Reward, Amvic, Logix, IntegraSpec or Nudura which ICF
Last Post 05 Jul 2013 04:16 PM by Roger R. 62 Replies.
|
|
Marc&Kem
 New Member
 Posts:50
 |
11 Sep 2008 07:03 PM |
|
Now we have the decision of which ICF to go with. I know there are many representatives of their product out there. Please, I am not trying to start an ICF battle based on bashing. I hope you can represent your product by facts such as block density, structural support (to prevent waves in the wall), locking design, wall blowout failure, cost and other facts based on data not hear say. Some people think that controversy bring knowlege to the top. I can agree if it's based on facts/data not emotion. My choices are: Reward, Amvic, Logix, IntegraSpec or Nudura. I look forward to your input and respect the experience you can provide. I can tell you Reward Wall Systems was recommended.
Thanks,
Marc and Kemella Athens, TN
|
|
|
|
|
|
wes
 Advanced Member
 Posts:810
 |
11 Sep 2008 07:28 PM |
|
I have used Logix since their creation as a company. And I have also used several other brands over the years, including a couple others that you mention. While these forms are all good products, I have always come back to the Logix. The combination of strength, ease of use, and consist quality can't be beat. Also, they would ship to you from their Johnson City TN plant, which should keep your freight costs down.
|
|
Wes Shelby<br>Design Systems Group<br>Murray KY<br>[email protected] |
|
|
ICFconstruction
 Veteran Member
 Posts:1323
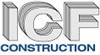
 |
11 Sep 2008 07:39 PM |
|
Can't go wrong with any of those, let your ICF contractor decide. Whatever they are most comfortable with is what they should use. |
|
Brad Kvanbek - ICFconstruction.net |
|
|
Paul Stevens
 Basic Member
 Posts:200
 |
11 Sep 2008 08:31 PM |
|
I agree with ICFconstruction, if you are going to sub out your ICf install, let the contractor decide. If you are going to tackle the install yourself, you will want to answer these questions, which company has a distributor close to you, can they provide tech. support, do they have enough bracing to handle your job, can they help with your permits, answering any questions the building dept. may have, if you need 3 more blocks do they have a warehouse close so that they can run them over in a pick-up or will you need to pay big freight charges? I install Logix and Nudura and are very happy with both blocks. Reward and Amvic appear to be very similar to Logix and have heard good things about them as well, but I don't know much about Integraspec. This topic has come up before and like those times you will get a different answer from everyone you ask. Try contacting a local redi-mix company and ask for a few names of the local ICF installers and ask them. You will probably get the best advice form those guys, they are probably teamed up with the guy who provides the best service to them. Thats the one I would go for. Hope this helps some. Paul Stevens |
|
|
|
|
TLC-ICF
 New Member
 Posts:98
 |
11 Sep 2008 11:02 PM |
|
We are in Cookeville, can drop ship Logix to your jobsite. Let me know if I can help. |
|
|
|
|
Raider Bill
 New Member
 Posts:75
 |
12 Sep 2008 09:22 AM |
|
I am building in Englewood TN. Used amvic. If you want to see the house let me know. All ICF work is done.
|
|
|
|
|
icfman
 New Member
 Posts:4
 |
12 Sep 2008 11:18 AM |
|
M & K in Athens, congrats on the icf building. ICF's in general perform like the installers putting them together. LOGIX is the choice we have made over other products in the 10 years building and installing with alot of other product we tried. Application and installation per manufacturer recommendations are key. Tech support, if your doing the work, is something to really consider. As with many things it is said, application, application...
|
|
|
|
|
Farmboy
 Basic Member
 Posts:356
 |
12 Sep 2008 06:46 PM |
|
M & K, Is the ICF work being contracted out or are you Doing It Yourself (DIY)? Then follow the advice from ICF Constr'n and Paul Stevens.
Here's an extensive ICF comparison chart: http://www.icfmag.com/documents/ICF_COMP_CHART/08_ind_comp_chart.pdf
Our story. We will erect the ICF walls of our upcoming home ourselves and will use Logix for several reasons: 1. Close to us. Block is made just about 40 miles from our home site. 2. Foam is 2-3/4" thick which gives us a higher R-value, total of 5.5" of foam. 3. Concrete is 6.25" thick, so a bit more strength. Think Kansas tornados. 4. I've seen several homes built with it during the construction phase and it is sturdy. 5. Attended distributor training and have helped a friend using it for his country home. 6. Have good working relationship with the distributor and they can provide all the bracing, accessories and tech support we will need.
Other Block We Considered. Eco-Block (2.5" foam, 6" concrete). Helped stack some block at a residence. Only problem for me is that you have to assemble the block on site. Advantage is that the block ships easier, but you need to ensure the ties are snapped in correctly and you have sufficient quantity.
Amvic. Seems to be a well received block and available locally.
Buildblock. Heard good comments about it. Used on an Extreme Home Makeover project.
IF you are DIY, might check out Fox Block (2-5/8" foam, 6" concrete). They are reasonably priced and are made and sold out of Omaha. I think the first truckload load is shipped free or used to be.
Reward Block (2.5" foam, 6" concrete). My wife and I helped construct the foundation and exterior walls for a home in Greensburg earlier this year. They used Reward Block which seemed fairly forgiving given that no one had much experience with ICF at all. Because we had attended the one day course a week or two before made us the "experts", but we got it done. Reward block is reversible which makes stacking a bit less complex. Just grab any corner block and use it. With Logix we will have to make sure we have it right side up.
Hope this might help you decide. Good luck, Dave |
|
|
|
|
woulfcc
 Basic Member
 Posts:147
 |
12 Sep 2008 07:10 PM |
|
The real question is are you the installer?
ALL the blocks in the right hand will work. (yes ,I said that)
All the blocks in new hands will have some problems.
You only get 1 chance to get your home right so pick your help , and let them pick the block.
This is true all over the icf product lines ,all can be put up wrong and have problems. They also in the hands of an experienced user can look and work just fine. So are you the installer? |
|
Changing How the World BUILDS!<br>Green , Done , Easy<br>Woulf c.c. of Wisconsin |
|
|
Marc&Kem
 New Member
 Posts:50
 |
13 Sep 2008 09:29 AM |
|
If we decide to go with an installer I agree it would be best to:
1. Choose someone with experience. 2. Let the installer choose the block 3. Talk with customers 4. Use an architech/Engr with ICF experience
After talking with you guys it seems like ICF's are kinda like purchasing a car. Today there are many good MFG's and they all have a decent product. But if I were to make one myself or have one made. I would want someone with experience, support and provide training with an onsite Rep. I feel more comfortable with a block that has strips every 6" Vs every 8". also the thicker foam is good if the density is there. I have not seen density over 1.5 I want to find some training. I think this will convince me whether to do it myself or hire someone. I have come down to 3 block manufactures Logix, Reward and Amvic. Dave , thanks for the comparison chart. Wow! that is a great tool. Paul, ICFman, Wes, TLC-ICF, farmboy, Raider Bill, Woulfcc & ICF Construction, I just want to say thanks! I feel like I have gotten some good unbiased info. Kinda of like the peace of mind you get from talking to a "friend" in the business. Now I need to find a training class in this part of the country.
Marc & Kemella Athens, Tn
|
|
|
|
|
renangle
 Basic Member
 Posts:302
 |
13 Sep 2008 09:31 AM |
|
M & K,
Here are my thoughts regarding the block in question:
Amvic - Ties are every 6" o.c., making it one of the strongest blocks on the market. They are reversible as well which takes a lot of guess work out of the build, especially with regards to coners. They have a manufacturing plant outside of Charlotte, so frieght shouldn't be too bad.
