albanygreen
 New Member
 Posts:3
 |
03 May 2010 07:14 PM |
|
I am planning to build a new 4000+ sq ft house in upstate NY (specifically, in Albany, NY) and have been thinking of using ICF. I am aware of all the benefits of ICF but I am a little concerned about the appropriateness of ICF for a place like upstate NY. I might be wrong but there doesn't seem to be that many houses in this area that have used ICF. Is there something about the winter, snow, etc. that might reduce the effectiveness of ICF? Also, are concrete roofs appropriate here? Any guidance on this would be most welcome.
|
|
|
|
|
|
dmaceld
 Veteran Member
 Posts:1465
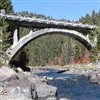
 |
03 May 2010 08:11 PM |
|
Posted By albanygreen on 03 May 2010 07:14 PM
there doesn't seem to be that many houses in this area that have used ICF.
Except for certain localities that's pretty much the situation all over the country. ICF still isn't a widely adopted construction method. Do a search in these forums for "thermal mass" and you'll turn up lots of sometimes heated discussions of the pros and cons of using ICF in northern climes. ICF by its nature does not lend itself to cheap construction like wood frame can. That's one reason it's not more popular. Search for "cost" and "construction" and you'll come up with a lot of discussion about ICF costs vs. other methods. What you will find is that compared to cheap construction ICF loses, but compared to quality construction which is energy efficient ICF is competitive, especially when non-energy factors such as strength of the shell, fire resistance, etc. are factored in. I see this is your first post. What you will find very quickly by reading these forums is there are no simple answers to your questions. You are embarking on a challenging, time consuming, and rewarding project to learn what you need to know to make your own decisions with which you will be comfortable. Happy hunting! Is ICF appropriate for upstate NY? I will say the answer lies somewhere between probably and absolutely yes! |
|
Even a retired engineer can build a house successfully w/ GBT help! |
|
|
TexasICF
 Advanced Member
 Posts:622

 |
03 May 2010 08:32 PM |
|
I would skip the probably and go straight to absolutely. If one thinks they can do better I like to be enlightened. See Oakridge labs report (particularly regarding Minnesota - i don't recall if New York is mentioned specifically or not). Read it very carefully -- in order for a low mass system to perform (about 10% poorer) it must be built to the same R-value - which is not that easy to accomplish.
Folks often misquote this report to say that ICF only provides 10% improvement over conventional. Try building your home out of 2x8 studs and foam and see how your costs compare. Remember that typical wood performs to about an r1 per inch so even with 2x8s roughly 15-20% of your stucture is performing at a very low r-value - thus - even with a huge rvalue between the studs (e.g. closed cell foam) the only way you can get there is to stagger your studs so they are not connecting inside and out. etc.
That said dmaceld is right --- read up on this. Good luck though lots of @##x and misinformation to wade through. Regards. |
|
|
|
|
smartwall
 Veteran Member
 Posts:1197
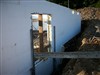
 |
04 May 2010 07:27 AM |
|
You are correct about the dirth of total icf homes in upstate. This is a foundation market primarily. I can give you the name of a customer in Clifton Park who built a unique Italian villa with icf's, I think the square footage was about 5.000 with a 3 car garage and a finished basement with 10' ceilings. |
|
|
|
|
albanygreen
 New Member
 Posts:3
 |
04 May 2010 02:27 PM |
|
I would much appreciate the lead to the Clifton Park house which used icf. Thanks.
|
|
|
|
|
smartwall
 Veteran Member
 Posts:1197
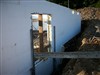
 |
04 May 2010 06:53 PM |
|
I'll send you a PM after I call the customer, I don't think it would be a problem. |
|
|
|
|
TF System
 New Member
 Posts:4
 |
04 May 2010 09:14 PM |
|
Absolutely ICF is OK to build with in Upstate NY. We have two projects in upstate right now and we have sent several to NY this spring. Todd |
|
|
|
|
mugzy
 New Member
 Posts:4
 |
04 May 2010 10:40 PM |
|
Albany uses a lot of Precast Superior Walls in residential work as well. |
|
<a href="http://www.todaysconcretetechnology.com/community">Concrete Discussion</a> |
|
|
albanygreen
 New Member
 Posts:3
 |
05 May 2010 07:26 AM |
|
Todd, it will be great if you could let me know where those two projects in upstate are ... Thanks. In the past few days I have become aware of some projects in this area and I am trying to touch base with the builders to see what brands they use, their experience, etc.
