jimexcelcs
 New Member
 Posts:8
 |
08 Dec 2014 09:11 AM |
|
Greetings! This forum has been an invaluable resource for researching modern building practices. Thank you.
I'm starting construction on a new home (North Alabama) very soon. I've decided on SuperiorWalls for my walkout basement and am looking hard at SIPs construction for my home.
The home is 1800 heated sq ft main level and 1100 in the walkout basement (53 linear feet of exposed wall on walkout basement) plus a 25x25 garage.
The home is a modern design with "shed" style roofs that nicely lend themselves to vaulted SIPs construction.
I have one estimate from a contractor for 100% stick construction as follows.
Framing materials $32,000
Misc material-nails $1,717
Framing labor $25,000
Insulation: $3,000
Total: About $62000.
My SIPs estimate came in at $56,000 including vaulted roofs and delivery. But I will have to add to that the cost of the uninsulated 25x25 garage which will be of stick/truss construction - I'm guessing 6 to 10k? I also have to add the cost of interior walls to that. Another 3 or 4k perhaps?
So, about 68k total to build my house out of SIPs compared to 62,000 for stick construction.
But for that additional money, I get no surprises - I know what the cost will be ahead of time. I get a much higher R value (R23 for walls, R30+ for roof) which reduces the tonnage for AC and, of course, heating/cooling bills.
Plus, the house is "dried in" in two days shaving weeks off construction time which will save money in loan interest.
Am I missing anything here? The two quotes I've received so far seem to be high. Are my quotes about what you'd expect?
Attached is a file with the mail level and basement on one page. |
Attachment: plan_small.jpg
|
|
|
|
|
richm
 Basic Member
 Posts:107
 |
08 Dec 2014 11:09 AM |
|
Hi Jim, No attachment has shown up! Does the SIP pricing include installation? Are all of the prices with or without the floor framing? What type of SIPs? Metal, OSB? RichM |
|
|
|
|
Alton
 Veteran Member
 Posts:2157
 |
08 Dec 2014 11:13 AM |
|
Would you mind telling us which SIP company gave you the quote? |
|
Residential Designer & Construction Technology Consultant -- E-mail: Alton at Auburn dot Edu Use email format with @ and period . 334 826-3979 |
|
|
jimexcelcs
 New Member
 Posts:8
 |
08 Dec 2014 11:17 AM |
|
Sorry, Rich. The SIPs price includes delivery and crane/setup. I would have to supply the laborers. They are 4.5" OSB SIPs. Stupid me, I had not considered that the "stick" price includes flooring. The SIPs quote does NOT include flooring. That makes the price difference between SIPs and sticks even wider. Don't know that I can justify that. The SIPs quote was only one quote from one highly-recommended SIPs provider that is within 2 hours driving time from my location. I'm expecting other quotes soon. I can't see how to attach a JPEG to this message. |
|
|
|
|
jimexcelcs
 New Member
 Posts:8
 |
08 Dec 2014 11:22 AM |
|
Alton, the provider of my quote was SipsOfTheSouth dot com. The constructed a house in my area (Florence) and the owners are singing their praises. I've also been impressed with their level of service thus far but I *think* their prices are considerably higher than I anticipated. |
|
|
|
|
richm
 Basic Member
 Posts:107
 |
08 Dec 2014 06:21 PM |
|
Jim, Can we assume that the SIP roof panels are thicker than the 4.5" wall panels? RichM |
|
|
|
|
jimexcelcs
 New Member
 Posts:8
 |
08 Dec 2014 07:22 PM |
|
richm, Yes, the roof SIPs are 8.5" thick (R30ish) as opposed to the 4.5" walls (R17ish). |
|
|
|
|
acobb
 New Member
 Posts:30
 |
09 Dec 2014 05:05 PM |
|
Jim, Some thoughts to help you along the way: You've chosen a "superior" basement system that has similar High-Performance attributes as does a SIP system. I'm willing to wager that you can find a significantly cheaper basement in poured walls or CMU. Therefore, how do you justify the Superior walls system over the inferior competition and not see at least the same advantage of SIPs over sticks? You have chosen wisely with SOTS. They are both reputable and capable. Keeping that in mind, when you get competing quotes, I urge you to verify similarities in all quotes. Are you being quoted a fully CNC fabricated package with lumber? Do all quotes include drawings, delivery, installation accessories, and installation assistance? One of the advantages of dealing with a "Full Service" dealer like SOTS is that you get a complete package. Your dream of a smaller and more affordable HVAC system will only be realized if you engage a third party to do energy modelling and create a equipment sizing specification. Without that piece of the puzzle, you are at the mercy of "Old school Rules of Thumb"! The secret to sizing is to use a professional who understands high performance and approved modelling software. In furthering my above point, I wonder if you have spoken to a HERs rater yet. If not, you're stacking the deck