Lbear
 Veteran Member
 Posts:2740
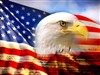
 |
28 Nov 2011 01:33 AM |
|
A very good study and read about voids in ICF walls. The conclusion is that voids WILL occur in all ICF applications. It is a 100% guaranteed fact. This leaves one to decide on HOW to eliminate or reduce these voids. ICF Void StudyThe study states: "In a properly designed concrete mix, it is virtually impossible to “over vibrate” the concrete leading to segregation. However, with increased vibration, the possibility of blowouts increases."The 3 external mechanical vibration techniques (hammer, orbital sander, and reciprocating saw) ALL FAILED to properly eliminate voids. They all allowed "significant" voids in the ICF walls. Internal vibration using a pencil vibrator held the most promise for eliminating voids. Ideally the use of a slump of 150 mm (6 in.) or greater can be used to produce ICF walls free of voids, especially if internal vibration is utilized. Contractors that utilize more water to get better slump are actually harming the strength of an ICF wall. For each 0.1 increase in the water-to-cement ratio, they can drop the psi strength by almost 1,000. So a 3,000 psi mix with extra added water will drop down to 2,000 psi. |
|
|
|
|
|
BrucePolycrete
 Advanced Member
 Posts:524
 |
28 Nov 2011 01:10 PM |
|
Great report from several years ago, but it's always a good topic to bring up... debunking myths about vibrating ICF walls. Bottom line on this report is that standard internal vibration, self-consolidating concrete or use of super-plasticizers are the only ways to avoid dangerous voids in ICF walls.It's also important to note that placing concrete beside the corner and hoping it flows down in is also a recipe for failure. The report showed that proper use of the vibrator is critical. That means a small vibrator with a 3" sphere of influence has to be inserted every 2" inches in order to get the job done. Or use a larger head with a larger area of influence. The challenge here is that all of these methods of preventing voids also increase the chance of blow-outs. This is not news to Polycrete. It's why they developed the Big Block. Steel reinforcement inside the EPS panel prevents blow outs even when pouring 8 feet or more per hour. Slim 4mm steel wire cross ties do not impede the flow of concrete like cumbersome conventional plastic ones do. Polycrete's unique corner guide/support are strong enough to allow you to place concrete directly into the corner. Polycrete couldn't have asked for a more favorable report if they had commissioned the study themselves. |
|
|
|
|
smartwall
 Veteran Member
 Posts:1197
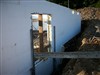
 |
28 Nov 2011 04:09 PM |
|
This isn't really new news. The PCA 2003 report says proper mix and a proper sized vibrator will overcome voids. Many forms on the market can take a 8 slump or better when you use a water reducer to increase slump. The important part of the report found that increasing the slump up to SCC range didn't dramatically increase the pressure on the form. Find a good form and a proper mix and you will be ok. |
|
|
|
|
BrucePolycrete
 Advanced Member
 Posts:524
 |
28 Nov 2011 04:30 PM |
|
Unfortunately, they only had pressure testers on the 4" wall, and it was extruded polystyrene, not expanded, so the test didn't really reflect more common real world conditions. Pressure testing on an 8" EPS wall with 8' of concrete and an 8" slump would have been more interesting. |
|
|
|
|
Lbear
 Veteran Member
 Posts:2740
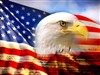
 |
28 Nov 2011 07:37 PM |
|
Posted By BrucePolycrete on 28 Nov 2011 01:10 PM
The challenge here is that all of these methods of preventing voids also increase the chance of blow-outs. This is not news to Polycrete. It's why they developed the Big Block. Steel reinforcement inside the EPS panel prevents blow outs even when pouring 8 feet or more per hour. Slim 4mm steel wire cross ties do not impede the flow of concrete like cumbersome conventional plastic ones do. Polycrete's unique corner guide/support are strong enough to allow you to place concrete directly into the corner. Polycrete couldn't have asked for a more favorable report if they had commissioned the study themselves.