Logix - Ties are every 8" o.c., which probably isn't a big deal but it is something I would consider, especially if price isn't any different. They are not reversible, so there is more to take into account when building.
Reward - Ties are every 6" o.c. and they are reversible, so they compliment Amvic quite well. Also, from what I have read/heard they have developed a new corner which is one of the strongest being made today.
Nudura - Ties are every 8" o.c., so they go in the Logix category. Also, I have heard when unhinging them, there can be a slight bow in the block (also because of their length) which must be looked at when building. Their ties when stacking are extremely tight which is a good thing, but if you have to unhook them because of some error before pouring it is difficult.
IntegraSpec - I don't know enough about them to give you a great opinion.
At the end of the day, I believe it comes down to service. If you have a contractor that is comfortable with one because of experience, go with what they recommend. Another very important factor also is bracing. Many distributors offer brace rental or usage if you build using their block so out of the ones you mentioned if only one has bracing available, I would go with them. |
|
|
|
|
SoCalScott
 New Member
 Posts:91
 |
19 Sep 2008 01:29 AM |
|
M & K
The three forms youare looking at all perform the same way ( the differneces between these three forms are more or less aesthetic). If installed PROPERLY they will all give you straight plumb walls w/o blowouts. That is where service comes in. If you go with an installer - go with your four steps. If you decide to DIY, make sure you have local representation to consult with you during the process. make sure your ICF source has ICF bracing available for you to rent. Do NOT try to brace/scaffold with lumber.
Your local distributor should have inventory so that you do not have to worry about haveing extra forms or running short without a readily available supply.
So far sounds like you are on the right track!
|
|
|
|
|
wes
 Advanced Member
 Posts:810
 |
19 Sep 2008 07:04 AM |
|
SoCalScott, I have to disagree with you on your statement about not using lumber scaffolding/bracing. We started doing ICF walls before bracing systems were born, and wood was the only game in town. The system we use is simple, easy to use, and over 90% recycled into the project construction process. And when done properly, just as foolproof as the modern systems. I suppose if all we did were the ICF systems, I would be more inclined to the bracing systems, but considering that we are usually involved in the entire construction process, I cannot justify spending multiple thousands of dollars for a system that would not pay for itself during its usable life. |
|
Wes Shelby<br>Design Systems Group<br>Murray KY<br>[email protected] |
|
|
SoCalScott
 New Member
 Posts:91
 |
19 Sep 2008 08:03 PM |
|
Wes -
Understood, that part of my comment was for the DIY scenario, where the home owner would rent the bracing/scaffold system their project. If they were to hire a subcontractor, and the sub has sucessful experience using a lumber system, by all means go with what has worked. But on a one time basis for the unexperienced installer they are much more likely to get it done right by using the ICF bracing system.
Out here, they normally rent for $10 per set per "week" (with some latitude for what a week is). So on a typical project the cost for rental bracing would run $300 to $600, to cover 150 and 300 linel feet of wall, respectively. All depends on local distributor/availability.
Scott
|
|
|
|
|
Buddy Newberry
 New Member
 Posts:9
 |
06 Oct 2008 09:32 AM |
|
There seem to be a lot of individuals in the dark when it comes to IntegraSpec ICF. I would like to shed some light on this unique ICF Wallsystem.
In my opinion, after having used IntegraSpec exclusively for five years in custom home construction, it is the most versatile and user friendly ICF on the market today. It is an independant panel system which makes meeting specific wall height requirements and constructing RSO's a breeze. IntegraSpec is specified to have a 10' pour height as apposed to the 3' to 4' pour heights of other ICF's. The tallest pour I have done is 14' with a 6" concrete core cavity in one shot and one pass around the house. This system is completely flippable and reversible which makes installation quick and easy, there is no up or down, no right or left. There is absolutely no form compaction and no form lift, which means no gluing forms together, no tying them down, and no guessing, exact measurments for RSO's can be used. IntegraSpec has anti-compaction channels that negate form compaction and the webs lock together which in turn negates form lift. In combination, the anti-compaction channels and inter-locking webs create a spine throughout the wallsystem subsequently making the forms easier to plum and straighten during pours. The furring strips are every 8" on center and are 1 5/8 wide, these inserts are also made out of HIPS plastic and not polypropolene, which provides a better mechanical bond with the EPS, a pull test of 156 pounds per sq. inch and results in superior strength and taller pour heights. IntegraSpec has a patented H-clip which allows it to accomplish something that no other ICF's in the industry can obtain. This H-clip allows you to gang together multiple webs to achieve any concrete core thickness. The thickest wall I have poured was 24 inches and 8 ft tall, I was able to pour this wall in one shot, I was apprehensive at first, but couldn't believe the results. As well, IntegraSpec's IntegraBuck system is the insulated solution to window insulation and bucking around your RSO's. It is cheaper per lineal foot than PT wood, it insulates and has a furring strip within it to provide for window installation and jamb extensions. As well, in using this bucking system the wallsystem is a one material substrate for stucco applications. Finally, IntegraSpec has dovetail grooves on the inside face of their panels which creates a mechanical bond with the concrete as it cures and contracts. This in turn provides a superior surface for stucco or EIFs applications which awards IntegraSpec and Nudura (which have dovetails as well) extended warranties from many of the EIFs manufacturers. When using ICF's I always look at the cost of the blocks, IntegraSpec is not among the cheapest but in looking at how this ICF performs and the versatility of the product I consider these forms to be priceless. Installed cost is more important in the end, and with a flippable and reversible system that pours 10 ft, I save a lot of money in the installation process. It is very easy to have a good nights sleep when you feel confident and comfortable with the buidling system that you are using. Check out www.integraspec.com, it is quite an informative site with slideshows of feature projects and product brochures.
I hope this helps,
Buddy Newberry, |
|
|
|
|
renangle
 Basic Member
 Posts:302
 |
06 Oct 2008 10:58 AM |
|
Buddy, welcome to the forum.
I am curious of the statment regarding the HIPS plastic is stronger than polypropolene? A quick search from me found that the Amvic pull-out strength of 198 lbs./sq. in. where IntegraSpec is at 156 lbs./sq. in. Also, when pouring Amvic is listed with the strongest strength test at 865 lbs./sq.ft.
Also, one thing people like about the polypropolene is that its recycled material in most cases, I am unaware if the same can be said of the HIPS plactic. We have used a put together form before as an organization, but after studying all ICF companies, we went with a flat panel wall system as it was more efficient building material. Also, if Marc and Kem are going to build their house themselves, I would think a put together system may take more time. Again, depends on what their contractor recommends.
renangle |
|
|
|
|
ErVikingo
 New Member
 Posts:35
 |
06 Oct 2008 04:18 PM |
|
What about Quad Lock? |
|
|
|
|
John Clem
 New Member
 Posts:38
 |
06 Oct 2008 06:42 PM |
|
Hi Marc & Kem, I do not know if you have made a choice yet, but thought I would add my two cents. By the way, I am a Logix distributor. Logix is a very strong block and easy to work with. I do not believe the 8" vs 6" spacing is an issue. Logix does have a special web design incorporated into the outside corners. Gives extra attachment area. I do not know how the other blocks address this issue. Also, 41% of Logix blocks (by weight) are completely recycled. John |
|
Home Design<br> ICF Distributor<br> http://www.clemdesign.com<br> http://blog.clemdesign.com/ |
|
|
Paul Stevens
 Basic Member
 Posts:200
 |
06 Oct 2008 07:45 PM |
|
Buddy Newberry, don't take this the wrong way, but are you either an Integra spec rep or owner, you certainly sound like one? It is great to be passionate about your block, I certainly am.But please clarify a statement you made about Integraspec having a specified pour height of 10' and other ICF's of 3-4'. Pouring concrete to a specified height has nothing to do with which ICF you pour, if you check the building codes they will tell you that you shouldn't pour more than 4 feet every hour whether it be in an ICf wall or conventional panel walls. I have poured walls 16' high as well in Nudura, Logix, and Arxx if you are experienced and confident in the block you are using then pouring that height isn't a big deal. Paul Stevens |
|
|
|
|
Aaron McKinney
 New Member
 Posts:56
 |
06 Oct 2008 08:02 PM |
|
I haven't seen anyone mention build block yet.
|
|
|
|
|
woulfcc
 Basic Member
 Posts:147
 |
06 Oct 2008 11:18 PM |
|
On average I have been pouring around 100 yd. of concrete a week for about 20 + years.