against yourself before the job even begins. If you have begun a relationship with a rater, you are aware of all the good things they can offer including proving similarities in performance. What I'm saying is that your rater can define a level of performance that your stick framer should match so that you are comparing apples to apples. Let's see if your framer is willing to commit to meeting the 2015 MEC and guaranteeing a blower door test of less than 2 ACH@50. I'm willing to bet he wouldn't touch that specification with the material and labor number that he has already quoted. Lastly, why are you (Like so many others) looking at "first cost & not "total cost"? Unless you plan to build and sell the house within a few years, you are ignoring the biggest advantage of a SIP structure. You SAVE money every month in utility costs over code minimum stick framed house. Hence, if you run the numbers of a mortgage (I'm assuming you're not paying cash for this house) you will usually see that an upfront increase in building cost converted to a monthly payment is less than the utility savings created by your intelligent choices made right now. OK, this is lastly as well. You will not dry that house in in two days with a SIP package! If you want to know what else you're missing, we can talk about: the green addendum proper appraisals for high performance homes energy efficient mortgages proper ventilation etc. Regards, acobb
|
|
|
|
|
raqqasa
 New Member
 Posts:1
 |
11 Dec 2014 09:52 AM |
|
Also, If you take out the Sip roofs and put a roof truss system on your house instead - where does that bring your cost? Are the R values of the traditional built house and the SIP walls similar? Are you looking at thermal bridging? I'm currently going through the same price quote process .... looking at ICF's or Superior Walls for my Walkout basement and SIPS vs Traditional Stick for my home. I'm heavily leaning towards SIPs because I do plan on living in this home for 15+ years. |
|
|
|
|
jimexcelcs
 New Member
 Posts:8
 |
12 Dec 2014 01:57 PM |
|
"Lastly, why are you (Like so many others) looking at "first cost & not "total cost"? " I don't think I stated I was looking at "cost first." I have a budget that I cannot exceed. My research tells me that SIPs ought to cost "about " or "a little more" than stick but with extraordinary benefits. My first quote was at least double the cost of stick construction and that goes against everything I've read. Fortunately, I have found a couple of other suppliers that are in line with what I expected. My last quote was from Panel Wright and was more than 20k less expensive. "If you take out the Sip roofs and put a roof truss system on your house instead - where does that bring your cost? " The roof panels on my first quote are about 20k.. That would be a vaulted roof that is already insulated, of course. My truss quote comes in a 5k for the trusses. To that, I have to add insulation (perhaps $500 for 1800sq ft?) and osb sheathing (25 sheets) about $1000. Total truss material cost of $6500. Gonna have to add a little labor to both but, as it stands now, truss construction will save me at least 10k. BUT! Some of my numbers are quite jibing. I think the first quote overestimated the roof square footage. They have 3800 sq ft and I only have 2400 sp I'm studying that a little more. Another quote I received suggested that if I use trusses for my roof, I could still use "single sided" (nailbase) SIPs panels. However, I am not seeing the benefit of those sips versus a simple assload of insulation above sheetrock in a truss system. So, the journey continues. Thanks all. I'll still be post here as I get more info.
|
|
|
|
|
Lbear
 Veteran Member
 Posts:2740
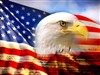
 |
12 Dec 2014 06:54 PM |
|
Cheapest route = truss roof with blown in cellulose Where SIPs rule over truss systems is: - SPEED - one can have a fully enclosed & insulated roof within 2-3 days vs weeks or months later with a truss system
- STRENGTH - trusses are toothpicks in high winds vs SIPs which are 3-4 times stronger
- AIR TIGHTNESS - much harder to seal a truss attic space
- CONDITIONED ATTIC - no need for gable, attic, ridge, soffit vents
- CATHEDRAL CEILINGS - the proper way to insulate and seal a cathedral ceiling
- INSTANT SOFFIT/OVERHANGS - no need to frame out and build soffits, SIPs make instant soffits
The above points is what you pay extra for in a SIP.
|
|
|
|
|
jonr
 Senior Member
 Posts:5341
 |
15 Dec 2014 11:36 AM |
|
It's not clear to me what happens to OSB roof SIPs after the asphalt shingles get old (or any other leak) and the OSB rots here and there. |
|
|
|
|
Lbear
 Veteran Member
 Posts:2740
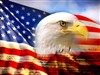
 |
15 Dec 2014 04:56 PM |
|
Posted By jonr on 15 Dec 2014 11:36 AM
It's not clear to me what happens to OSB roof SIPs after the asphalt shingles get old (or any other leak) and the OSB rots here and there.