How does one install screws into the steel cross ties? When you are hanging drywall, you can run a screw into the plastic cross ties but if the tie is metal, how do you install anything to it? Do contractors use internal vibration machines when using ICF like QuadLock? Wouldn't the machine cause the plastic ties to break? |
|
|
|
|
BrucePolycrete
 Advanced Member
 Posts:524
 |
28 Nov 2011 10:16 PM |
|
Lbear, First of all, Polycrete's steel cross ties are 4mm steel wire -- you don't screw anything into them. What you DO screw into is the 1-1/2" X 22 gauge steel fastening strip, which runs horizontally on 12" centers. That means no vertical studs to line up when stacking the blocks, so less waste. And you use self-tapping screws. Polycrete Big Block is most commonly used in commercial construction, where studs are typically steel anyway. If you're thinking about Polycrete Big Block, it's such a radical innovation on ICF technology that you should just forget everything you already know about ICFs -- most of it does not apply. On your other question: Yes, good contractors use internal vibration on ICF walls like QuadLock. But they have to be very careful, as the vibrator can most certainly break the plastic ties and cause the forms to blow out. |
|
|
|
|
robinnc
 Advanced Member
 Posts:586
 |
28 Nov 2011 10:21 PM |
|
I think what he was saying that their blocks have the wire on the 'inside' of their block but the webs are on the outside like reg. ICF blocks to hang stuff.
|
|
|
|
|
BrucePolycrete
 Advanced Member
 Posts:524
 |
28 Nov 2011 11:56 PM |
|
Sorry I can't figure out how to post pictures on here, but have a look at polycreteusa.com for details. |
|
|
|
|
BrucePolycrete
 Advanced Member
 Posts:524
 |
28 Nov 2011 11:56 PM |
|
Oops, double post. God, Giants suck tonight. |
|
|
|
|
smartwall
 Veteran Member
 Posts:1197
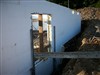
 |
29 Nov 2011 08:32 AM |
|
Fox Blocks had their icf tested in Canada and it was the only 8" on center web block to pass the internal pressure test. |
|
|
|
|
BrucePolycrete
 Advanced Member
 Posts:524
 |
29 Nov 2011 09:02 AM |
|
Not sure where Smartwall got that information on Fox Blocks, but Polycrete Big Block has steel ties on 8" centers and test results on a 10" thick Polycrete wall showed ZERO deformation and only 3mm out of alignment over the entire wall surface. Better yet, that was an 8' wall consisting of two 4' lifts poured within 15 minutes and vibrated internally with a mechanical vibrator. Message me offline and I will send anyone the entire report. By the way, that's a test that all ICFs used in Canada must pass. |
|
|
|
|
TexasICF
 Advanced Member
 Posts:622

 |
29 Nov 2011 10:37 AM |
|
Be careful what you claim here smartwall. You should be made aware that there are TWO different testing methods utilized in Canada to COMPLY WITH CCMC Evaluation Requirements for “Form Capacity” Testing. Questions have been raised throughout the ICF Industry regarding the legitimacy of test method “Option A” as to its applicability to ICF Form Systems and questions have been raised as to whether the test is truly repeatedly from one lab to another. My understanding is that Foxblock’s system was tested at a different laboratory than many others to this Option A method. Further, if you go to the CCMC Website, you will see that MANY of Foxblock’s competitors have successfully obtained CCMC COMPLIANCE by conducting testing to the Option B Test method which more accurately represents actual concrete pressure than the artificial pressure plate option (A) test can replicate. Therefore, your claim is inaccurate and mis-leading to the Industry as a whole. Just for food for thought.., I've taken the liberty of posting pictures of successful forty foot (two pours) and thirty five foot (two pours). I have many tall wall pours to post if that would be of value. Regards.+   |
|
|
|
|
Jerry D. Coombs, PE
 Basic Member
 Posts:138
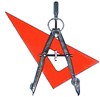
 |
29 Nov 2011 11:33 AM |
|
True, there's not a lot in there that is news, but it sure helps when trying to explain to building officials that a little honeycomb (or voids) isn't always a bad thing. How much void space is there in a stick-frame wall? CMU? Yeah, we have to watch it more closely in below grade applications. As far as pressure and its blowout tendancies, from what I can tell, there are so many variables that it's hard to quantify, and the skill/ experience of the installers has most to do with getting it in well and without voids. |
|
Jerry D. Coombs, P.E.<br>Coombs Engineering, P.C.<br>
<br>You can have with quality; You can have it fast; You can have it cheap. Pick any two. |
|
|
Lbear
 Veteran Member
 Posts:2740
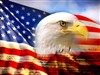
 |
29 Nov 2011 01:30 PM |
|
Posted By BrucePolycrete on 29 Nov 2011 09:02 AM
Not sure where Smartwall got that information on Fox Blocks, but Polycrete Big Block has steel ties on 8" centers and test results on a 10" thick Polycrete wall showed ZERO deformation and only 3mm out of alignment over the entire wall surface. Better yet, that was an 8' wall consisting of two 4' lifts poured within 15 minutes and vibrated internally with a mechanical vibrator. Message me offline and I will send anyone the entire report. By the way, that's a test that all ICFs used in Canada must pass.