Thats in a lot of different forms, not just icfs but wood , pans, decks what ever.
I work commercial construction mostly and thats what I do for a living.
I say this not to beat my chest but to let you know where my opinion is based from. Do you actual work with the concrete or sell stuff? I am not selling any thing here And I am not looking for work.
I love icfs they are so easy on the crew that is doing the build. Every man in the field I have put icfs in their hands like the ease of the stacking and see how this is a real assume way to build. All icfs. Hands down are a better way to build. I have used a lot of blocks and am always willing to work with a icf any one of them.
The icf form that I will use hands down over any one out on the market is integraspeck. If you look at the whole build it just works faster and cheaper the any other form out their. I don't get into bashing any one here, keep building with icfs they are the way to go. I don't make a dime on any icf here not in the last year any way. I just work with them. So what I heard from Buddy was PIN ON! I you think just anyone of the street can just stack and pour icfs and get it right all the time well Good luck to you! This is not to say that a hand man is not able to use icfs ( they can) Just know that sometimes people don't know what they don't know. In concrete that is dangeres.....things do go bad, can you fix it. Do you know how? Stop all the stack and pour stuff , put the block in the hands of the pros out in the feild.
|
|
Changing How the World BUILDS!<br>Green , Done , Easy<br>Woulf c.c. of Wisconsin |
|
|
EMM
 New Member
 Posts:7
 |
08 Oct 2008 11:18 AM |
|
I am curious of the statment regarding the HIPS plastic is stronger than polypropolene? A quick search from me found that the Amvic pull-out strength of 198 lbs./sq. in. where IntegraSpec is at 156 lbs./sq. in. Also, when pouring Amvic is listed with the strongest strength test at 865 lbs./sq.ft.
Also, one thing people like about the polypropolene is that its recycled material in most cases, I am unaware if the same can be said of the HIPS plactic.
renangle,
renangle,
Your perception on the HIPS plastic used in IntegraSpec is inaccurate. HIPS used in IntegraSpec is made of 100% repro.
For people wandering what HIPS means, here it is H= High, I= Impact, P= Poly, S= Styrene.
What buddy means, IntegraSpec use HIPS in their form because it is highly compatible with the EPS used for the panels fusing both materials together when being mold which make a stronger form.
Greenblock use to have the same HIPS plastic a while back making it to be a strong form as well. I know because we use to install it in the 90’s
As for the concrete free fall, that is another myth. See the attached document. Since we started using Greenblock & now IntegraSpec, we always filled our walls straight up. By filling them, the concrete is always flowing down & not dropping down.
Think about it, if you go around in lift, there is at least 2 to 3 lift. If you don’t pay attention, your are increasing the risk of cold joints between the lifts which create a weakness in the wall & on top of that creating possible water seepage point in the walls. Water is lazy & it will take the easiest route. Now if you have a water problem in your ICF walls, how do you find the problem spot???? |
Attachment: Free Fall of Concrete.pdf
|
|
|
|
Aaron McKinney
 New Member
 Posts:56
 |
08 Oct 2008 12:10 PM |
|
Guys; that's a good article. I would like to show that to every inspector that made us cut port holes because they were concerned about the height we were pouring from. I might like the idea of being able to pour in one lift, and I do like the idea of eliminating possible cold joints. I was taught to vibrate the lifts together, going through the most recent lift 1' into the lift underneath it to mix the concrete together, which as far as I know has worked well. I'm assuming that with all the weight from pouring in one shot it would allow you to not need to vibrate as much. Can you guys experienced in this give some more details?
|
|
|
|
|
Alton
 Veteran Member
 Posts:2157
 |
08 Oct 2008 12:19 PM |
|
EMM,
I read the attachment about the Free Fall of Concrete. Very interesting. Of course, this is opposite of what I was taught in school many years ago. Hopefully, I am not too old to change my thinking about how concrete behaves.
When you say you always fill the walls straight up, do you mean that most of the concrete is placed at one point. If so, do you have to add more bracing to counteract the fluid pressures at that point? Do you use superplasticizers that make the concrete more fluid? Please elaborate. |
|
Residential Designer & Construction Technology Consultant -- E-mail: Alton at Auburn dot Edu Use email format with @ and period . 334 826-3979 |
|
|
EMM
 New Member
 Posts:7
 |
08 Oct 2008 02:37 PM |
|
Posted By Alton on 10/08/2008 12:19 PM
When you say you always fill the walls straight up, do you mean that most of the concrete is placed at one point. If so, do you have to add more bracing to counteract the fluid pressures at that point? Do you use superplasticizers that make the concrete more fluid? Please elaborate.
Alton,
In our area the concrete plants have a specialized ICF mix which includes a type 2 superplastisizer & pea stone. The mix usually arrives on site at a 6 to 7” slump which flow nicely in the walls. It gives us plenty of time to pour & align our walls. Of course I move around while filling up the walls in one pass.
Believe it or not, since 1992, I can truly count on one hand the number of blow outs that I had in 16 years in ICF contracting. The worst part is, it was due to stupidity or trials/testing. The biggest advantage in using HIPS plastic, it gives you time to react do to the fusion between the two materials (HIPS/ties & EPS panels). I.e. if you see the form buldge while pouring you have time to move the pump without getting an actual blow out.
Aaron,
It happens to us on some occasion that an inspector requested us to remove pieces of foam at the bottom of the walls to see the concrete consolidation & one every occasion it was nicely consolidated. I will use a vibrator is in lintels & walls when we are dealing with quite of bit of rebar. |
|
|
|
|
Buddy Newberry
 New Member
 Posts:9
 |
08 Oct 2008 02:57 PM |
|
In regards to EMM's post and the attached article, this is a document I am quite familiar with and am very happy to see posted. As mentioned in a post before when pouring heights that are above the specified recommendations it is important that you are using a high-end ICF that you trust and feel comfortable with. The addition of more bracing is not required and additional vibration would be left up to the installer. This technique of pouring the walls full, eliminates cold joints and ensures a monolithic wall structure. The flowing of the concrete throughout the forms provides for better concrete consolidation, but this is not to say vibration is not needed or should be lessened. However, if your concrete has the right amount of additives and the slump is 6" or 7" you could choose to only vibrate in tight spots. This is not something I have attempted yet simply because I bought the vibrator...It hasn't failed me and I'm going to use it.
This way of pouring saves time and money in having the pump truck on site for two hours not five, and from what I have experienced it yields professional results with the elimination of added complications when pouring in lifts as EMM has pointed out.
EMM is exactly right in referring to my reference about HIPS plastic, I meant to say that the fusion of the HIPS with the Type 2 EPS creates a stronger mechanical bond between the two materials resulting in a strong form, which is one reason why I trust IntegraSpec. I trust that if there is weakness within the forms due to an installation error I will be able to recognize this point of weakness before a blow out and avoid it until the necessary strapping is applied. As well, I was unaware that HIPS was 100% repro, that is good to know. Buddy Newberry,
|
|
|
|
|
renangle
 Basic Member
 Posts:302
 |
08 Oct 2008 03:45 PM |
|
EMM,
I appreciate the clarrification on the HIPS, though I don't really see how it is that much stronger than other products mentioned before. The pull out test mentioned earlier states that it IntegraSpec is not as strong as others and the strength test of Amvic still stands by itself as the strongest as far as I have read. I have yet to see the hard data on IntegraSpec's superior strength. The data regarding Amvic can be found on the ICF comparison chart from ICF Builder Magazine.