The goal of any roof sheathing is to keep it dry. SIPs are no different. The roof underlayment is key. Asphalt shingles are not supposed to be the water barrier. The underlayment is supposed to do that. Peel & stick is the best choice for keeping the roof sheathing/SIPs dry and rot free. |
|
|
|
|
cmkavala
 Veteran Member
 Posts:4324

 |
15 Dec 2014 07:30 PM |
|
Posted By Lbear on 15 Dec 2014 04:56 PM
Posted By jonr on 15 Dec 2014 11:36 AM
It's not clear to me what happens to OSB roof SIPs after the asphalt shingles get old (or any other leak) and the OSB rots here and there.
The goal of any roof sheathing is to keep it dry. SIPs are no different. The roof underlayment is key.
Asphalt shingles are not supposed to be the water barrier. The underlayment is supposed to do that. Peel & stick is the best choice for keeping the roof sheathing/SIPs dry and rot free.
Actually ....... shingles (properly installed ) are the primary water barrier, the underlayment is the "secondary" water barrier |
|
Chris Kavala<br>[email protected]<br>1-877-321-SIPS<br /> |
|
|
acobb
 New Member
 Posts:30
 |
16 Dec 2014 10:44 AM |
|
Actually.... Chris is right about the shingles and the advice to use peel and stick is only applicable in the deep South. Without a clear understanding of building science that's geographically applicable, you can often be mislead by on-line forums such as this. Placing a vapor barrier (Peel & Stick membrane) on the wrong side of your assembly is a really bad idea! Regardless of the type of panel, trapping moisture in your assembly can lead to all types of moisture related issues. Al Cobb SIPschool.org training and consulting for the SIP industry |
|
|
|
|
jonr
 Senior Member
 Posts:5341
 |
16 Dec 2014 11:17 AM |
|
Peel and stick would be safe with a vented design (another OSB layer above the SIP). How does it work when you remove old shingles - does the P&S get damaged and need replacing too? Of course adding a vent/gap and P&S starts to up the cost even more (as compared to a vented attic/truss/cellulose/OSB/tar paper/shingles design). |
|
|
|
|
Lbear
 Veteran Member
 Posts:2740
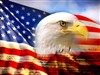
 |
17 Dec 2014 12:53 AM |
|
Posted By acobb on 16 Dec 2014 10:44 AM
Actually.... Chris is right about the shingles and the advice to use peel and stick is only applicable in the deep South. Without a clear understanding of building science that's geographically applicable, you can often be mislead by on-line forums such as this. Placing a vapor barrier (Peel & Stick membrane) on the wrong side of your assembly is a really bad idea! Regardless of the type of panel, trapping moisture in your assembly can lead to all types of moisture related issues. Al Cobb SIPschool.org training and consulting for the SIP industry
SIP roofs CANNOT breathe or dry to the exterior once you place a standing seam metal roof on them. So it makes sense to use a peel & stick membrane underneath the metal roof since it will protect and seal the OSB from water infiltration. |
|
|
|
|
acobb
 New Member
 Posts:30
 |
17 Dec 2014 10:05 AM |
|
Lbear, your original comment about using peel & stick was used in conjunction with asphalt shingles. In that scenario, (without back-ventilation and in the majority of North America) you have offered bad advice as it relates to SIP assemblies. A peel & stick membrane acts as a vapor barrier as it has zero permeability. Therefore, if we follow your specification and the codes requirement of a vapor barrier (SIP tape) on the inside in all climate zones north of Florida, we have the worst of all possibilities. Zero capacity to dry! You have designed an assembly with a vapor barrier on both sides! I agree that a standing seam roof (Or any other non- self-ventilating cladding) that is installed directly on the roof assembly greatly reduces the assemblies ability to dry. However, it's capacity is not reduced to zero until we apply peel & stick. The detailing of installation MUST be geographically driven. A standing seam roof in Georgia may work very well applied directly to the SIP. However, in Vermont the reduced capacity to dry would suggest an installation detail that uses some form of back-ventilation. Once again, your blanket statement does not qualify a climate zone or the applicable building science. The proper detailing of any high performance assembly pays as much or more attention to drying than it does to keeping bulk water out. By definition, a high performance wall or roof assembly has a "Reduced Capacity to DRY" because of the air-tightness associated with maximum energy efficiency. In climate zones 4 and above, one must be very careful with the detailing to create an environment that promotes drying. The use of self-ventilating cladding and/or back ventilating is the best way to ensure durability of the structure and eliminate moisture related problems. This discussion is equally applicable to all types of SIPs and all types of assemblies. I stand by my statement that it's a really bad idea unless you're building in a climate zone that does not require a heating system. In that case, your vapor barrier goes on the outside of the structure and your assembly can dry to the inside. Al Cobb SIPschool.org training and consulting for the SIP industry |
