the emittance range under consideration here. When it comes to passive solar and thermal mass design, most of the info published isn't worth the paper used to publish it. I can't comment specifically on the ORNL report as I haven't read it, but I will try to do so when I can find some time. Heat transfer on the other hand is a very well understood engineering discipline and it can always be readily determined with a very high degree of accuracy. Yes, if you are thinking of using thermal mass in the classical/historical/passive sense as a means for irradiance absorption, heat storage, and subsequent heat release, you would certainly use the zero inch interior (removable pans...photo attached) and not purchase/install the 3.5" interior cavity option. Our designs have evolved well beyond what I would term "passive thermal mass" to take advantage of what you can accomplish by using "active thermal mass" which has PEX embedded in it. Yes, it is always best to "collect" irradiance by allowing the photons to directly strike the thermal mass as you indicated. When you get aggressive about collecting irradiance using an active thermal mass approach, you then also need the ability to store (or just reject) the excess solar heat that occurs during clear sky days. Having lots of high mass concrete walls that have a high internal/external heat transfer ratio provides a less complicated way (e.g., less complicated than say using water tanks) to accomplish this. In essence, you use the excess solar heat to actively increase the effective R-value of the walls to reduce the building heat loss during the non-irradiance period. Controlled/predictable building heat loss reduction is just as good as controlled/predictable building heat gain.
 |
|
Borst Engineering & Construction LLC - Competence, Integrity and Professionalism are integral to all that we do! |
|
|
You are not authorized to post a reply. |
|
Active Forums 4.1
 |
Membership: |
 |
Latest:
jcardenas555 |
 |
New Today:
2 |
 |
New Yesterday:
1 |
 |
Overall:
34731 |
 |
People Online: |
 |
Visitors:
129 |
 |
Members:
0 |
 |
Total:
129 |
|
|
|