I believe that all we need to look back to the initial question Marc and Kem asked (before the information changed), "please explain the differences between the blocks based on fact and not emotion". It appears to me that Marc and Kem are inexperienced to the ICF industry and would like their question answered as it was intened. Many of the earlier posts did just that and with regards to the historical intend of this forum, one should always try to be objective. Some may promote one block or the other, but for their particular job, most seem to agree that they should use the block that their contractor/subcontractor advises. Also that service should be a factor.
There are many experienced professionals on this forum who can pour a wall to the top in one pass as well as other things that many on this forum would be uncertain of doing. Stating that doing a pour in one pass (no lifts) could get a novice that reads this forum and believes that ICF construction isn't very difficult in a lot of trouble.
renangle |
|
|
|
|
lkazanov2
 Basic Member
 Posts:177
 |
08 Oct 2008 10:28 PM |
|
Guys,
What about quadlock? The system is elegant, allows you to position the ties where needed, and has very strong corner system? What do you all think??
|
|
|
|
|
renangle
 Basic Member
 Posts:302
 |
09 Oct 2008 08:43 AM |
|
lkazanov2,
As a building system ICF can't be beat in my opinion. With regards to who's block is better you will find several different opinions especially here. If a person is looking to build, the smart money is to identify the ICF professionals in your area, discuss your project with them, the block they commend, and research it (them and the block). Service (from the distributer or builder) when buiding with ICF is typicallly very important, do they have bracing, can they help you find an architect/engineer with ICF experience (if needed), how many projects have they done, what do they bring to the table?
If I lived in Rockford, IL and the only distributor/installer/builder around recommend Brand X and could show me they know what they're tallking about, I would probably use them. If I had no support and was going to still build with ICF I personally would use a block system that is as simple as possible to use, thus one that doesn't have to be put together on the job site, as I would be concerned that perhaps I would miss something.
Again, they all work at the end of the day, we could go on forever debating who's best...Amvic, Reward, Logix, Nudura, IntegraSpec, Quadlock, Build Block, Eco Block, Arxx, etc, etc, etc...most people here would recommend talking with a professional in your area, research them and make the best informed opinion possible.
renangle |
|
|
|
|
EMM
 New Member
 Posts:7
 |
09 Oct 2008 10:45 AM |
|
lkazanov2,
Doesn’t matter which ICF system you select. Knock down or pre-assemble. What is very important is for you do your homework & choose the best dealer/rep that will give you the best customer support possible. Class room course simply doesn’t cut it out. You need to be trained on site as every site are different. Anybody without pouring experience should NOT be left pouring a job by themselves no matter which ICF forms used.
Renangle,
If I am not mistaking the pull out test is perform on the fastening strip by inserting anchors (i.e. screws & then pulling them out) & not the overall forms strength. Obviously we are both bias & feel confident with our choice of ICF brand with very similar end result. |
|
|
|
|
Marc&Kem
 New Member
 Posts:50
 |
09 Oct 2008 10:03 PM |
|
Wow, what great info.
I know we tend to drift away from the original question, but this has helped us realize there are more important things to consider than the type of block. For instance, the installer and support and what has me busting at the seams to learn is the best method for vibrating/pouring the wall. Thanks for elaborating on those areas, it has helped us understand why a installer with experience is the key.
Marc and Kemella |
|
|
|
|
Buddy Newberry
 New Member
 Posts:9
 |
10 Oct 2008 11:22 AM |
|
Marc & Kem,
An experienced installer is the KEY!! I applaud you for conducting such extensive ICF research and for asking the right questions. Once you have decided on a ICF wallsystem it is important to decide on the right installer and ask them the right questions as well.
It is important to ask if they are a certified installer of the product, follow that with a call to the Head Office of the ICF and verify their certification, most often it will be on file, however you may have to ask the Distributor of record for verification depending on their system of operations. Next, the installer may be certified, but what projects has he done??? If you are planning on going to the roof trusses with ICF you may not want someone who is only experienced with foundation applications. This is not to say they couldn't do it, and you may want to give an honest hard working person a chance if you believe they could. Many certifications are all encompassing and only some operate on a tiered certification program ex. A= foundations, B= Residential, C= Commercial, D= Commercial/Industrial. It is important to know what type of license they are operating on. If it is all ecompassing find references to projects they have done, if it is a tiered certification the level they have will tell you if they are qualified and capable of constructing your project (references still recommended). As well, customer support and training are paramount in this process as well, and EMM is correct in saying that this type of construction CANNOT be taught in a hotel room or through a seminar, on site training is the only way to go and if your installer is of the right certification he can train you on site as well. I believe in the tiered system simply because there is a certain amount of trust already instilled within the certification that the customer can count on.
In terms of vibration techniques, most often this is up to the installer. Building inspectors will expect to see a vibrator on site during the pour and being used often to ensure proper concrete consolidation and the absence of voids. It is very important that when vibrating you stick your pencil vibrator (generally 1/2" to 1" vibrator) in the conrete cavity and then turn it on and pull it out. Do not stick the vibrator in the wall while it is turned on, this can and will create air pockets in your concrete and negate the purpose of vibration. In pulling the vibrator up out of the concrete the concrete moves in a downward direction and ensures proper compaction. Pushing the vibrator down into the concrete seperates and slightly lifts the concrete which could result in a negative outcome. I vibrate every 5 to 6 feet, pushing the pencil vibrator as deep into the wall as possible, turn it on and pull it out.
Buddy Newberry, |
|
|
|
|
DesignGreen
 New Member
 Posts:9
 |
17 Oct 2008 08:39 PM |
|
I have worked with four out of the five you have mentioned here, but from a design standpoint. I would agree w/Buddy. An experienced installer is the key. An experienced installer can take a "so-so" block and make a good install out of it. They can take a good block and make a superb install. So the installer is key. I have designed several homes and have worked with several installers. There is one in your area (Knoxville) that has consistently provided me good results. I'm sure they would be glad to help or consult with you. |
|
|
|
|
ph3nom3nalICF
 New Member
 Posts:6
 |
07 Nov 2008 11:48 AM |
|
There's always ARXX, Eco-Block & Polysteel as well to consider. Really it's just best to do your research and based on your requirements a suitable fit should easily be found. Each block has its own features. for example: ARXX - exposed strapping for direct attachment of ext and int finishes PolySteel - Tall wall applications for fast set up ECO-Block - Knock Down block for ease of core width expansion Just thought I would throw some other good blocks into the ring. All The Best |
|
|
|
|
Bob
 New Member
 Posts:7
 |
14 Jun 2013 10:25 AM |
|
BuildBlock, Reward, Amvic, Logix, IntegraSpec or Nudura are all good block. Each manufacture has to have a little tweak to be able to say "Their block is the best"! After all by making fine adjustments to their own product is simply marketing and their way to say they are the best. What makes a block good is the ability to be user friendly and do the job. In turn will help speed the building process along without compromising the project's integrity. Good planning is the name of the tune. Thus a block having no right or left, or up or down will make the job go smoother. Additionally there are two schools of thoughts RE: web spacing. In using a 6" concrete cavity's 8" webs are a little easier to use a pencil 1" vibrator. BUT - the flip side is that it is sure nice to have 6" centers for the finish work. On closing, and this does not effect me, it would be really sweet if the manufacture would tell their distributors to give out pricing on a per square foot along with what they believe would be shipping costs to a site. Being upfront with this is the only way to go. Manufactures and distributors guard this as though it is a propriety top secret! One should educate new clients in the over all benefits of ICF's and have pricing up front and center. In the end all would benefit. ICF construction is the way to build. Regards, from a guy with no dog in the fight.