|
|
|
|
Alton
 Veteran Member
 Posts:2157
 |
17 Dec 2014 10:05 AM |
|
Regarding roof construction: http://www.buildingscience.com/documents/insights/bsi083-mea-culpa-roofs/view?utm_source=Building+Science+Corporation+List&utm_campaign=8b06c95e02-BSC+Newsletter+Issue+%2375&utm_medium=email&utm_term=0_194890bc8c-8b06c95e02-63876805 |
|
Residential Designer & Construction Technology Consultant -- E-mail: Alton at Auburn dot Edu Use email format with @ and period . 334 826-3979 |
|
|
jonr
 Senior Member
 Posts:5341
 |
17 Dec 2014 11:22 AM |
|
What little research I found suggests that a standing seam metal roof does allow small amounts of air flow (ie, isn't an effective vapor or air barrier). It's not like the metal is glued to the decking and the seams are caulked. Same for asphalt shingles. |
|
|
|
|
Lbear
 Veteran Member
 Posts:2740
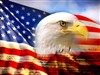
 |
17 Dec 2014 11:27 AM |
|
Posted By acobb on 17 Dec 2014 10:05 AM
A peel & stick membrane acts as a vapor barrier as it has zero permeability. Therefore, if we follow your specification and the codes requirement of a vapor barrier (SIP tape) on the inside in all climate zones north of Florida, we have the worst of all possibilities. Zero capacity to dry! You have designed an assembly with a vapor barrier on both sides! This discussion is equally applicable to all types of SIPs and all types of assemblies. I stand by my statement that it's a really bad idea unless you're building in a climate zone that does not require a heating system. In that case, your vapor barrier goes on the outside of the structure and your assembly can dry to the inside. Al Cobb SIPschool.org training and consulting for the SIP industry
Al, At 4" - 6" closed sell (polyurethane) or even open cell (polystyrene) core on a SIP has basically ZERO permeability. The latter EPS has a little more permeability but the polyurethane at that thickness is basically almost ZERO in terms of permeability. Therefore, a SIP design like that CANNOT dry to the interior even if it wanted to. That is why I am confused by your statements. You stated, " Zero capacity to dry! You have designed an assembly with a vapor barrier on both sides!"Unfortunately, that is the SIP described in my paragraph. Such a SIP has ZERO ability to dry because the 6"+ of closed cell PU foam or 8-10" of open cell PS foam is basically a vapor barrier. The vapor barrier is inherent in the SIP design itself due to the vapor impermeable core sandwich. The only way around it is to use a core with 4" - 6" of EPS and even so, the vapor drive through that will be so miniscule that it would take forever for something to dry out and rot would occur if the OSB got wet. The ONLY solution that building scientists will agree on (if that is even possible since they argue between themselves about this issue quite often) is to create another OSB layer above the SIP and leave a 1/2" air space between the SIP and the extra layer of OSB. The problem with this is the very expensive costs $$$ it adds to a SIP roof. Nobody would want to spend that type of money on a SIP roof and then have to build another roof above the SIP roof. SIPA doesn't push that because they would go out of business as would any other SIP industry related company. What kind of sales push would that be if you told the buyer they have to build 2 roofs $$$ if they use a SIP for their roof. Good luck selling that. So where we disagree is that you claim SIPs are vapor permeable even with a 4" - 6" PU core or 8"-10" + of PS cores. I believe you are 100% wrong. Show me the studies that vapor drive will occur with 4" - 6" of closed cell polyurethane and/or 8-10" of open cell polystyrene. |
|
|
|
|
Lbear
 Veteran Member
 Posts:2740
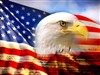
 |
17 Dec 2014 11:47 AM |
|
CLOSED-CELL POLYURETHANE CORE:
Water Vapor Transmission ASTM E96 0.7 perms @ 1.5"
PER BUILDING SCIENCE STUDY:
Closed-cell (about 2 pounds per cubic foot density or more) spray foam applied in thicknesses of over 2” (50 mm) will control vapor diffusion to safe levels in all climates up to 10000 HDD and interior winter-time relative humidities of up to an over 50%RH. As thickness increases the level of diffusion control increases.