|
|
|
|
|
miformguy
 New Member
 Posts:43
 |
05 May 2010 07:49 AM |
|
We recently completed a hotel several miles north of you. We started late fall and finished this spring. One of the owners lives in an ICF home which was a driving force in the decision to use ICF on their hotel and restaurant project. |
|
|
|
|
BrucePolycrete
 Advanced Member
 Posts:524
 |
05 May 2010 09:43 AM |
|
New York State is currently a very active area for ICF construction. We have commercial projects in the bidding process now and completed an addition to the Performing Arts Center in Rhinebeck this past fall. |
|
|
|
|
jamesmacdonald1
 New Member
 Posts:95
 |
05 May 2010 10:24 AM |
|
There are few projects I was involved with in upstate NY using Durisol if you are interested. |
|
|
|
|
ausableriver
 New Member
 Posts:2
 |
10 May 2010 11:26 AM |
|
I'm looking to build a 1500 square foot home in Keene NY out of Durisol. I would love to hear of your experiences with the product both in terms of construction and how the product works in real life. The home design has 178 linear feet of exterior wall. I'm an owner/builder for the project. Thanks |
|
|
|
|
BrucePolycrete
 Advanced Member
 Posts:524
 |
10 May 2010 11:44 AM |
|
I'm interested in learning what caused you to choose that particular product. |
|
|
|
|
jamesmacdonald1
 New Member
 Posts:95
 |
19 May 2010 10:36 AM |
|
We chose it because we feel it had benefits over traditional ICF systems. Not that there is anything wrong with either type (I don't want angry EPS form guys yelling at me). My comments below contain a lot of qualifications because I know without it, the polystyrene proponents will be all over me. Here is our conclusion of benefits vs detriments for Durisol: 1.No polystyrene or other petroleum based products. I won't get into VOC or offgassing issues because the polystyrene industry indicates that this is not an issue, but the overall environmental impact of the material is less (that is all I am talking about is the material, and not the long term benefits of polystyrene that might mitigate the manufacturing of polystyrene, etc). Durisol is comprised of simple ingredients; cement and wood aggregate. The mineralization process is purely subtractive which means that nothing is added to the wood and only the sugars are removed to render it inert and allow for cement hydration. In actuality, by using the waste wood, there is considerable Carbon being sequestered in the product that would otherwise either be burned (fast carbon release) or slowly rot/decay (slow carbon release). 2. Energy input for Durisol is less (manufacturing does not require temperature/high pressure). Extra cement in the forms is offset by less cement in the volume of concrete required. 3. 100% recycled wood content. They only use recycled waste wood (100% clean, natural softwood lumber) that is taken from sources such as truss manufacturing operations, and otherwise being sent to landfill sites or burned. 4. Durisol does not burn or melt. Fire rating are same for all ICF products, but zero flame spread, smoke spread of 11 and no black smoke or fumes created in the event of a fire are desirable 5. Durisol is more energy efficient. I know there is differing opinion on this, but ultimately, from a building science perspective, most experts seem to agree that the goal is to have the insulation continuous on the exterior of structure (for both heating and cooling climates). There are no thermal bridges through the Durisol webs (R1.75 per inch x 12" thickness) and with the insulation placed primarily on the exterior of the concrete mass, it was a more desirable configuration for us. 6. Durisol facilitates improved healthy / indoor air quality. The Durisol material is a hygroscopic material - which means that it has a very large capacity to store and release moisture as required, depending on the environmental conditions. This storage capacity refers to storing moisture in the form of water vapour and increased material moisture content – not liquid water. Also, the Durisol material and wall system is extremely vapor permeable. It does not act as a vapor barrier, but acts as a vapor regulator and keeps indoor RH (Relative Humidity) levels at a healthy and comfortable level. They have proven that Durisol does not allow condensation within the wall cavity when used without a vapor barrier, and maintains RH levels below RH 65-70 naturally. They have been approved for use without a vapour barrier. The traditional ICF has a built-in vapour barrier so it doesn't need another one, but in the case of Durisol, it doesn't have one and doesn't need one. In our projects, mold mitigation was also important. We wanted to do this in a more natural way instead of mechanical means (I am not suggesting one is better than the other, but it was a choice). Firstly, because the material is hygroscopic and vapor permeable, RH levels are kept low enough such that it is not possible to reach the level of RH where mold can start to grow (typically 75% RH +). Combined with the high pH (alkaline) environment resulting from the cement content, this means that the wall system actually helps to inhibit mold growth on the interior. Again I am not saying traditional ICFs promote mold growth, but just providing some of our thought process. 