|
|
|
|
|
BrucePolycrete
 Advanced Member
 Posts:524
 |
14 Jun 2013 11:05 AM |
|
There are opinions and then there are facts. There is a lot of junk out there passing itself off as a code compliant ICF. You would be amazed to learn that some companies market "ICFs" that do not comply with ICC. Others whose names you might recognize are so inferior that they barely cross the bar. Read more here http://polycreteusa.blogspot.com/ |
|
|
|
|
Lbear
 Veteran Member
 Posts:2740
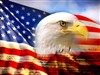
 |
14 Jun 2013 10:40 PM |
|
Posted By BrucePolycrete on 14 Jun 2013 11:05 AM
There are opinions and then there are facts. There is a lot of junk out there passing itself off as a code compliant ICF. You would be amazed to learn that some companies market "ICFs" that do not comply with ICC. Others whose names you might recognize are so inferior that they barely cross the bar. Read more here http://polycreteusa.blogspot.com/
I believe if you stick with the NAME BRAND ICF's, you are safe. The big players like Nudura, Fox, Amvic, Polycrete, etc. The problem is that some states only have a few professional ICF installers. These installers have their own familiar "favorite" ICF block and they stick with that block. When a customer approaches them with an ICF job and asks them to switch blocks, they usually will not or they will charge a higher fee in order to do so. So I pose the question to you: If a customer came up to you and wanted to build a home using a name brand block other than Polycrete, would you agree to it and would you charge a higher fee? |
|
|
|
|
Chris Johnson
 Advanced Member
 Posts:877
 |
15 Jun 2013 08:40 AM |
|
Lbear, to address your question. there are many many many many factors in pricing a project, not just the block itself. Each block has it's own nuances. some require finicky work in one respect and not in another and vice-a-versa on another. Things to consider when reviewing a project, that a lot of people miss, site access. I normally order full trailer loads, so, can a 53' truck fit into the site, if not, where am I staging and how long to move from some shopping center parking lot on a smaller flat bed to the site itself. example, if the truck can get right on site, 45 minutes and we have unloaded the entire truck. if I am shuttling block it has taken 4-5 hours to move it, there is extra costs involved in doing that. Reversible block is worth it's weight in gold...especially with newer guys on site, less head scratching as they stare at a block trying to figure out a left and right corner, laugh as you may, I use to see it all the time. A larger, reversible block does install quicker based how fast it can be moved on the site, or ease of movement/placement in the work area. As you get up higher, smaller blocks require an extra man moving around and passing block up to the man on the scaffold, as opposed to leaning larger blocks against the scaffold and pulling them up as needed. Smaller blocks are easier to handle while cutting (rip cuts) above and below windows. If you are working on regular scaffold say doing a tall wall application, moving the block up to the workers is pretty much the same with a zoom boom and chances are reversibility doesn't mean a lot at that point either. But the number one thing, if you are not using a professional ICF installer, is tech support. ICF has been around long enough that in the big areas where ICF is common it is not an issue, but in some of the smaller areas where it is not common, who is the tech support, where is the stock coming from. If you are doing one foundation, and need 3 more blocks, can you get them? How long? etc. If you have left overs (as you should, never order the exact amount, shit happens, bad cuts, someone stepped on one, etc) can you return it? So before you make the block decision, start with the installer, what is his preference, he will give you a better price for block he is familiar with, now if you are buying the block, ask all the questions, stock, needing more, need to return, etc. Tech Support, everyone has a 1-800 number, big deal, if you are a DIY'er, lets be honest, you need someone to come to site occasionally, not someone answering a phone 1000 miles away trying to solve your issue. FYI, Tech Support can be an installer who is familiar with your ICF, some manufacturers will 'contract' to installers to keep an eye on you. Don't go shopping on price, as the saying goes, you get what you pay for, sometimes you get lucky, but not always the best bang for your buck
|
|
Chris Johnson - Pro ICF<br>North of 49 |
|
|
sailawayrb
 Veteran Member
 Posts:2274
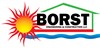
 |
15 Jun 2013 01:21 PM |
|
As others have said, the choice of ICF system largely depends on your local combination of ICF system availability and associated contractor experience that will ensure a successful result. We suspect that block systems will soon become obsolete and will ultimately be replaced by vertical systems. There are already vertical systems available (e.g., TFSystems) that install much faster than block systems and can handle full 12' foot lifts with confidence. Vertical systems also offer other advantages such as ease of creating hydronic heated walls and allow having customized exterior and interior side R-values as required for specific building designs. |
|
Borst Engineering & Construction LLC - Competence, Integrity and Professionalism are integral to all that we do! |
|
|
TexasICF
 Advanced Member
 Posts:622

 |
16 Jun 2013 08:58 AM |
|
Posted By sailawayrb on 15 Jun 2013 01:21 PM
We suspect that block systems will soon become obsolete and will ultimately be replaced by vertical systems.
Do we? This is quite a statement and one that I must comment on. As far as I can tell the vertical systems remain collectively below a few % of the ICF market share. For these systems to be recognized as better they will need to begin capturing tens of millions of square feet of work per year not tens of thousands.
There is a lot of hype around the speed of these systems and their versatility. I will agree that they are much better than conventional construction. However, they have been around for several years and have not gained any significant momentum as far as I can tell. Regards. |
|
|
|
|
Chris Johnson
 Advanced Member
 Posts:877
 |
16 Jun 2013 09:41 AM |
|
And to add to TexasICF statement, vertical ICF systems along with about 40+ odd other ICF systems, they seem to only capture a localized area. Only a handful of ICF are nation wide or even worldwide. |
|
Chris Johnson - Pro ICF<br>North of 49 |
|
|
sailawayrb
 Veteran Member
 Posts:2274
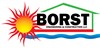
 |
16 Jun 2013 12:44 PM |
|
Right, that's exactly what I stated and precisely my point. ICF product availability and contractor experience with a given product is still very localized and often highly monopolized to the detriment of the consumer. This is one the reasons that the installed cost of ICF construction for an identical building plan in different localities can vary by nearly an order of magnitude. Vertical ICF already dominates the few local markets where it is available, but vertical ICF currently has very limited availability unless you are willing to pay the additional shipping cost which can be as much as the product cost...although this can still end up being lower cost than using some block ICF systems. From our experience, vertical ICF is by far a preferable product with regard to design flexibility and construction cost and, as such, we expect it will ultimately dominate all markets eventually. The only question in our mind is whether this dominance will be accomplished by the few existing vertical ICF companies successfully expanding their territory or by the some of the existing ICF block companies eventually switching to vertical ICF after expiration of patents held by the existing vertical ICF companies. |
|
Borst Engineering & Construction LLC - Competence, Integrity and Professionalism are integral to all that we do! |
|
|
Midsouth ICF
 New Member
 Posts:65
 |
16 Jun 2013 02:27 PM |
|
I would also agree, let the installer decide. they will have their favorite that they can rock and roll with and save you time and money. |
|
Ryan Gunn Owner, Midsouth ICF Builders LLC |
|
|
jperiod
 New Member
 Posts:21
 |
16 Jun 2013 04:32 PM |
|
A disadvantage of installers having favorite ICF block is that it could minimize the options available to a potential customer. For example, if a customer wants higher insulation value (i.e. R30) that are available from some ICF products , if the local installer's favorite does not provide this higher insulation value your may be SOL. Compare this with a stick builder who builds with 2x 4 studs, if the customer wants 2x 6 walls with higher insulation,he just buys 2x 6 instead of 2x4s and its no problem. I think that in order to get higher acceptance the iCF industry needs to have this kind of flexibility. |
|
|
|
|
Midsouth ICF
 New Member
 Posts:65
 |
16 Jun 2013 04:39 PM |
