bpwrightwv
 New Member
 Posts:35
 |
26 Feb 2007 01:48 PM |
|
I'm curious if the contractors regulary test the soil to see if it can handle the weight of ICFs?
How about those of you building in sandier soil settings, like FL and coastal regions?
|
|
|
|
|
|
Cattail Bill
 Basic Member
 Posts:206
 |
26 Feb 2007 08:10 PM |
|
I live in Minnesota land of ten thousand lakes with sandy beaches, we also have the other extreme clay so heavy that the full swing hoe will almost tip over trying to dig it out. But we also have the frost push up here and that can be very severe so to say the least we always put in the max amount of rebar and we get to sleep at night. Rebar is still relatively inexpensive in the grand scheme of your construction project. Remember build cheap and you have cheap, build expensive and you have expensive but not nesassarily any better than cheap, build right and you have the best of all worlds. |
|
|
|
|
icfcontractor
 Basic Member
 Posts:277
 |
26 Feb 2007 09:01 PM |
|
BP,
In the Seattle area most Designers, Architects, and Engineers are specing a footing to placed on the least common denominator soil which is a 1500 PSF soil or sandy soil. If you are building a single home, it typically does not pay to have a soils engineer to test your soil so you can adjust your footing size to the weight carrying capacity of the soil you are building on. In the case of a development or large structure, it may be cost effective to have a goetech test your site to help reduce the size of your footing. Anyway typically around here people default to 1500 Pounds per Square Foot soil which is sand. Hope this helps.
ICF Contractor |
|
|
|
|
fjohnson
 New Member
 Posts:30
 |
27 Feb 2007 10:20 AM |
|
Here, most contractors that build residential know the type of sub-soils and just build accordingly. The sub-soils here are almost all the same except for near rivers. When we built we bought a soil penetrometer to test the base, and then called an engineering company and asked them to send someone experienced in the field, who could look at our soil type and verify for us what we had already determined. This eased my wife's concerns and saved us the cost of doing a lot soil boring. |
|
|
|
|
PanelCrafters
 Advanced Member
 Posts:680
 |
27 Feb 2007 04:34 PM |
|
Posted By bpwrightwv on 02/26/2007 1:48 PM I'm curious if the contractors regulary test the soil to see if it can handle the weight of ICFs?
How about those of you building in sandier soil settings, like FL and coastal regions? In my area of Colorado all foundations must be engineered. So, it's up the the engineer whether to test or not. To CTA, I'm guessing that most do. |
|
....jc<br>If you're not building with OSB SIPS(or ICF's), why are you building? |
|
|
jredburn
 New Member
 Posts:51
 |
27 Feb 2007 07:59 PM |
|
bp We build ICF four story houses on the beach here in Florida and they all need piling to support the weight. So an Engineer has to do his thing on them. About a year ago a major developer dredged a hole in the ground and used the stuff for fill under the houses on his project. The Engineer told him not to do that but he went ahead and did it anyway. The houses settled and cracked, the County came in and told him to tear down 27 of them and replace the fill. Now the County requires EVERY lot to be soil tested by an Engineer. If you have an Engineer test the soil and the house settles, he is liable. If you dont have it tested and the house settles guess who pays. Regards, Joe |
|
|
|
|
Mark Fleming
 Basic Member
 Posts:112
 |
08 Mar 2007 09:39 PM |
|
The International Residential Code contains some generic information on soil types, bearing allowances, and concrete wall heights and building heights. If you meet the tables, then you don't need engineering. The issue might be whether you have "poorly graded sand and gravel" or "poorly graded gravel and sand." Better to meet the table for the weaker soil condition and then add two inches deeper, four inches wider, and an extra rebar. Costs an additional $250. Or, pay a geotech $1,500 and then add two inches deeper, four inches wider, and an extra bar.
Mark Fleming |
|
|
|
|
eric monkman
 Basic Member
 Posts:262
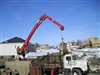
 |
10 Mar 2007 03:24 PM |
|
We always use a local Geotech. They know the history and peculiarity's of their stomping grounds.
From the report, we hire a consulting P Eng to design footings based on all loads. We have to provide full drawings and roof system loads for this. Lintel re-inforcing is also reviewed at this time.
This little extra step lets me sleep really well at nite, and has probably saved us many $$. We have gone to 4 in core on several jobs and the fees have been won back many times over with economical Engineering design, as well.
The best part, really, is the BO relax's with you, cause you've got their behind covered. They like that. |
|
|
|
|