For a 2-story residential home, is Polycrete "overkill"? It seems to be more of a commercial application. I was looking to do a 6" pour for the home. I assume that with Polycrete you still insert re-bar every 16" OC, correct? |
|
|
|
|
jeepster
 Basic Member
 Posts:153
 |
29 Nov 2011 11:38 PM |
|
It's amazing how this topic brings up varied responses between builders. According to our local pump truck operated, builders around here swear to NOT use a vibrator during the pour. Just pound on the walls. These builders also order the concrete at about a 6 slump and then possibly add water on site. I, on the other hand, wasn't that keen on the idea. Voids are one thing, but simply getting the air out and consolidating around the rebar to make sure you have a good bond is also very important. I don't think just pounding on the icfs will do anything to help that. The last wall I poured was 9' tall. I did it in three lifts. I fabricated my own "rebar shaker" using an angle grinder. The device threads onto the grinder's arbor and I machined a snout that would fit over the #5 rebar. That snout is off-center, so it shakes the rebar at about 13,000 rpm, which is about the same speed as a typical concrete vibrator. Since I had vertical rebar every 16", I placed the snout over each piece of rebar and hit the grinder switch. It worked surprisingly well. I also had a concrete vibrator on hand and the rebar shaker actually did a better job of moving the concrete around. When I'd pour along a window opening, I'd just hit the closest vertical rebar with the angle grinder and the concrete would just flow into the opening. Here was the limitation. After the first pour, the bottom of the rebar was stiff enough to the point where the rebar didn't shake so much and I don't think it was very effective at all. Long and short -- it work great during the first lift, but not for the others. A few weeks ago I poured two retaining walls that tapered from 8' down to about 3' along a 24' span. I ordered the concrete at a 3.5 slump, 6 bag mix. I made the retaining walls out of scrap pieces of 8" thick ICF. I vibrated the crap out of those walls. I basically used the vibrater to pull the concrete down the wall from where the truck was able to shoot it in. I didn't get a single bow or buckle. I wanted the low slump, because I didn't want the concrete to push out at the bottom while I was filling it at the top. I'm a big fan of internal vibration. I think where many get into trouble is they pour it too high of a slump and too high of a lift. |
|
|
|
|
TexasICF
 Advanced Member
 Posts:622

 |
30 Nov 2011 07:19 AM |
|
Posted By jeepster on 29 Nov 2011 11:38 PM It's amazing how this topic brings up varied responses between builders. According to our local pump truck operated, builders around here swear to NOT use a vibrator during the pour. Just pound on the walls. These builders also order the concrete at about a 6 slump and then possibly add water on site. I, on the other hand, wasn't that keen on the idea. Voids are one thing, but simply getting the air out and consolidating around the rebar to make sure you have a good bond is also very important. I don't think just pounding on the icfs will do anything to help that.
The last wall I poured was 9' tall. I did it in three lifts. I fabricated my own "rebar shaker" using an angle grinder. The device threads onto the grinder's arbor and I machined a snout that would fit over the #5 rebar. That snout is off-center, so it shakes the rebar at about 13,000 rpm, which is about the same speed as a typical concrete vibrator. Since I had vertical rebar every 16", I placed the snout over each piece of rebar and hit the grinder switch. It worked surprisingly well. I also had a concrete vibrator on hand and the rebar shaker actually did a better job of moving the concrete around. When I'd pour along a window opening, I'd just hit the closest vertical rebar with the angle grinder and the concrete would just flow into the opening.
Here was the limitation. After the first pour, the bottom of the rebar was stiff enough to the point where the rebar didn't shake so much and I don't think it was very effective at all. Long and short -- it work great during the first lift, but not for the others.