|
How about Fox Blocks? I have used most block and I prefer Fox. I trust it and it is very versatile. However, each installer prefers a certain block and the homeowner will benefit from an installer that trusts and knows his respective block. |
|
Ryan Gunn Owner, Midsouth ICF Builders LLC |
|
|
BrucePolycrete
 Advanced Member
 Posts:524
 |
16 Jun 2013 06:33 PM |
|
If you're thinking about using a vertical product, take a close look at the code compliance. You may be surprised to learn that some vertical "ICF" systems that market most aggressively do not meet the International Code Council's minimum requirements for insulated concrete forms or those of ASTM E-2634. |
|
|
|
|
sailawayrb
 Veteran Member
 Posts:2274
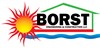
 |
16 Jun 2013 10:15 PM |
|
No, actually I would not be surprised that some vertical ICF systems do not meet ASTM E-2634. I would be more surprised if any vertical ICF systems actually meet ASTM E-2634...along with some block ICF systems that are out there too. As stated in scope section 1.2 of ASTM E-2634, "products covered by the specification consist of molded expanded polystyrene (EPS) insulation panels that are connected by cross ties to form the ICF system." Vertical ICF systems don't use or depend on cross ties to maintain structural integrity during the pour and it would seem to me that ASTM E-2634 would not be applicable to vertical ICF systems. Vertical ICF systems use continuous rails that can often handle full 12' lifts and don't often exhibit the wavy wall issues resulting from horizontally seamed EPS cross tie induced float or settling like block ICF systems have always struggled with. ASTM writes material testing standards and often lags keeping up with new material and product developments. No matter what ICF system is used, we would be much more concerned that it meets the applicable engineering structural design codes for the specific location. |
|
Borst Engineering & Construction LLC - Competence, Integrity and Professionalism are integral to all that we do! |
|
|
Lbear
 Veteran Member
 Posts:2740
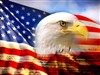
 |
17 Jun 2013 01:35 AM |
|
I don't see block systems becoming obsolete anytime soon by vertical systems. If it did happen, it would be like 10-15 years before they would become mainstream, the big emphasis on "if". As TexasICF mentioned, the current blocks are used in millions of square feet of builds. The vertical systems are very scarce when compared to the standard block system.
I can maybe see the manufacturers testing the market and maybe offering BOTH systems and if they verticals took off, they might switch over but that would be a long time. ICF when compared to residential wood frame is pretty rare. For every 1,000 wood frame homes that go up, how many ICF homes go up? Out here in my neck of the woods I would safely estimate that for every 1,000 wood homes, 10 ICF homes go up. So around 1%. Other states have more ICF builds but out here they are rare.
|
|
|
|
|
BrucePolycrete
 Advanced Member
 Posts:524
 |
17 Jun 2013 06:14 AM |
|
@Sailawayrb, ASTM and ICC-ES define and certify minimum standards for safety and performance. In my opinion, the bar they set is not high enough, but many vertical systems do not meet those minimum standards.There is also the issue of thermal bridging. The "rail" configuration causes a thermal superhighway with heat and cold traveling back and forth freely. Additional measures required to reduce that problem can be costly and time consuming. |
|
|
|
|
smartwall
 Veteran Member
 Posts:1197
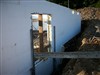
 |
17 Jun 2013 04:06 PM |
|
Bruce, for somone who sells a 32 lb form the make up of which is maybe 2/3 steel, thou should not cast stones. I believe the TF system uses recycled poly in it's rails that can be buried inside as much foam as you would choose to buy. |
|
|
|
|
BrucePolycrete
 Advanced Member
 Posts:524
 |
17 Jun 2013 04:20 PM |
|
Thanks Smartwall, You are correct that the Big Block contains 66% steel by weight and it's recycled steel. It is a VERY strong ICF that will not bulge, scallop or blow out. You continue to make my other points for me as well. You must buy additional foam to solve that thermal bridging problem on the vertical system.Then you have to install it -- or mess around with the EIFS panel. But how do you solve the problem that the system does not meet the minimum ICC requirements? |
|
|
|
|
sailawayrb
 Veteran Member
 Posts:2274
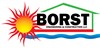
 |
17 Jun 2013 07:15 PM |
|
Lbear, your 10-15 year forecast sounds about right to me...assuming it will be the existing block ICF companies switching to vertical ICF that will actually increase availability and NOT the existing vertical ICF companies successfully expanding their territory. I believe the vertical ICF system design patents were granted in 2011 and design patents expire after 14 years. So the existing block companies should be able to get into the vertical ICF game about 12 years from now or in 2025. I wish that we could wait that long for vertical ICF availability to improve, but the passive solar and hydronic radiant floor integrated building designs that we specialize in greatly benefit from the vertical ICF advantages. Bruce, having recently trained on the TF Systems vertical ICF, I don't see how their thermal bridging could be any worse than block ICF systems? Any thermal bridging effect on thermo performance should be included in the whole wall R-value. The standard TF Systems vertical ICF with 2.5" EPS, 6" core, and 2.5" EPS has a whole wall R-value of 25.17. TF Systems doesn't play games by mixing R-value and thermal mass effects to claim a higher R-value like some companies do. TF Systems even allows you to put as much as 12" of EPS on one side of the core and 0" on the other side (or 12" on both sides) if you so desire. I am not of aware any contractors needing to do remedial work to address a thermo performance with any vertical ICF system. Do you have definitive data/reports that you can share on this? Bruce, I would agree ASTM E-2634 is intended to address product safety. However, the safety issue that is addressed is in regard to the initial form structural integrity to allow safely pouring the walls and NOT the final structural integrity. While initial form structural integrity is certainly something that us contractors need to worry about, us engineers and home buyers should be more concerned about meeting the applicable final structural integrity requirements for the specific building location. The final structural integrity largely depends on the concrete strength/thickness and the rebar schedule (or Helix dose) used. You can remove the EPS forms from all ICF systems after the concrete cures and the final structural integrity is solely governed by the reinforced concrete core and it will be exactly the same with or without the EPS forms in place. ASTM E-2634 doesn't even attempt to address concrete strength and rebar schedule...or meeting the applicable structural requirements for the specific building location such as wind and seismic loads. Bruce, I don't recall that ASTM E-2634 even addresses ICF performance? I am going from recollection here as I am currently on location and I don't have this spec handy, but I thought it only covered basic EPS properties (e.g., density, surface burning characteristics, etc) and quality assurance stuff...and not thermo performance. In any event, we are only talking about EPS and reinforced concrete here. So we really only need to know the correct whole wall R-value and have the knowledge to work out the thermal mass performance to allow us to meet all our design objectives. Smartwell, you are correct that TF Systems uses recycled products. They have been involved with a couple LEED Gold projects. They are also involved with the Pensmore project which is designed to be a tornado-proof 70,000 SF residence using their 12" concrete core vertical ICF and ballistic-proof windows. I also agree with you that a 66% steel block would make a strong ICF form, but would significantly and adversely affect thermo performance too. Sounds "old school" to me and most ICF companies with residential products have learned to use recycled plastic, properly consider thermo performance, and only make the form strong enough to ensure that the pour can be safely and confidently accomplished. As mentioned previously, some TF Systems vertical ICF products can be poured to full 12' lifts with minimal vibration required to achieve proper consolidation. So initial form structural integrity should not be a concern for this product. I have attached photos showing some of the TF Systems product options from when I took their training a couple months ago. We don't have any affiliation with TF Systems (or any other ICF company) and we believe anyone making comments on this forum about various companies or products should also always fully disclose if they have an affiliation with a specific company or product.