Therefore a 4 - 6" roof SIP with PU has a vapor impermeable core.
Now all we need is the stats on 8 - 10" of polystyrene cores and what the water vapor transmission perm rate is for 8 - 10" of EPS. Anything < 1.0 perms is considered a vapor barrier by IRC.
|
|
|
|
|
acobb
 New Member
 Posts:30
 |
17 Dec 2014 05:24 PM |
|
Lbear. I thought we were talking about drying potential and applying a vapor barrier to the cold side of a roof assembly. Now you want to change the course of the conversation to permeability? OK First, EPS is a closed cell foam. Yes, you are correct that the thickness of any closed cell foam will result in a perm rating that cause it to act as a vapor barrier. "Therefore, a SIP design like that CANNOT dry to the interior even if it wanted to. That is why I am confused by your statements." You seem to suggest that drying has to be through the entirety of the assembly. When in fact, the outer layer need only to dry towards an environment that is, itself, dryer than the skin. Hence, if the inside skin needs to dry to the inside it doesn't need to permeate the entire core. Only the skin itself. Same is true with the outside skin. " The vapor barrier is inherent in the SIP design itself due to the vapor impermeable core sandwich." With a vapor permeability of .1-1.0, it's classified as vapor semi-permeable. Yes this qualifies as a vb but the industry, the code,and anybody who's done a blower door test knows that the Achilles heal of the system is the joints. If the joints are not properly sealed, vapor is allowed to enter the assembly and potentially migrate to a cold skin on the opposite side. And, since we both know that vapor travelling on air leaks is a thousand times more likely to carry vapor than it is by means of permeability, I fail to see your position behind arguing about perm ratings. " the vapor drive through that will be so miniscule that it would take forever for something to dry out and rot would occur if the OSB got wet." So you want to further delay the time it would take to dry by adding P&S so that moisture damage occurs faster??? "The ONLY solution" - "is to create another OSB layer above the SIP and leave a 1/2" air space between the SIP and the extra layer of OSB." Not so at all. There are many methods to enhance drying that are both effective and affordable. But, None of them work if we let you put P&S directly to the SIP! "Good luck selling that." Not only do I sell it, but I install it, I teach it, and I show my clients how to do it with an eye towards durability, increased thermal performance, and increased sound isolation. It's a win,win,win. "So where we disagree is that you claim SIPs are vapor permeable even with a 4" - 6" PU core or 8"-10" + of PS cores. I believe you are 100% wrong. Show me the studies that vapor drive will occur with 4" - 6" of closed cell polyurethane and/or 8-10" of open cell polystyrene. " I never made such a claim. However, any material above .1 still drys to some extent. What if the drying needs only to pass through the panel skin? Consider, if you will, the drop of moisture lay directly inside of the panel skin. Your concerns over foam permeability are moot. In that scenario, you need only to look at the permeability of the SIP skin. AND, if that drop of water found its way to that skin via air-transport and condensed on a cold skin, then fire your SIP installer and know that the drying can occur through the cold skin (albeit though slowly) or back the way it came via the improperly sealed gap that let it in in the first place. Again, foam permeability plays virtually no part in drying in either direction. Where we disagree is that I want a high performance assembly to DRY in any way possible. And you want to seal in the moisture with a method that violates the building code. Al Cobb SIPschool.org training and consulting for the SIP industry
|
|
|
|
|
Lbear
 Veteran Member
 Posts:2740
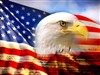
 |
17 Dec 2014 06:42 PM |
|
Posted By acobb on 17 Dec 2014 05:24 PM
Where we disagree is that I want a high performance assembly to DRY in any way possible. And you want to seal in the moisture with a method that violates the building code. Al Cobb SIPschool.org training and consulting for the SIP industry
So what is your solution/build-up of a SIP roof with a metal roof on top? Please don't tell me "building paper" because metal roofs with building paper underneath is a match made in hell... The only viable solution that is out there and recommended by BSC is adding a vented roof on top of the SIP. What is the going rate $$ of adding furring strips and another layer of OSB on top of a SIP and then adding the proper vent channel details? The truth is that SIP companies do a song and dance when it comes to this issue. They know the cost of SIPs is a negative to builders and if they have to mandate a cold roof design, that is adding injury to insult, a hard sale to make to home builders. |
|
|
|
|
scottucs
 New Member
 Posts:4
 |
23 May 2015 11:36 AM |
|
You might also take a look at the ThermaShell building system. It exceeds the R-values for SIPs, goes up even quicker than SIPs and is very resistant to wind (up to 173 mph), termites, mold and mildew. And you will benefit with reduced electricity costs for heating and cooling of up to 80%!