7. From my interactions with various health consultants, and doing some research on the health policies in various European countries, there is some potential health concern with EPS. While there is less concern about the health effects of EPS itself, the brominated fire retardants used in most EPS foam (decaBDE or hexabromocyclododecane are the most commonly used) generate health and environmental risks that are generating even more significant concern. The EPS proponents will advocate that as long as these fire retardants are kept isolated and do not leech into the air or get disturbed, there is no risk. I personally find it like arguing for asbestos which is ok as long as it isn't disturbed. You can find a lot of information from the EPA and other credible health organizations if you look for it. Again, i am not try to be a fear monger, but if there is information coming out slowly, it is worth being aware of it. Apparently in the 90's there were a dozen or so permitted fire retardants in the US and as the EPA investigated each one separately, they were banned one by one. There are only a few left as approved, but the EPA has not looked at the research on them in depth. It is not fair to just ban all chemical configurations of fire retardants based on studies of one specific type, so they apparently investigate one configuration, find some issues, ban them, and then look at the next one. I think that is why it is taking so long to get through the list of all the different fire retardants that are available for use. Anyway, you should do your own research on this topic and decide whether it is real or liberal propaganda. 8. Durisol is more impact resistant. Both stucco and drywall, when attached to Durisol result in a solid, durable, impact resistant finish. 9. Durisol is more resistant to termites. They have completed a 7 year termite study with US Forest Service and found no damage to the Durisol material over this period of time. Although Styrofoam does not provide a food source to termites, it does provide a protected high humidity environment that can also serve as a pathway for termites. Because of the cement around the wood fibers, they can't eat it. Also since there is a random matrix of material, although the Durisol is porous, there is no real path to follow. And again, the alkalinity of the material is a deterrent as well. 10. Both types of ICF are arguably equally strong and resistant to blowouts (Durisol says they are stronger and others say they are, etc.) 11. Both types of ICF arguably require the same amount of bracing (same as above). 12. It is possible to drywall or attach screws to any point on the finished surface, not just at the discrete plastic web locations of traditional ICFs 13. Durisol costs more 14. The blocks are heavier. 15. Need an air/weather barrier on the exterior of the Durisol (same as conventional contstruction) |
|
|
|
|
jamesmacdonald1
 New Member
 Posts:95
 |
19 May 2010 10:45 AM |
|
To ausablriver: From a performance perspective, I like the Durisol very much. I have been in both types of ICF homes and there is a difference in how they "feel". They energy efficiencies are great (as they would be with any ICF system). You can tell that there is something more solid behind the finishes, but that is just a feeling. Humidity control is very noticeable (even with non vapour permeable finishes). Overall the feeling difference might be a bias, by then again I guess everyone has a bias. From a construction perspective, the only real issue is the weight of the blocks. Although they weigh the same as a CMU unit and are much larger, Durisol units are smaller than the polystyrene units which are ridiculously light. But then again, building a house is supposed to be some work right? |
|
|
|
|
Rsipgeo
 Basic Member
 Posts:104
 |
20 May 2010 11:55 PM |
|
I wonder what kind of response you would get if you asked if SIPs were appropriate for an Albany home in the SIPs forum. Oddly, I am working on a project near Albany where I am stick building, using ICFs and using SIPs. My answer is that it depends what you are looking for that determines your building envelope. |
|
|
|
|
tomh
 New Member
 Posts:9
 |
20 Jun 2010 11:24 AM |
|
We just built an ICF home outside Rochester. I'm not sure if I would do it again. Nothing against the product at all, but the problem we had was finding contractors experienced with the product. If we lived in the Southwest or Florida, where they are prevalent, we wouldn't hesitate to go ICF again.
We only found three GCs that had worked with it. Only one had any extensive experience with ICFs and he disappeared half way through the selection process. The other builder had done one ICF house and the builder we went with had done 5 basements. Somehow he received nothing but glowing reviews.
We have been in the house two months now and are having water issues in the basement (see my post "Water issues on new Arxx build - please help" http://www.greenbuildingtalk.com/Forums/tabid/53/aff/4/aft/77261/afv/topic/Default.aspx).
If you are going to do it, you need to do as much research as possible. I did a ton, but I now wish I had obtained the installation instructions for each product prior to them being installed. You also need to be around a lot! Of course I would probably recommend that for any build regardless of materials.
Hope this helps.
Tom
|
|
|
|
|
khinsdale
 New Member
 Posts:2
 |
01 Jul 2010 10:36 PM |
|
This is a very good question albanygreen as it is one that I had as well. My wife and I are looking at building a new home in Western NY (about an hour and a half south of Buffalo) and someone made reference to the fact we should look at a ICF foundation. My one of many concerns (only because it is rather new) relating to this product is how it would hold up to the western NY winters. I am also concerned about the fact there are very few homes (if any) in this area that have ICF and in turn not aware of any contractors that have a track record of using it. Any western NYers out there who have put in ICF or know of anyone that did that could supply a reference? Early research on this product has me very excited as traditional block basement is old school and superior walls concern me due to the fact they do not sit on a footer. Any assistance out there would be much appreciated. |
|
|
|
|
Raider Bill
 New Member
 Posts:75
 |
21 Jul 2010 05:58 PM |
|
Watched a guy build in Rome NY which I know to be a lot colder that Albany and more snow that Buffalo. He's VERY happy with it. |
|
|
|
|