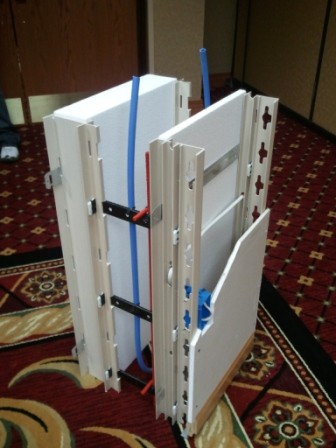 |
|
Borst Engineering & Construction LLC - Competence, Integrity and Professionalism are integral to all that we do! |
|
|
BrucePolycrete
 Advanced Member
 Posts:524
 |
17 Jun 2013 08:43 PM |
|
What is the compressive and flexural strength of their EPS? What is the fire rating on the wall system? What are the result of the fastener withdrawal and shear tests? There aren't any. The system does not meet ICC code.The panels, alone have burn tests and they are approved for exterior perimeter insulation only according to the information the company gave to our client when he inquired. Look up ICC-ESR 1006. Read the NY Times article on Pensmore and pay particular attention to the part where they say building codes and inspections would "complicate" the project. http://www.nytimes.com/2011/07/19/us/19ozarks.html?_r=3&partner=rss&emc=rss&
If I'm wrong, someone send me the test results. Lastly, on the steel in Polycrete, it's in the form of a .16" welded wire mesh that is inside the EPS panel. Rather than "old school" it's the future of commercial grade ICF. |
|
|
|
|
Lbear
 Veteran Member
 Posts:2740
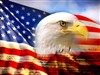
 |
18 Jun 2013 02:41 AM |
|
Posted By sailawayrb on 17 Jun 2013 07:15 PM
I can spot bad hotel carpeting from a mile away. Let me guess, Ramada Inn? I'm in the hotel biz and I've seen my share of hotel carpeting. |
|
|
|
|
arkie6
 Veteran Member
 Posts:1453
 |
18 Jun 2013 07:21 AM |
|
Those TF samples above look like expensive solutions looking for a problem. Radiant tubes in the wall? Why? |
|
|
|
|
Bob
 New Member
 Posts:7
 |
18 Jun 2013 09:11 AM |
|
Lbear said RE above post: "I can spot bad hotel carpeting from a mile away. Let me guess, Ramada Inn? I'm in the hotel biz and I've seen my share of hotel carpeting". MY guess, could be Residence Inn? Whoever took the picture, come clean - what hotel?? I am so glad to see this Forum pick back up since I did a random post on 14 Jun 2013 10:25 AM. Last post above mine was on 07 Nov 2008 11:48 AM from ph3nom3nallICF. Regards from no dog in the fight, RL |
|
|
|
|
sailawayrb
 Veteran Member
 Posts:2274
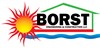
 |
18 Jun 2013 07:57 PM |
|
Lbear, great eye, but this was NOT a Ramada Inn (or a Residence Inn either Bob)...although I would certainly agree those would usually be very safe bets... These photos were from the location at which a TF Systems contractor training session was conducted a couple months ago in Green Bay, WI and at this resort: Tundra Lodge And the carpet installation was the least of issues associated with this building. In fact, this was one of the most poorly designed and constructed buildings that we had seen in quite a while. We actually commented about this and were told that the building had to be rehabilitated a year after opening because of overwhelming guest complaints about room to room noise. I believe they replaced all the original interior walls with QuietRock and moved the original back-to-back electrical outlets to non-adjacent locations. I don't know who the original contractor was on this project, but I would be very surprised if they are still in business. And speaking of construction industry best practices... Only a month after more than an estimated 1,100 Bangladeshi garment workers lost their lives in the collapse of a badly-built and poorly-maintained eight-story building, the new building code has thankfully gone into force. Its rigid practices are already being applied by highly-skilled and properly-trained construction teams laboring in harmony on job-sites all across the sub-continent: New Pile Driver Requirements Implemented Arkie, one of the benefits of vertical ICF is that you can leave one side of the wall open and easily place PEX tube (and rebar too). The most obvious reason for placing PEX tube would be for having hydronic radiant wall heating. This is possible because some of the TF Systems products allow the interior side of the concrete to remain exposed (which is also advantageous for active thermal mass passive solar design applications) while the exterior side of the concrete core can be insulated at whatever thickness of EPS is required for the building design. A less obvious reason for placing PEX tube would be to just slightly heat the EPS sandwiched concrete core to essentially increase the effective wall R-value. As we all know, heat loss through a wall component is proportional to the temperature differential across the component. So when you keep the concrete core at a higher temperature than the outside temperature, you will have less heat loss through the wall. The heat source for accomplishing this is typically from a free renewable resource such as solar heat collection or hydroelectric power. Conversely, the PEX tube can also be used to keep the concrete at a lower temperature than the outside temperature to reduce cooling load. However, one needs to fully understand condensation and dew point or this could become very problematic. Clearly, placing PEX tube in ICF walls is more of an energy efficiency design strategy for long-lived commercial and custom residential projects than for disposable tract homes. There are also few existing design/build companies capable of fully taking advantage of this vertical ICF system benefit. Bruce, I suspect that Mr. Huff's pursuit of happiness relative to acquiring/displaying excessive wealth, shunning government regulations, and lack of empathy to his neighbors as highlighted by this New York Times article has much more to do with his political affiliation/philosophy than with his ICF product selection. Nevertheless, he made his fortune in the software business and is likely very intelligent and busy savvy. So I doubt that Mr. Huff would invest an inferior ICF company and product for his 70,000 SF second residence and his next business venture. Every major code body in North America, including ICC and CCMC, has approved the use of TF Systems vertical ICF products. And as most contractors/engineers know, ICFs are also listed as a prescriptive method of building in the International Residential Code and can be built to commercial design specification using the International Building Code. EPS properties for the six types of available EPS can be found here: EPS Properties All reputable ICF companies purchase their EPS from EPS companies that adhere to ASTM-C578 standards and they typically select either Type II or IX for their ICF designs. Both types of EPS will work well in a given ICF design as long as either the block ICF cross tie system or the vertical ICF rail system has been properly designed to handle the weakest type of EPS that will be used in the final product for the highest allowed concrete pour lift specified. Type II EPS has a density, R-value per inch, compressive strength, and flexural strength of 1.35 PCF, 4.76, 15 PSI and 35 PSI, respectively. Type IX EPS has a density, R-value per inch, compressive strength, and flexural strength of 1.80 PCF, 5.00, 25 PSI and 50 PSI, respectively. TF Systems vertical ICF system products are available in both Type II or IX and in whatever EPS thickness the building design requires. However, I suspect that you already know all this and I get the strong impression that your motivation is more about casting doubt and spewing disparaging remarks about superior products that compete with whatever product you are likely affiliated with and reluctant to provide self-disclosure. |
|
Borst Engineering & Construction LLC - Competence, Integrity and Professionalism are integral to all that we do! |
|
|
BrucePolycrete
 Advanced Member
 Posts:524
 |
19 Jun 2013 09:06 AM |
|
Sailaway, you generate a lot of words but there is little evidence to support them so they just sail away into the clouds. You make disparaging remarks about my veracity without knowing anything about me, yet I am very easy to find. Do you know what ICC requirements for ICF are? Show us the evidence that TF meets ICC minimum requirements for insulated concrete forms and we will happily shut up. |
|
|
|
|
FBBP
 Veteran Member
 Posts:1215
 |
19 Jun 2013 12:21 PM |
|
Posted By sailawayrb on 18 Jun 2013 07:57 PM
And speaking of construction industry best practices... Only a month after more than an estimated 1,100 Bangladeshi garment workers lost their lives in the collapse of a badly-built and poorly-maintained eight-story building, the new building code has thankfully gone into force. Its rigid practices are already being applied by highly-skilled and properly-trained construction teams laboring in harmony on job-sites all across the sub-continent: New Pile Driver Requirements Implemented
Such harmony doesn't always exist on North American sites. Neither does the ingenuity. Please note that the holes are predrilled so the columns are only being place. Neat video anyway! |