A few weeks ago I poured two retaining walls that tapered from 8' down to about 3' along a 24' span. I ordered the concrete at a 3.5 slump, 6 bag mix. I made the retaining walls out of scrap pieces of 8" thick ICF. I vibrated the crap out of those walls. I basically used the vibrater to pull the concrete down the wall from where the truck was able to shoot it in. I didn't get a single bow or buckle. I wanted the low slump, because I didn't want the concrete to push out at the bottom while I was filling it at the top.
I'm a big fan of internal vibration. I think where many get into trouble is they pour it too high of a slump and too high of a lift. Jeepster -- you make some very good points. Here are some thoughts to add to your comments: I remain surprised about these "builders" you mention. There are no serious ICF installers that understand what they are doing and care about the results that don't vibrate. Sorry -- but this is a sure way to eventually get into trouble for yourself and/or the industry. As an installer, you can't generally (or shouldn't) control either the slump or the rebar to any great extent. I would add that internal vibration is required for commercial (it's not an opinion) and I wouldn't consider doing "un audited" residential without internal vibration either. What you may have are guys that are using a weak brand of block or not bracing properly. They are several brands out there that can take hard vibration without bulging etc. and you should align with one. What many don't realize is that concrete does not cure properly without vibration even at a high slump -- e.g. air removal was mentioned and proper bond to the rebar, etc. As you stated with the grinder idea--- this might work great for the first course. Where you need to be careful here is that once the first or second course begins to set up and the concrete is beginning to grab the bar then the apparatus will wallow (sp?) out around the lower rebar and create a small void or space all the way around the rebar and for obvious reasons you don't want that. That's part of the reason the frequency of these vibrators is so high. We use a long wand and a short wand (two different vibrators) on every pour. You might use your grinder for the long wand effect if you are confortable that it's doing the trick and then get one of the short internal vibrators (usually around $150 or so) for the top of the wall. Regards. |
|
|
|
|
smartwall
 Veteran Member
 Posts:1197
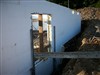
 |
30 Nov 2011 08:36 AM |
|
Accepted practice is 4 foot lifts and somehow Nudura can pour 40 and 35 foot pous in 2 lifts with the concrete magically jumping over the webs. I'm not buying it. The Nudura form has a restrictive web which keeps concrete from flowing as easily as other forms and your telling me that those walls have no voids BS. |
|
|
|
|
Chris Johnson
 Advanced Member
 Posts:877
 |
30 Nov 2011 04:02 PM |
|
I think when he said two lifts he meant 18-20' build and pour, another 18-20' and pour. Not 40' with 2 lifts of concrete at 20' each, that isn't going to work as you said and your correct. I will exceed the 4' max. lift on a 6" wall without concern, but thicker cavities I will not do it for fear of too much pressure around windows and corners creating havoc.
|
|
Chris Johnson - Pro ICF<br>North of 49 |
|
|
Draftman56
 New Member
 Posts:5
 |
30 Nov 2011 05:03 PM |
|
In defence of Texas ICF, Chris has got the right idea. I know he meant 2 successive POURS of concrete each conducted using 4 foot lifts (and vibration) for each pass of concrete placement up to the projected finish pour height. (then build another 18-20 feet and repeat) All of us I'm sure will agree that your 4 foot limit per lift of concrete is correct. Many installers might push pass this limit but to be true to ACI Practices most will concede the text book SAFE limit is typically 4 feet - may be less if temperatures dicate it. |
|
|
|
|
BrucePolycrete
 Advanced Member
 Posts:524
 |
30 Nov 2011 05:21 PM |
|
I hate to keep beating this same old drum, but ACI tables refer to formwork designed to withstand a specific pressure per square foot at a given temperature. I know of only one ICF manufacturer that will tell you what pressure its forms are designed to resist. Polycrete Big Block 1600 withstands 1,600 lbs per sqft of lateral pressure. It has tested much higher, but that is the safe level. ACI tables will tell you that you can comfortably pour 10' per hour when the temperature is 50 degrees. Polycrete knows how strong the other popular products are because Polycrete has tested them. None of the popular residential grade forms -- even ones advertising themselves as "Industrial Strength" come close. |
|
|
|
|