www.thermashell.com |
|
|
|
|
cmkavala
 Veteran Member
 Posts:4324

 |
23 May 2015 01:59 PM |
|
Posted By scottucs on 23 May 2015 11:36 AM
You might also take a look at the ThermaShell building system. It exceeds the R-values for SIPs, goes up even quicker than SIPs and is very resistant to wind (up to 173 mph), termites, mold and mildew. And you will benefit with reduced electricity costs for heating and cooling of up to 80%!
www.thermashell.com
scottucs, the product from what I can see does not exceed SIP R- values and will not be resistant to anything unless cladded with plywood, and at that point not resistant to termites? the technical specifications on the website are misleading making claims that they have an Energy Star" 5 star rating? Energystar does not give 5star ratings to building materials , They do give ratings to "whole house" buildings , of which, the insulation plays a small part of the overall rating, as does the: windows, doors, HVAC system, finished roofing, Hot water system, lighting, appliances and blower door results. "EnergyStar" is very touchy about logo misuse and false claims involving their name/ratings |
|
Chris Kavala<br>[email protected]<br>1-877-321-SIPS<br /> |
|
|
LMN
 New Member
 Posts:2
 |
11 Feb 2016 08:08 AM |
|
Hey Jim,
It's about 15 months since your original post. Please let us know what you decided to do, why, and how your project worked out (or is going). We are in a very similar situation and are most interested.
Thanks!
|
|
|
|
|
jimexcelcs
 New Member
 Posts:8
 |
11 Feb 2016 09:11 AM |
|
Hi LMN. I chickened out on SIPs but used SuperiorWalls for my basement. I'm pleased with both decisions. I was not exactly sure of some window placements in some areas of the home. SIPs have to be planned out and it's much harder to change window and door openings. Sticks allow for flexibility. I designed my own home and soe mistakes were not apparent until walls were erected. That would have been a nightmare with SIPs but no big deal with sticks. I also could never nail down a good cost comparison between stick and SIP construction. I'm pretty sure that IF I had done stick construction with 6" walls and sprayed in insulation, the SIPs wold have been comparable. One of the "problems" in my areas is that, here in North Alabama, our energy costs are far lower than elsewhere. So high-efficiency SIPs and spray insulation has a "payback" time measured in 15 to 20 years. Sorry, that's just not worth it for me but certainly may be for you. So, my home takes advantage of passive solar (still thinking about solar panels), R30 blown in the attic and standard fiberglass in the walls--but sealed up tight. |
|
|
|
|
LMN
 New Member
 Posts:2
 |
11 Feb 2016 10:28 AM |
|
Thanks for dropping back in with an update. The sips vs stick comparison is a point that is hard to put your finger on, especially if your utility costs are low. I found this study a fellow did in 2015 that evaluates that question (for a degree requirement it seems). He compared the sips vs stick in a couple of different locations and with several different residential designs - his conclusion is that sips cost more in almost every case due to the cost of the panels largely. He does have a nice little table near the end of the document that gives the price difference for each element of a structure (materials + labor) that's interesting. Seems to pretty thoroughly analyze the issues. It's located here |
|
|
|
|
sbatta
 New Member
 Posts:2
 |
30 Aug 2016 12:45 AM |
|
http://scholar.colorado.edu/cgi/viewcontent.cgi?article=2109&context=honr_theses |
|
|
|
|