|
|
|
|
FBBP
 Veteran Member
 Posts:1215
 |
19 Jun 2013 01:32 PM |
|
I don't think we have to worry about the vertical products taken over the market. There is a reason Lego is, well a block. Childs play. Those of us that entered the industry by way of cip walls with vertical forms are not likely to go back. The closer the height of the block is to the the base the more stable the product. With blocks you can go up to your reach height with virtually no bracing. If you are using a quality block that clips together top to bottom and interlock horizontally, your walls will stay put even in quite windy conditions. I can't imagine handling 8" x 8' foam strips in the wind. I would probably only be able to work 10 day out of the month while I wait for the wind to be below 20 K. While there will be some niche markets where it would be advantageous to place the bar after the wall is up, I can't see how dragging the bar through the uprights would be anywhere as quick as just tucking them in the open top of each layer. There is also an advantage to webs that actually grip the bar and hold it in place. I believe in the control of a pro, any of the main stream blocks can be pour 12' of height at a time. Not to sure why you would want to. Even TF manual appears to suggest 4' lifts. I don't see any reason to increase the the insulation beyond 2.5 plus 2.5". That enclosed mass already exceeds the thermal protection of any other component of the house. The funny thing is that the detractors of the ICF have give the manufactures an excuse to up sell the customers on higher foam levels that aren't needed. Just stay with the standard block and invest any extra coin you have in the other components. In spite of their fancy video I fail to see how TF systems can be faster. You have more component parts to deal with, you need to brace as you go, you need to drag the rebar through the wall. On top of that you need to have a trailer load of extra components to install their transform system. Over time these will get covered with slurry and be difficult to deal with. As it is a localized system, I suspect the the distributor will rent you all these pieces but it does remind me of going back to the job to strip the forms and loading all the forms at the end of the job prior to moving to the next. I believe there will be a place for this type of system but I doubt it will ever be main stream. Wether you have to transport your product 100 miles or 1000 the road cost form a surprisingly small part of the cost. Availability has more to do with the acceptance (or lack the of) of the product itself. The is certainly a case for the the small guys not having the advertising budget to expose their product. maybe that is Mr. Huff's problem. Wether a block is cast in the manufacturers facility or a contract facility makes small difference. The contract facilities do nothing else but blow foam. They are experts at making foam products just like concrete precasters are experts at precast. It doesn't matter what product the precaster are casting. Paying for an increase in pull out strength only makes sense if you are going to hang your kitchen cabinets with one screw. Fully load cabinet would seldom reach more than 60 pounds per lineal foot and most cabinets are hung with between 4 and 8 screws. Doesn't take much when you spread the weight over that many screws. If the product is well received in your area and you can talk to installers and homeowners about it, I would take that to heart more then exactly what codes it happened to be tested to. No installer is going to use a product for the long haul that give him problems. Happy installers are much more important then how some company got past a particular code compliance issue. As has been said, after the pour all concrete is the same regardless of what foam it is inside. If anyone is reading this to actual pick a product, I will say what many of the professional installers have already said. Go with the installers preference and where you get support. Beyond that I would look for a block the actively clips together top to bottom. These block do not drift or float. The webs are solid from top to bottom and have very little stretch or compression to them. If your wall is 8' high prior to the pour it will be 8' high after the pour. Also look for block that fully interlocks horizontally. There should be no need for extensive corner bracing etc.. Big blocks tend to go a bit quicker while smaller blocks have some advantage in complicated projects. Steel conducts heat much quicker than plastic so I would avoid any block that has steel in the foam part of the block. Just my thought on the subject.
|
|
|
|
|
sailawayrb
 Veteran Member
 Posts:2274
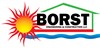
 |
19 Jun 2013 09:01 PM |
|
FBBP, glad you enjoyed the lighthearted video. I largely agree with all your thoughts on this subject. If we didn't do aggressive passive solar designs, we would continue to be perfectly happy with Logix. I now see while Mr. Polycrete asks many questions, he hardly ever answers any asked of him including yours and mine. However, from your response on page 2 of this thread, I now also know the "rest of this story". I guess I should have figured this out much earlier, but I really don't have time to stay current with no-name products. I also share your concern about wind and actually posted my thoughts about this on the forum previously: More perspective on TF Systems The above link also contains some additional perspective, photos, and takeoffs/prices on TF Systems vertical ICF products for those interested. Time will certainly determine how well vertical ICF performs in the market and it will be interesting to revisit this in the coming years. BTW, my wife said to convey thanks to the person who pointed her to the hypertufa pot mix, whom I believe was you. We now have some very nice pots awaiting soil and plants. |
|
Borst Engineering & Construction LLC - Competence, Integrity and Professionalism are integral to all that we do! |
|
|
BrucePolycrete
 Advanced Member
 Posts:524
 |
19 Jun 2013 11:55 PM |
|
Sailaway, the, words you generate are certainly breathtaking for their sheer volume. Those who prefer quantity over quality are doubtless impressed. Some think it’s fun to ramble in several directions at once. I’m a simple man, though and find brevity and directness more appealing. If I missed answering any of your questions, I apologize, but I was unable to find them in the sea of your loquaciousness. In order to free up some space in my inbox, I am going to turn off the notifications for this thread now. So if you ever come across any of those ICC test results or code approvals for TF, drop me a message and I’ll gladly sign back on for the public Mea Culpas. By the way, Polycrete’s been used to build energy efficient commercial structures that stand up to Mother Nature in sixteen countries on five continents since 1988. We have dedicated Polycrete factories in North America, Asia and Europe. Have a great summer!
|
|
|
|
|
Roger R
 Basic Member
 Posts:131
 |
05 Jul 2013 04:16 PM |
|
I'm a newbie at all this, as I am in the final throws of our design stage for an ICF addition to a CMU beach house. I've been looking at a few different ICF systems, including TF. Frankly, I tend to agree with Bruce's comment about the possibility of a constant thermal bridge, with the TF System. I like the way the TF panels slip into their forms, as my 'old timer' concrete guy can build his "rebar cage" and feel confident; and cleaning any forgotten debris or dropped items from the bottom of the cavity is easy - BUT all that metal - outside, through the concrete and into the inside of the house looks like a problem to me. Constructing all that TF metal seems like a nightmare too. Lego is popular because it is easy. Additionally, when I read that article on ICFMAG about the owners of the Pensmore house choosing that location because there are no building codes down there (How can that be - this isn't China!?), a BIG red flag went up for me. Maybe TF is still experimenting with their system, and maybe the Pensmore guy is buying into the factory, I don't know - but as a consumer, I'd like a 'tried & true' system. I'm not a guinea pig and I'm not a pioneer. Adding all that together turned me off, and turned my engineer off to the TF System. TF is possibly a good start to something that will be good in the future, but for right now, I have to pass on it. Polycrete, Quad-Lock and ARXX are in our final choice list, Quad-Lock being the easiest for me to get. If Polycrete had good West Coast distribution, I'd jump on it in a minute but Quad-Lock is 100 miles from my job.
I started a new thread/topic, to discuss the pro's & con's of Quad-Lock, and would enjoy reading feedback if you are familiar with Quad-Lock. |
|
|
|
|
Active Forums 4.1
|